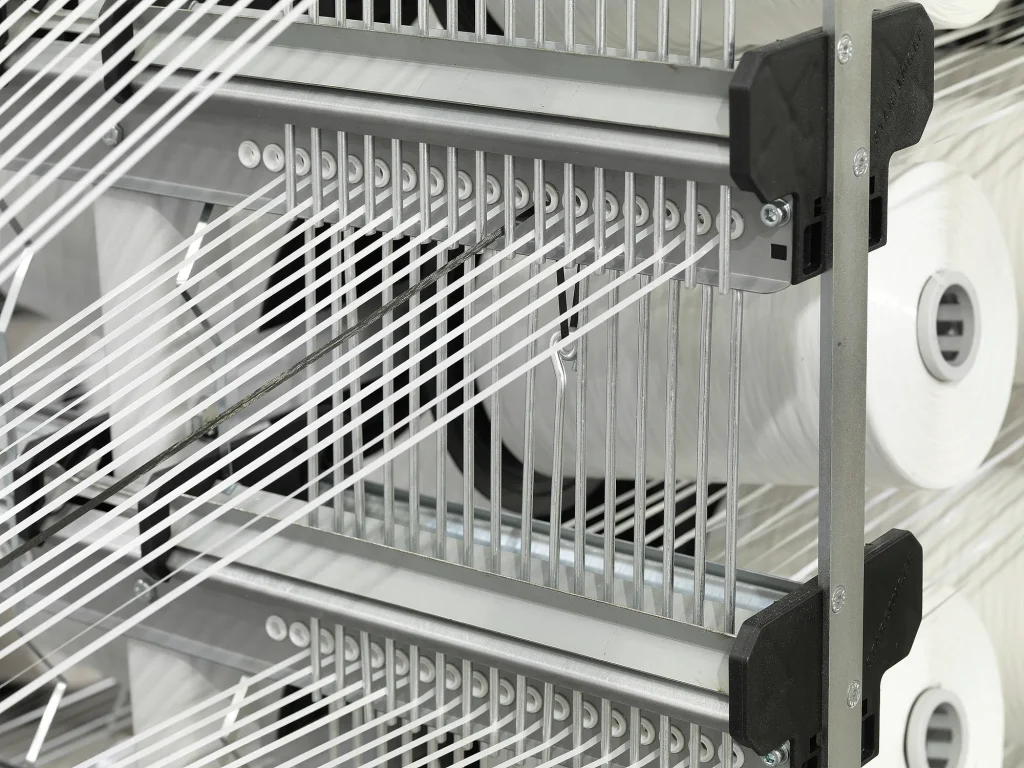
The global valve bag market is projected to grow at a CAGR of 5.2% by 2030, driven by increasing demand for efficient, eco-friendly, and industry-specific packaging solutions. At VidePak, we combine 30+ years of expertise with cutting-edge technology to deliver valve bags that prioritize recyclability, biodegradability, and hyper-customization for sectors ranging from agriculture to construction.
1. The Evolution of Valve Bags: From Functionality to Sustainability
Valve bags, designed for seamless filling and dust-free dispensing, have become indispensable in industries requiring precision and safety. However, modern challenges demand more than functionality—sustainability is now non-negotiable. VidePak addresses this through:
- Recyclable PP Materials: Our valve bags use 100% virgin polypropylene (PP) woven fabric, compatible with global recycling streams. For instance, our BOPP laminated valve bags achieve tensile strengths of 35–50 N/cm², ensuring durability while remaining fully recyclable.
- Biodegradable Additives: Partnering with material scientists, we integrate oxo-degradable additives that break down PP into harmless biomass under UV exposure, aligning with EU Directive 2019/904[citation:18].
- Lightweighting: By optimizing fabric density (40–200 g/m²), we reduce material use by up to 20% without compromising load capacity (up to 50 kg).
Case Study: A fertilizer manufacturer reduced its carbon footprint by 15% after switching to VidePak’s 90 g/m² biodegradable valve bags, customized with 6-color gravure printing for brand visibility.
2. Customization: Tailoring Valve Bags to Industry-Specific Needs
Valve bags are not one-size-fits-all. VidePak’s 100+ circular looms and 30 lamination machines enable precision customization:
Key Customization Parameters
Parameter | Options | Industry Application |
---|---|---|
Material | PP woven, BOPP laminated, Kraft paper composite | Chemicals (BOPP for moisture resistance), Food (Kraft paper FDA compliance)[citation:28] |
Printing | Up to 8 colors, flexo/gravure/screen | Agriculture (brand logos), Pharmaceuticals (safety instructions) |
Valve Type | Pasted, block-bottom, inflatable | Construction (block-bottom for fine powders), Food (inflatable for liquid retention)[citation:23] |
Lining | PE film, aluminum foil, non-woven | Petrochemicals (foil for static resistance), Animal feed (PE for moisture control) |
Example: For a Southeast Asian rice exporter, we developed BOPP laminated bags with 150D yarn density and PE liners, reducing spillage during maritime transport by 40%.
3. Future Trends: Where Innovation Meets Demand
A. Circular Economy Integration
- Closed-Loop Recycling: VidePak’s collaboration with European recyclers ensures 70% of post-consumer PP is reprocessed into new bags[citation:44].
- Bio-Based PP: Pilot projects using sugarcane-derived PP aim to cut fossil fuel dependency by 50% by 2027[citation:37].
B. Smart Packaging
RFID tags and QR codes are being embedded into valve bags for real-time tracking in pharmaceutical and high-value cargo supply chains[citation:50].
C. Regulatory Compliance
With stricter EU and US regulations on single-use plastics, our ISO 22000-certified production lines guarantee compliance, including REACH and FDA standards[citation:28].
4. VidePak’s Technical Edge
- Production Capacity: 300,000 bags/day, supported by 16 extrusion lines and 30 printing machines.
- Certifications: ISO 9001, ISO 22000, BRCGS[citation:28].
- Global Reach: Serving 85+ countries, with dedicated R&D teams in Germany and China.
FAQs: Addressing Procurement Concerns
Q1: What is the MOQ for customized valve bags?
A: VidePak’s MOQ starts at 10,000 bags, with bulk discounts for orders exceeding 100,000 units.
Q2: How do biodegradable bags compare in cost?
A: Biodegradable options cost 10–15% more than standard PP bags but offer long-term savings through regulatory compliance and brand equity.
Q3: Can valve bags withstand tropical climates?
A: Yes. Our UV-stabilized BOPP laminated bags maintain integrity at 90% humidity and 40°C.
Conclusion
Valve bags are no longer mere containers—they are strategic assets driving sustainability and efficiency. VidePak’s commitment to innovation, customization, and compliance positions us as the partner of choice for forward-thinking industries. Explore our BOPP laminated valve bags and eco-friendly woven solutions to elevate your packaging strategy.
References
- VidePak Company Profile (2025). PP Woven Bags Production and Sustainability Report.
- GlobalTextiles.com. PP/PE Woven Bags: Technical Specifications (2024).
- Made-in-China. Plastic Rice Bag BOPP Rice Bags PP Woven Laminated Bag (2015).
Contact VidePak:
- Website: https://www.pp-wovenbags.com/
- Email: info@pp-wovenbags.com