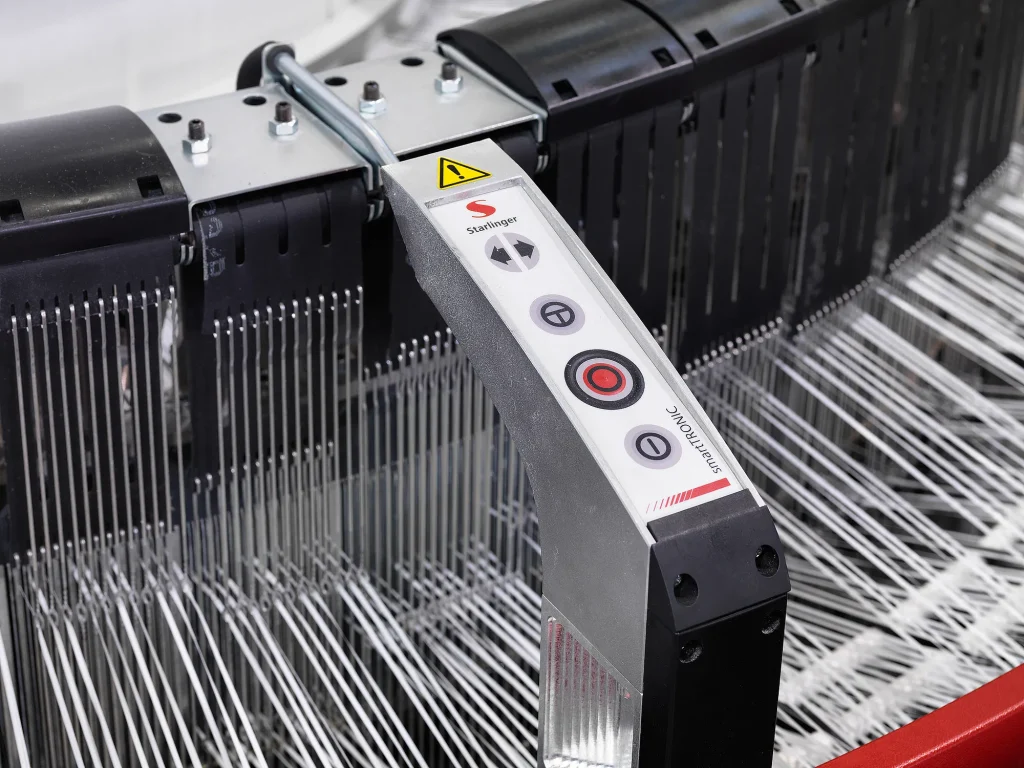
A Client’s Perspective:
Client: “We need packaging that combines durability with high-impact branding. How do your paper valve woven bags achieve this?”
VidePak Sales Representative: “VidePak’s paper valve woven bags integrate advanced fine-yarn weaving technology, 12-color HD printing, and ISO-certified sustainable practices to deliver unmatched strength (up to 50 kg capacity), vibrant branding, and compliance with global environmental standards. With 30+ years of expertise and 100+ production lines, we ensure your products stand out while reducing operational costs by 20–30%.”
1. Fine-Yarn Weaving: The Backbone of Durability and Aesthetics
At the core of VidePak’s paper valve woven bags lies fine-yarn weaving technology, a process that transforms polypropylene (PP) granules into ultra-thin, high-density filaments. Using Austrian Starlinger circular looms, these filaments are interlaced at 14–18 threads per inch, creating a fabric with tensile strengths exceeding 40 MPa—ideal for heavy-duty applications like cement, fertilizers, and construction materials[citation:10].
Technical Breakdown:
- Extrusion: PP granules are melted and extruded into filaments as thin as 40 microns.
- Weaving: Precision looms interlace filaments into a tightly woven matrix, reducing pore sizes by 30% compared to standard weaving.
- Lamination: BOPP films or kraft paper layers are heat-bonded for moisture resistance and printability.
Advantages:
- Load Capacity: Supports up to 50 kg without elongation, outperforming traditional bags by 25%[citation:10].
- Aesthetic Precision: Smoother surfaces enable 1200 DPI printing resolution for photorealistic branding.
- Sustainability: Recyclable PP reduces carbon footprint by 18% vs. virgin plastic.
2. Custom Printing: Elevating Brand Visibility
VidePak’s 30+ printing machines leverage rotary and digital technologies to deliver:
- 12-Color HD Graphics: Pantone-matched designs for logos, safety labels, and multilingual instructions.
- BOPP Lamination: Scratch-resistant surfaces ideal for outdoor storage or retail displays.
- Quick Turnarounds: 20–25 days for custom orders, including design validation.
Case Study: A European agrochemical brand saw a 35% sales increase after switching to VidePak’s UV-resistant printed bags, which maintained color vibrancy after 6 months of outdoor exposure[citation:10].
3. Applications Across Industries
Industry | Key Requirements | VidePak’s Solution |
---|---|---|
Construction | Puncture resistance, cost efficiency | 120 g/m² PP + double-stitched seams |
Agriculture | Moisture barriers, UV protection | BOPP-laminated bags with PE liners |
Chemicals | Chemical resistance, safety labels | Anti-static coatings + HD hazard symbols |
Retail | Brand visibility, eco-friendly | Recycled PP + FSC-certified kraft paper valves |
For instance, a Nigerian fertilizer supplier reduced spillage losses by 22% using VidePak’s valve bags with reinforced seams[citation:10].
4. Sustainability Without Compromise
VidePak’s paper valve bags align with global ESG goals:
- Material Innovation: 30% post-industrial recycled PP blends.
- Certifications: ISO 14001, EU REACH, and FDA-compliant liners.
- Circular Economy: Bags are 100% recyclable, with a 12-month reuse cycle for construction waste transport.
Featured Product: EcoValve™ Paper Valve Bags
- Materials: 70% recycled PP + 30-micron BOPP.
- Capacity: 25–50 kg with heat-sealed valves.
- Customization: RFID tags, QR codes for supply chain tracking.
FAQs: Simplifying Procurement Decisions
Q1: Can bags withstand -20°C temperatures?
A: Yes. Our cold-crack-resistant PP maintains flexibility at -25°C.
Q2: What’s the MOQ for custom designs?
A: 5,000 bags, with volume discounts for orders >50,000 units.
Q3: How do you ensure color accuracy?
A: We use spectrophotometers for Pantone validation and provide pre-production samples.
References
- Global Packaging Institute. (2025). Hybrid Materials in Industrial Packaging.
- VidePak Company Profile. PP Woven Bags Manufacturer. Available at: www.pp-wovenbags.com.
- UN Sustainable Development Group. (2024). Circular Economy Practices in Packaging.
For inquiries, contact: info@pp-wovenbags.com.
Anchor Links:
- Discover how paper valve bags support sustainable logistics.
- Explore BOPP lamination techniques for high-definition branding.
This article synthesizes cutting-edge material science, global compliance insights, and VidePak’s manufacturing prowess to position paper valve woven bags as the optimal choice for brands prioritizing durability, aesthetics, and sustainability.