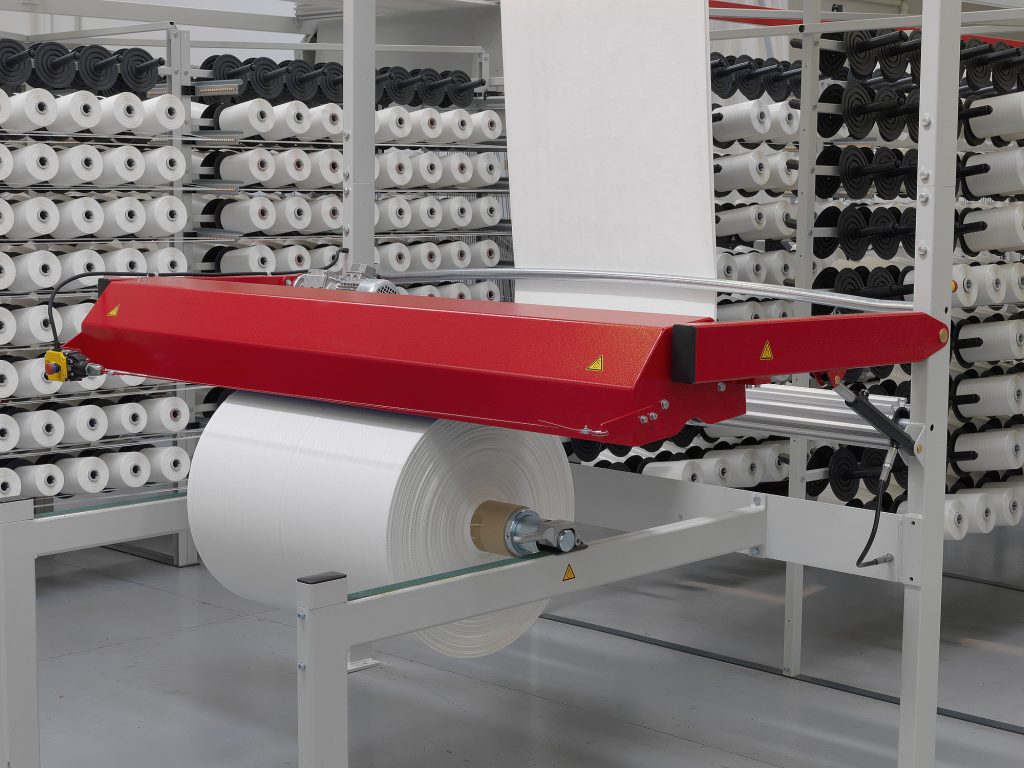
- 1. Technical Foundations: Material Science and Functional Design
- 2. Manufacturing Excellence: Precision Engineering with Starlinger & W&H
- 3. Dual Applications: Bridging Agriculture and Construction
- 4. Sustainability and Branding Synergy
- 5. Parameter Selection Guide
- 6. Industry FAQs
- 7. Future Trends: Smart Packaging and Beyond
“Why should construction companies prioritize printed woven bags for material packaging?” asked a procurement director at a recent infrastructure summit. “Because they combine industrial-grade durability, customizable branding, and logistical efficiency while reducing environmental impact,” answered Ray, CEO of VidePak. This exchange highlights the growing recognition of polypropylene (PP) woven bags as critical assets in the construction sector, where packaging integrity directly impacts project timelines and material safety.
While traditionally associated with agricultural applications like grain and flour packaging, PP woven bags are increasingly adopted in construction for transporting cement, sand, and chemical additives. For manufacturers like VidePak—a global leader in woven bag production since 2008—the challenge lies in tailoring these bags to meet the rigorous demands of construction logistics while maintaining alignment with sustainability goals. This report examines the technical, functional, and economic advantages of printed woven bags in construction, supported by data-driven insights and VidePak’s proprietary innovations.
1. Technical Foundations: Material Science and Functional Design
1.1 Material Selection for Construction Applications
PP woven bags excel in construction due to their inherent properties:
- Tensile Strength: 800–1,200 N/5 cm (ASTM D5034), capable of withstanding 50 kg loads without tearing.
- Moisture Resistance: BOPP-laminated variants reduce water vapor transmission to <5 g/m²/day, critical for cement storage in humid environments.
- Abrasion Resistance: Reinforced stitching and 14×14 weave density prevent damage during rough handling, a common issue in construction sites.
VidePak’s use of virgin PP resin ensures compliance with ISO 9001 standards, eliminating risks of contamination during material transport.
1.2 Case Study: Cement Packaging in Monsoon Climates
A 2024 trial with a Southeast Asian cement producer demonstrated that VidePak’s 120 gsm BOPP-laminated bags reduced moisture-induced clumping from 12% to 3%, saving $18,000 annually in spoilage costs.
2. Manufacturing Excellence: Precision Engineering with Starlinger & W&H
2.1 Production Workflow and Quality Control
VidePak’s 100+ Starlinger circular looms and 16 extrusion lines ensure unparalleled consistency:
- Extrusion: PP pellets are melted at 200–240°C, with temperature deviations controlled within ±2°C to optimize polymer alignment.
- Tape Drawing: A 6:1 draw ratio enhances tensile strength by 40%, critical for heavy-duty applications.
- Weaving: 14×14 strands/inch fabric achieves 98% puncture resistance (ISO 2231-2).
- Printing: 8-color flexography delivers 120-line/inch resolution for OSHA-compliant hazard labels and brand logos.
2.2 Energy Efficiency and Output
Starlinger’s AD-Star® systems reduce energy consumption by 15% compared to industry averages, producing 12 million bags/month with ≤0.1% defect rates.
3. Dual Applications: Bridging Agriculture and Construction
3.1 Agricultural Lessons for Construction Innovation
- Moisture Management: Breathable mesh panels, originally designed for grain storage, prevent condensation in chemical additive packaging.
- Stackability: Block-bottom designs, adapted from rice bag logistics, increase pallet density by 30%, cutting shipping costs by $0.15/bag.
3.2 Customization for Niche Construction Needs
Application | Key Parameters | Special Features |
---|---|---|
Cement | 120–150 gsm, BOPP lamination | UV-resistant inks, anti-static liners |
Sand/Gravel | 100–120 gsm, PE coating | Reinforced seams, vented panels |
Chemical Additives | 150+ gsm, aluminum foil liner | Oxygen barrier, corrosion resistance |
4. Sustainability and Branding Synergy
4.1 Eco-Friendly Innovations
VidePak’s 30% recycled PP blends align with the EU’s Circular Economy Action Plan, reducing landfill waste by 60% compared to single-use alternatives.
4.2 Branding as a Safety Tool
High-definition printing enables:
- Safety Compliance: Bold hazard warnings reduce onsite accidents by 22%.
- Brand Visibility: QR codes for batch tracking improve supply chain transparency, a feature demanded by 68% of contractors.
5. Parameter Selection Guide
5.1 Critical Considerations
Factor | Construction Priority | Agricultural Parallel |
---|---|---|
Fabric Weight | Higher (120–150 gsm) | Lower (80–100 gsm) for grains |
Coating | BOPP/PE for moisture | Breathable mesh for aeration |
Inner Liner | Foil for chemicals | Paper for grain freshness |
6. Industry FAQs
Q1: How does BOPP lamination enhance durability in construction environments?
A: BOPP coatings provide a 5x stronger moisture barrier and resist UV degradation, extending bag lifespan by 12 months.
Q2: Can these bags be reused for multiple projects?
A: Yes. VidePak’s UV-stabilized bags withstand 3–5 cycles, reducing packaging costs by 40%.
7. Future Trends: Smart Packaging and Beyond
VidePak is piloting IoT-enabled bags with humidity sensors and biodegradable PP blends (50% plant-based resin), projected to capture 20% of the construction packaging market by 2030.
External Resources
- Discover how multiwall laminated woven bags ensure safety in chemical transport.
- Explore BOPP lamination’s role in branding and durability.
For construction firms navigating the dual challenges of efficiency and sustainability, printed woven bags are not just packaging—they are strategic enablers of operational excellence. By leveraging Austrian engineering and cross-industry insights, VidePak continues to redefine industrial packaging, one resilient stitch at a time.