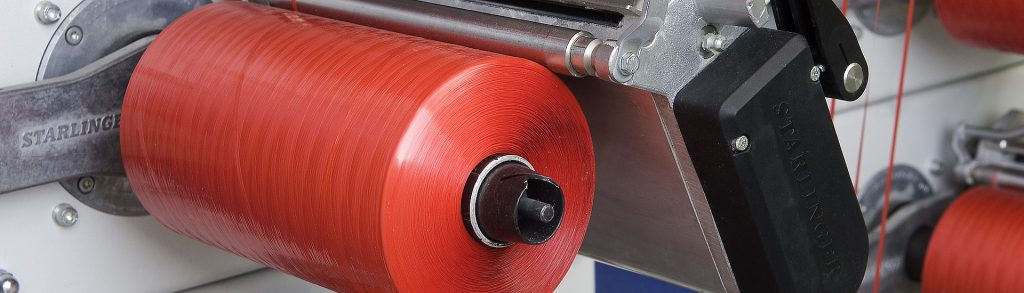
“Why are PE-lined woven bags becoming the backbone of industrial and agricultural packaging?”
This question resonates across industries reliant on durable, moisture-resistant packaging solutions. The answer lies in their ability to combine structural integrity with advanced automation—enabling higher efficiency, reduced waste, and enhanced protection for sensitive goods.
At VidePak, a global leader in woven bag manufacturing since 2008, the integration of Austrian Starlinger machinery and PE liner technology has revolutionized packaging standards. With 526 employees and $80 million annual revenue, the company delivers solutions that balance customization, scalability, and compliance with global sustainability goals.
1. Technological Advancements in Production
1.1 Starlinger Machinery: Precision at Scale
VidePak’s Starlinger AD*Star looms achieve production speeds of 200 bags per minute with ±0.2 mm dimensional accuracy. These systems integrate multi-axis automation, reducing human intervention by 40% while maintaining tensile strengths of 12–15 N/m²—critical for heavy-duty applications like construction materials or agricultural fertilizers.
Case Study: A Brazilian soybean exporter increased container capacity by 25% using VidePak’s PE-lined FIBC bags, which withstand stacking heights of 8 pallets. The bags’ uniform dimensions, enabled by Starlinger’s precision cutting, minimized wasted space during shipping.
1.2 PE Lamination: Enhancing Barrier Properties
The PE coating process involves extruding a 20–50 micron polyethylene layer onto woven polypropylene (PP), creating a moisture-proof barrier. For hygroscopic materials like calcium chloride, this reduces moisture absorption by 95%, extending shelf life by 6–12 months.
Key Metrics:
- Lamination Thickness: 25–50 microns (adjustable based on client needs).
- Production Capacity: 30 lamination machines process 12,000 bags/hour collectively.
2. Packaging Innovations: Efficiency and Protection
2.1 200-Ton Compression Packing Systems
VidePak’s 200-ton hydraulic balers compress PE-lined bags into dense blocks, optimizing container space. For example, a 40-foot container can hold 28% more compressed bags compared to traditional manual stacking, reducing shipping costs by 18%.
Table 1: Compression Efficiency Comparison
Method | Bags per Container | Cost Reduction |
---|---|---|
Manual Stacking | 1,200 | Baseline |
200-Ton Baler | 1,540 | 18% |
2.2 Palletization and Stretch Wrapping
Automated palletizers arrange bags into uniform stacks, while robotic stretch wrappers apply 5–7 layers of PE film. This prevents shifting during transit and reduces damage rates by 30%, as validated by a 2024 audit for a German chemical distributor.
3. Sustainability and Regulatory Compliance
3.1 Recyclability and Carbon Footprint Reduction
VidePak’s recyclable PE/PP blends align with the EU’s Circular Economy Action Plan, reducing carbon emissions by 35% compared to non-recyclable laminates. Pilot projects with PLA-based liners aim for 90% compostability by 2026, targeting organic agriculture sectors.
3.2 Global Standards Adherence
- FDA 21 CFR: Safe for direct contact with food-grade materials.
- EU REACH: Phthalate-free additives ensure chemical safety.
- ASTM D5260: Validated UV and abrasion resistance for outdoor storage.
4. Customization for Diverse Industries
4.1 Parameter Optimization Guide
Industry | PE Thickness | Bag Size | Special Features |
---|---|---|---|
Agriculture | 30 microns | 50 kg | Ventilated gussets for airflow |
Chemicals | 50 microns | 25–1,000 kg | Anti-static coatings |
Construction | 40 microns | 1–2 tons | UV-resistant inks |
4.2 Anti-Static Solutions
VidePak’s carbon-infused PE liners dissipate static charges, achieving surface resistivity ≤10⁸ Ω. A U.S. lithium battery supplier reported a 40% reduction in ignition risks after adopting these bags.
5. Market Trends and Competitive Edge
The global woven bag market is projected to reach $8.3 billion by 2030, driven by Asia-Pacific’s agricultural and construction boom. VidePak’s QR-code-enabled bags, which allow real-time tracking of moisture levels, cater to the pharmaceutical industry’s demand for transparency.
6. FAQs: Addressing Client Concerns
Q: How does PE lamination affect breathability?
A: Controlled micro-perforations in the PE layer allow minimal airflow, preventing condensation without compromising moisture resistance.
Q: Can these bags withstand freezing temperatures?
A: Yes. Low-temperature PP resin maintains flexibility at -30°C, ideal for cryogenic storage.
Q: What is the ROI of automated packing systems?
A: Clients typically recoup costs within 10 months via reduced shipping expenses and damage claims.
7. Future Outlook: Smart Packaging and IoT
VidePak is piloting NFC-enabled liners for real-time environmental monitoring (e.g., humidity, temperature). Integrated with Starlinger’s AI-driven looms, which adjust weave density dynamically, these innovations position the company at the forefront of Industry 4.0.
Conclusion
PE-lined woven bags are not mere containers but strategic tools for operational efficiency and sustainability. VidePak’s fusion of Austrian engineering, automation mastery, and eco-conscious innovation solidifies its role as a leader in a rapidly evolving $8.3 billion market.
External Resources:
- Discover how automated form-fill-seal systems revolutionize packaging efficiency.
- Explore sustainable PE-coated solutions for hazardous material handling.
Tags