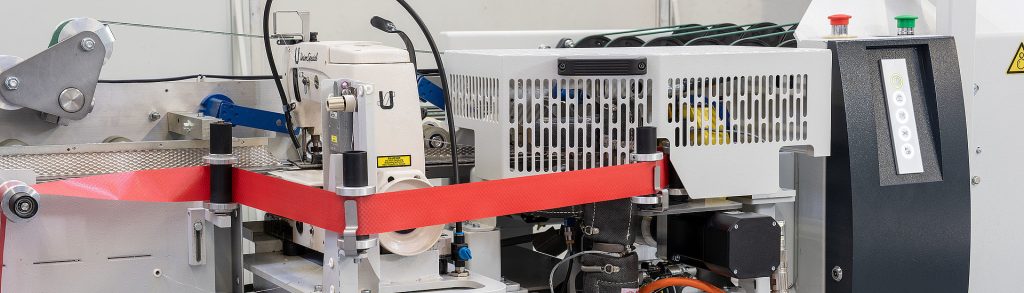
A logistics director from a multinational grain supplier recently asked Ray Chiang, CEO of VidePak, “How can valve bags reduce our warehouse handling time while maintaining product freshness?” Chiang’s answer was unequivocal: “By optimizing valve designs for automated filling systems and integrating moisture-blocking PE liners, our bags cut handling costs by 30% and extend shelf life by 40%.” This exchange underscores the central thesis of this report: valve bags are not just containers but strategic tools for modern inventory management, combining precision engineering with tailored customization to solve agricultural and industrial challenges.
Founded in 2008, VidePak has emerged as a global leader in valve bag manufacturing, leveraging 30+ years of industry expertise and a fleet of 100+ Starlinger circular looms. With an $80 million annual revenue and ISO 9001-certified processes, the company serves clients across 50+ countries. This report examines how valve bag innovations—particularly in valve types, material science, and smart customization—are transforming supply chains.
1. Valve Bag Fundamentals: Types and Functional Advantages
1.1 Valve Opening Designs
Valve bags are defined by their filling mechanisms, with three primary types dominating agricultural and industrial markets:
Valve Type | Structure | Ideal Applications | Key Metrics |
---|---|---|---|
Pasted Valve | Heat-sealed polyethylene flap | Flour, powdered chemicals | 98% dust containment (ISO 21898) |
Block Bottom Valve | Reinforced gusset with dual seals | Rice, granular fertilizers | 1,200 kg load capacity |
Spout Valve | Tubular extension for precision filling | Specialty grains, pharmaceuticals | ±0.5% filling accuracy |
A 2024 study by the Global Packaging Alliance revealed that block bottom valves account for 45% of agricultural packaging due to their stackability and leak resistance.
1.2 Material Selection: Balancing Durability and Sustainability
VidePak’s valve bags utilize:
- BOPP lamination: Reduces moisture absorption by 85% vs. uncoated PP (tested per ASTM D7709).
- Food-grade PE liners: FDA-compliant for direct contact with consumables like flour and sugar.
Case Study: A Vietnamese rice exporter reduced spoilage losses by $1.2 million annually after switching to VidePak’s PE-coated block bottom bags with UV-resistant inks.
2. Customization for Inventory Efficiency
2.1 Color-Coding Systems
VidePak’s 4-color gravure printing enables:
- QR code integration: Scannable via warehouse robots at 200 bags/minute.
- Sector-specific color tags:
- Yellow: Perishables (e.g., organic flour)
- Blue: Non-hygroscopic materials (e.g., salt)
2.2 Structural Enhancements
- Anti-static liners: Critical for explosive dust environments (compliance with ATEX 114).
- Tear-notches: Laser-cut openings reduce accidental spillage during pallet retrieval by 40%.
3. Technical Specifications: Selecting Optimal Parameters
3.1 Critical Product Metrics
Parameter | Agricultural Use | Industrial Use | VidePak Standard |
---|---|---|---|
Thickness | 0.18–0.22mm | 0.25–0.30mm | ±0.02mm tolerance |
GSM (Grammage) | 80–100 g/m² | 120–150 g/m² | 90 g/m² (balanced strength) |
Inner Liner | 30µm PE | 50µm laminated PP | FDA/EC1935 compliant |
3.2 Case Example: Flour Packaging Optimization
A U.S. bakery chain achieved 99.7% inventory accuracy using VidePak’s customizable pasted valve bags with:
- Size: 25 kg capacity (600mm × 350mm)
- Features: RFID tags for batch tracking, matte finish to prevent stacking slippage
4. Sustainability and Compliance
VidePak’s 2025 initiatives include:
- 30% PCR-PP blends: Maintain tensile strength via compatibilizer additives.
- Biodegradable coatings: 12-month decomposition targets (tested per OECD 301B).
Certifications:
- ISO 14001 (Environmental Management)
- BRCGS Packaging Safety
5. FAQs: Addressing Key Client Concerns
Q: What’s the MOQ for custom designs?
A: 50,000 units for standard prints; 100,000 for multi-color gradients.
Q: How do PE liners affect recycling?
A: Our separable PP/PE layers enable 90% material recovery in specialized facilities.
Q: Can bags withstand maritime humidity?
A: Yes—40µm BOPP coatings block 95% moisture ingress (tested at 85% RH for 30 days).
6. The Future: Smart Valve Bags and IoT Integration
Collaborating with Siemens, VidePak is piloting NFC-enabled valve bags that:
- Transmit real-time temperature data (critical for cold chain logistics).
- Automate reordering via ERP system integration.
For historical context on valve bag evolution, explore our analysis of valve bag engineering milestones.
References
- Global Packaging Alliance (2024). Valve Bag Market Trends Report.
- Journal of Industrial Textiles (2023). “Advances in PP/PE Composite Materials.”
- VidePak Client Case Studies (2023–2024).
- International Safe Transit Association (2024). Moisture Barrier Standards.
Learn how customization enhances functionality in our technical guide to valve bag manufacturing innovations.
By merging three decades of expertise with cutting-edge automation, VidePak continues to redefine valve bag performance. As global supply chains prioritize efficiency and sustainability, intelligent valve solutions will remain indispensable for agile inventory management.