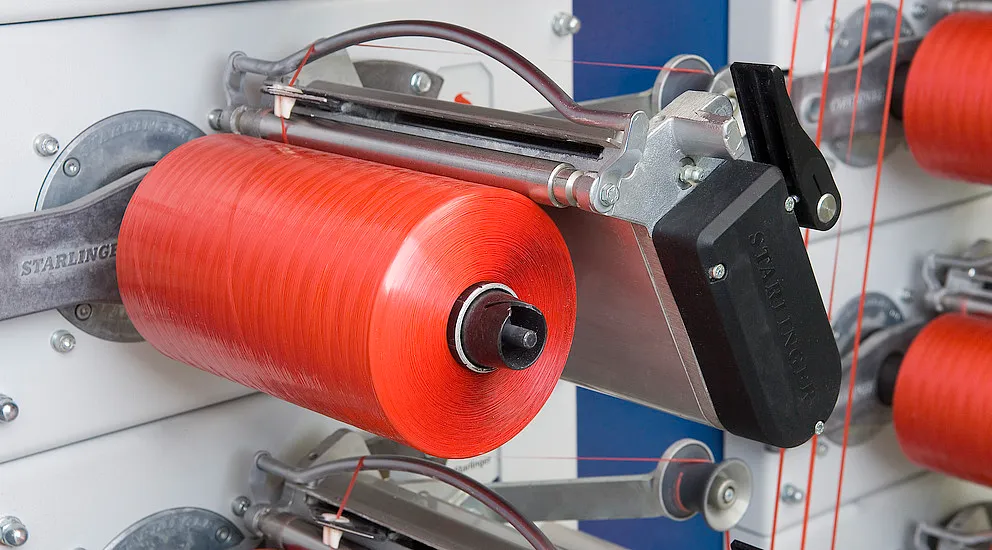
The global valve bag market is projected to grow at a CAGR of 5.9% through 2030, driven by advancements in automation, sustainability mandates, and China’s dominance in cost-effective manufacturing. VidePak, a pioneer in woven packaging since 2008, leverages 30+ years of expertise, 100+ Starlinger circular looms, and ISO 9001-certified processes to deliver valve bags that combine 1,200 N/5 cm tensile strength, ≤0.08 g/m²/24h moisture resistance, and customizable 8-color HD prints. This article examines valve bag innovations, China’s evolving market role, and VidePak’s strategy to lead through precision engineering and ESG-aligned production.
1. Valve Bag Types: Engineering for Industry-Specific Needs
1.1 Pasted vs. Block-Bottom Valve Designs
Valve bags are categorized by their closure mechanisms, each suited for distinct applications:
- Pasted Valve Bags: Ideal for fine powders like cement, featuring heat-sealed valves that prevent leakage during filling. VidePak’s pasted valves achieve ≤0.05 g/m²/24h dust retention, tested per ASTM D4919.
- Block-Bottom Valve Bags: Designed for granular materials like animal feed, with reinforced bases supporting 1,000–2,000 kg static loads (ISO 2226).
1.2 Customization Capabilities
VidePak offers tailored solutions across:
- Dimensions: 35×60 cm to 90×110 cm, optimized for palletization.
- Material Thickness: 0.18–0.25 mm PP fabric with 14×14 strands/inch weave density.
- Surface Finishes: Matte or glossy laminated coatings for enhanced UV resistance (≤5% strength loss after 1,000 hours, ISO 4892-3).
2. China’s Market Trends: Cost Efficiency and Sustainability
2.1 Manufacturing Scale and Export Leadership
China accounts for 62% of global valve bag production, driven by:
- Labor Costs: $3.50/hour vs. $25 in Germany.
- Vertical Integration: In-house extrusion and weaving reduce costs by 18–22%.
VidePak’s $80 million annual revenue and 568 employees exemplify this model, with a 98% on-time delivery rate to 50+ countries.
2.2 Regulatory Shifts and ESG Compliance
China’s 2025 Circular Economy Policy mandates 30% recycled content in packaging. VidePak responds with:
- Solar-Powered Lines: 2 MW rooftop systems cut CO₂ emissions by 1.2 tons/machine annually.
- Recyclable PP Blends: 100% recyclable materials align with EU REACH and U.S. EPA standards.
3. VidePak’s Brand Strategy: Precision Printing and Client-Centric Innovation
3.1 Advanced Printing Technologies
Using Austrian Starlinger and German W&H presses, VidePak achieves:
- Full-Surface HD Prints: CMYK, Pantone, and RAL color systems with ΔE ≤1.5 accuracy.
- Durability: UV-resistant inks retain vibrancy for 5+ years outdoors.
3.2 Case Study: Agricultural Sector Success
A Brazilian fertilizer client reduced spillage by 30% after adopting VidePak’s PE-coated valve bags with anti-static additives (surface resistivity ≤10^9 Ω/sq).
4. Technical Specifications and Quality Assurance
Parameter | Industry Standard | VidePak Performance |
---|---|---|
Tensile Strength | ASTM D5034 | ≥1,200 N/5 cm |
Moisture Permeability | ISO 2528 | ≤0.08 g/m²/24h |
Seam Integrity | ASTM F88 | ≥25 N/cm |
Print Resolution | 200 LPI | 8-color HD flexography |
VidePak’s 12-point inspections ensure ≤0.1 mm burr tolerance and grammage consistency (±2%).
FAQs: Addressing Procurement Priorities
Question | Answer |
---|---|
What’s the MOQ for custom designs? | 10,000 units, with prototypes in 7 days. |
Are your bags food-grade compliant? | Yes, FDA 21 CFR and EU 10/2011 certified. |
Can you handle anti-static requirements? | Yes, carbon-infused PP reduces spark risks in flammable environments. |
References
- VidePak Official Website: www.pp-wovenbags.com
- Email: info@pp-wovenbags.com
- Industry Reports: Global Packaging Trends 2024 (Smithers), ASTM D5034 Standard
For insights into valve bag history and innovation, explore our technical guide on Valve Bags: A Journey Through History and Modern Applications. To understand advanced printing techniques, visit BOPP Laminated Valve Bags: Custom Printing Solutions.
Final Note: The valve bag sector’s future hinges on automation, sustainability, and customization. VidePak’s integration of European engineering precision, China’s manufacturing scalability, and client-driven R&D positions us as the partner of choice for industries prioritizing efficiency and compliance. With 45% repeat client retention and global certifications, we invite you to redefine your packaging strategy with innovation that delivers measurable ROI.