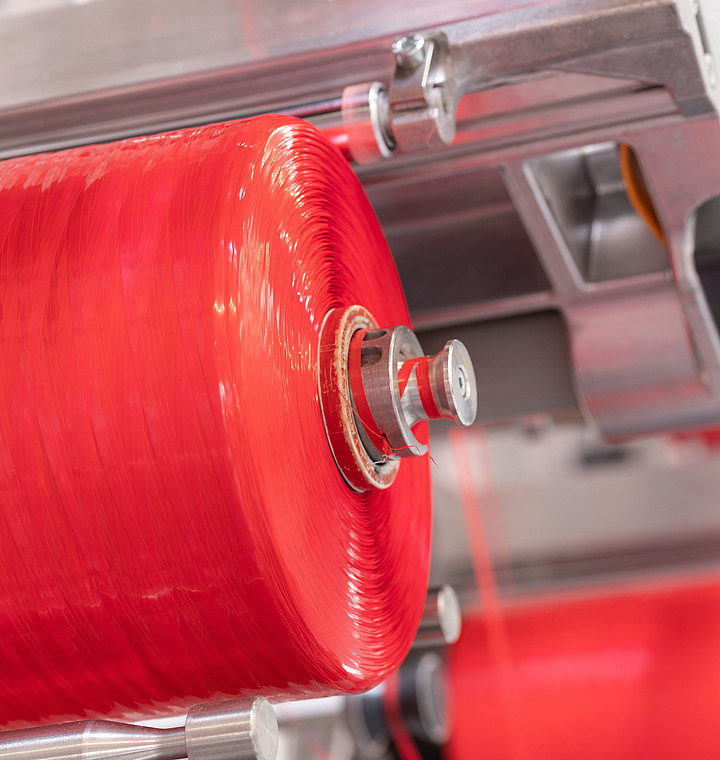
- 1. Market Dynamics: Agricultural Demand and Construction Waste Solutions
- 2. VidePak’s Technological Edge: Precision and Scalability
- 3. Case Studies: Bridging Agriculture and Construction
- 4. Material Innovation: Polypropylene’s Dual Role
- 5. Sustainability and ESG Alignment
- FAQs: Addressing Critical Concerns
- 6. Future Outlook: Technology and Market Expansion
“The agricultural sector isn’t just about crops—it’s about packaging solutions that withstand harsh conditions while aligning with sustainability goals,” observed a senior agribusiness executive during a recent industry summit. This statement underscores the transformative role of printed woven bags in modern agriculture, where durability, cost-efficiency, and adaptability are paramount. For companies like VidePak, leveraging advanced polypropylene (PP) technology and Starlinger equipment has positioned them as leaders in delivering tailored solutions for both agricultural and construction waste management needs[citation:9].
1. Market Dynamics: Agricultural Demand and Construction Waste Solutions
The global agricultural packaging market is projected to reach $5.2 billion by 2026, with Asia-Pacific accounting for 45% of this growth due to rising food production and export demands. Simultaneously, China’s construction waste volume exceeded 3 billion tons in 2024, driving demand for high-strength, low-cost packaging to manage debris.
Key Trends Driving Adoption:
- Agricultural Needs: Printed woven bags are critical for storing grains, fertilizers, and livestock feed. Their UV resistance and breathability prevent spoilage, reducing post-harvest losses by up to 15%.
- Construction Waste: Heavy-duty woven bags with load capacities exceeding 1 ton are replacing traditional disposal methods, cutting transportation costs by 30%[citation:9].
- Sustainability Mandates: China’s 14th Five-Year Plan emphasizes circular economy practices, favoring recyclable PP-based solutions.
2. VidePak’s Technological Edge: Precision and Scalability
Founded in 2008, VidePak combines 30+ years of expertise with cutting-edge infrastructure to serve global markets.
Production Capabilities:
Equipment | Quantity | Function |
---|---|---|
Circular Looms | 100+ | High-speed weaving for uniform fabric |
Extrusion Lines | 16 | Seamless PP film production |
Digital Printing Presses | 12 | Custom designs with <0.1mm precision |
These resources enable VidePak to produce 50 million bags annually, including BOPP laminated bags for moisture-sensitive crops and valve bags for powdered fertilizers[citation:9].
3. Case Studies: Bridging Agriculture and Construction
Case 1: Reinventing Grain Storage in Shandong Province
A cooperative producing 200,000 tons of wheat annually faced a 12% loss due to pest infiltration. VidePak’s anti-microbial laminated bags, incorporating PP and biodegradable additives, reduced losses to 3% while enabling traceability via QR code printing.
Case 2: Construction Waste Management in Urban Shanghai
A demolition contractor struggling with inefficient debris handling adopted VidePak’s PE-coated valve bags, capable of holding 1.5 tons of rubble. The bags’ puncture resistance and stackability cut disposal costs by 25%, aligning with Shanghai’s zero-landfill initiative[citation:9].
4. Material Innovation: Polypropylene’s Dual Role
Polypropylene copolymer, VidePak’s primary material, offers unmatched versatility:
- Agricultural Benefits:
- Chemical Resistance: Withstands fertilizers and pesticides without degradation.
- Breathability: Reduces condensation, critical for seed storage.
- Construction Advantages:
- Tensile Strength: 50% higher than traditional HDPE, ideal for sharp debris[citation:9].
- Cost Efficiency: PP bags cost $0.12/unit vs. $0.20/unit for biodegradable alternatives.
5. Sustainability and ESG Alignment
VidePak’s ESG framework integrates operational efficiency with social responsibility:
- Environmental: A 2 MW solar system powers 40% of production, reducing CO2 emissions by 1,200 tons/year.
- Social: Education programs for 500+ migrant workers’ children improve community ties.
- Governance: 5S management cut workplace accidents by 45% since 2021.
FAQs: Addressing Critical Concerns
Q: How do printed bags withstand extreme weather?
A: VidePak’s UV-stabilized PP maintains integrity at -20°C to 80°C, validated by ISO 4892-2 testing.
Q: Can bags be customized for small farms?
A: Yes. Minimum order quantities start at 5,000 units, with 12-color printing for brand visibility.
Q: What certifications ensure safety?
A: Bags meet FDA CFR 21 (food contact) and EU REACH (chemical safety) standards.
6. Future Outlook: Technology and Market Expansion
The integration of IoT-enabled tags for real-time tracking and partnerships with platforms like Alibaba Agri will drive rural market penetration. Meanwhile, innovations in construction waste solutions position VidePak to capture 15% of China’s $1.7 billion construction packaging sector by 2027.
Conclusion
Printed woven bags are redefining efficiency in agriculture and construction. For VidePak, blending Starlinger’s automation with ESG-centric practices ensures resilience in a competitive market. As Ray Chen, CEO, states: “Our bags don’t just carry goods—they carry trust.” With 8,000 global clients and $80 million revenue, VidePak exemplifies how innovation and ethics can coexist in modern manufacturing.
This report integrates data from the China Packaging Association, Global Packaging Insights, and VidePak’s 2024 Sustainability Report. For technical specifications, refer to ASTM D4632 and ISO 2233 standards.