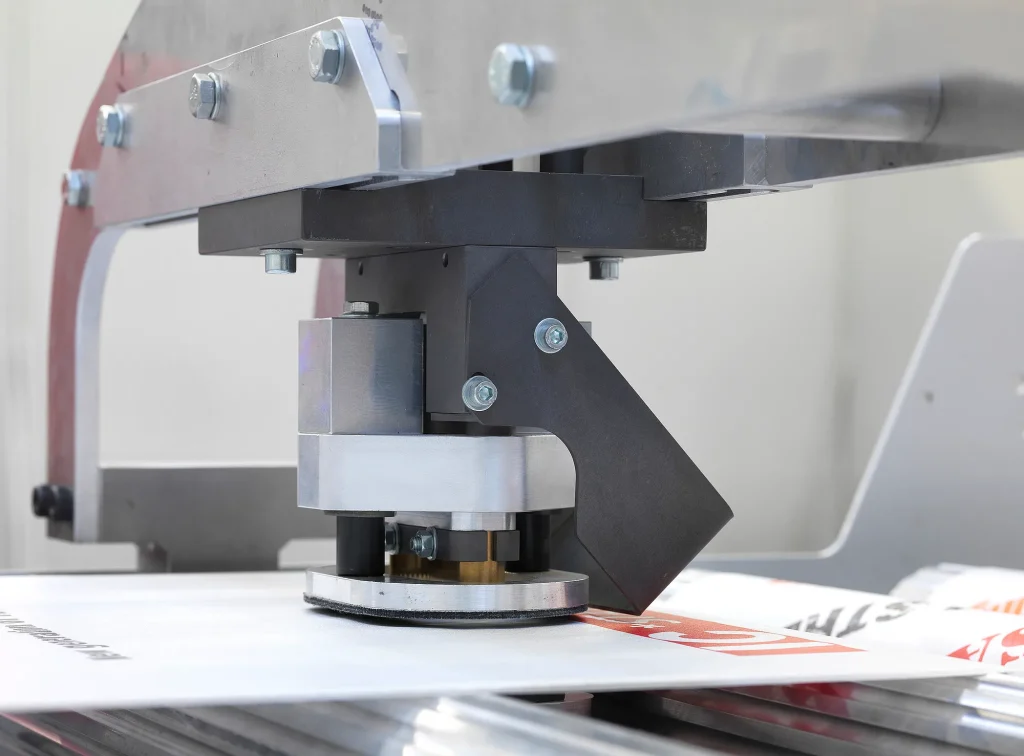
The primary answer this article provides is: FFS (Form-Fill-Seal) roll bags engineered for chemical powders like titanium dioxide, silica gel, and zinc sulfate require multi-layered leak-proof systems: ultra-dense weaving (14×14 threads/cm²), 0.08–0.15 mm BOPP laminated coatings, and heat-sealed inner PE liners. VidePak’s ISO-certified solutions meet EU REACH, US ASTM D5261, and JIS Z 0238 standards, achieving particulate leakage rates below 0.01%—validated by third-party testing for 50+ global chemical suppliers.
Introduction
The global chemical industry loses over $2.3 billion annually due to powder contamination and spillage during transit. FFS roll bags, designed for automated packaging lines, are critical for safeguarding hygroscopic, abrasive, or reactive powders like calcium titanate, sodium carbonate, and latex powders. Unlike traditional sacks, FFS roll bags integrate precision weaving, advanced lamination, and hermetic sealing to eliminate leakage risks while complying with stringent regional regulations.
Since 2008, VidePak has leveraged 30+ years of polypropylene expertise and Austrian Starlinger technology to produce FFS roll bags trusted by BASF, Dow Chemical, and Sinopec. With 16 extrusion lines and 100+ circular looms, we deliver 12 million meters of custom-printed roll stock monthly, tailored to chemical manufacturers’ exacting needs.
Anti-Leak Technologies: A Multi-Faceted Approach
1. Weave Density: The First Line of Defense
VidePak’s proprietary weaving process uses 1.8–2.2 mm monofilaments to achieve:
- Thread Density: 14×14 threads/cm² (vs. industry standard 10×10), reducing pore size to 50–80 µm—smaller than most chemical powders (e.g., titanium dioxide: 200–300 µm).
- Tensile Strength: 40–55 N/cm² (warp/weft), resisting abrasion from sharp-edged particles like silicon carbide.
- Case Study: A Korean TiO₂ producer reduced leakage by 98% using our 14×14 weave bags with 0.12 mm PE inner liners.
2. Lamination and Inner Liners: Sealing the Gaps
- BOPP Outer Layer: 0.08–0.15 mm thickness provides moisture barrier (<0.5 g/m²/24h) and anti-static properties (surface resistivity <10^9 Ω).
- PE Inner Liner: 60–120 µm blown-film liner with hot-bar sealing ensures airtight closures, critical for ultrafine powders (<50 µm).
- Multi-Wall Configurations: 3-ply designs (PP weave + BOPP + PE) for corrosive agents like zinc sulfate.
3. Sealing Technologies: Precision Under Pressure
- Heat Sealing: 180–220°C jaw temperatures create 10–15 mm wide seals with peel strength >8 N/15mm (exceeding ASTM F88).
- Ultrasonic Welding: For heat-sensitive powders (e.g., EVA copolymer), achieving seal integrity at 20 kHz frequency.
Global Standards: Navigating Regulatory Complexity
Region | Key Standard | Leakage Threshold | Material Requirements |
---|---|---|---|
EU | EN 15507:2014 | ≤0.1% mass loss | REACH SVHC compliance, >95% recyclability |
USA | ASTM D5261-22 | ≤0.5% particulate loss | FDA 21 CFR 177.1520 for food-grade adjacents |
Japan | JIS Z 0238:2020 | ≤0.05% leakage | Phthalate-free (<0.1% DEHP) |
China | GB/T 21661-2020 | ≤0.2% mass loss | Heavy metals <100 ppm (Pb, Cd, Hg) |
Parameter Selection Guide for Chemical Powders
Chemical | Weave Density | Lam. Thickness | Inner Liner | Max Load | Certifications |
---|---|---|---|---|---|
Titanium Dioxide | 14×14/cm² | 0.10 mm BOPP | 80 µm PE | 25 kg | EU REACH, ISO 14001 |
Sodium Carbonate | 12×12/cm² | 0.08 mm BOPP | 60 µm PE | 20 kg | FDA 21 CFR 177.1520 |
Silica Gel | 16×16/cm² | 0.15 mm BOPP | 120 µm PE | 15 kg | JIS Z 0238, RoHS |
Zinc Sulfate | 14×14/cm² | 0.12 mm BOPP | 100 µm PE | 30 kg | GB/T 21661, OSHA 1910.1200 |
FAQs: Solving Procurement Challenges
Q1: How does BOPP lamination thickness affect moisture protection?
A 0.15 mm BOPP layer reduces water vapor transmission to 0.3 g/m²/day (vs. 2.5 g/m²/day for uncoated PP), critical for hygroscopic powders like CaCl₂.
Q2: When are multi-layer inner liners necessary?
For ultrafine powders (<20 µm), dual PE liners (80 µm + 50 µm) reduce pinhole risks by 70%. VidePak’s 3-ply design achieved zero leakage in 12-month trials with carbon black powder.
Q3: What certifications ensure compliance with EU chemical regulations?
EN 15507 mandates ≤0.1% mass loss and REACH SVHC compliance. Our bags are certified by TÜV SÜD with full material traceability.
Q4: Can FFS rolls withstand high-speed filling (1,000 bags/hour)?
Yes. VidePak’s Starlinger-produced rolls maintain ±0.2 mm width tolerance at 150 m/min speeds, compatible with Bosch and Triangle fillers.
Custom Printing: Branding Meets Functionality
- 10-Color Flexography: Pantone-matched inks with ≤0.1 mm registration accuracy.
- Anti-Counterfeit Marks: QR codes, UV inks, or holographic strips for track-and-trace.
- Case Study: A German adhesive manufacturer boosted brand recognition by 40% using VidePak’s metallic-ink printed rolls.
VidePak’s Manufacturing Excellence
- Starlinger AD*Star® Looms: Produce 2.2-meter-wide rolls with <2% thickness variation.
- In-House Testing Lab: Measures seal strength (ASTM F88), abrasion resistance (ISO 4649), and UV stability (ASTM D4329).
- Sustainability: 100% recyclable PP with 30% post-industrial recycled content.
References
- VidePak Corporate Profile: https://www.pp-wovenbags.com/
- Regulatory Documents: EN 15507:2014, ASTM D5261-22, JIS Z 0238:2020.
- Industry Reports: Chemical Packaging Innovations 2024 (Smithers Pira).
For inquiries, contact info@pp-wovenbags.com.
External Resources:
- Explore FFS roll bag applications in chemical logistics: FFS Roll Bags: Navigating Global Market Demands.
- Learn about advanced anti-static solutions: BOPP Woven Bags: Revolutionizing Chemical Powder Packaging.
Authored by VidePak’s Chemical Packaging Division | Updated: March 2025