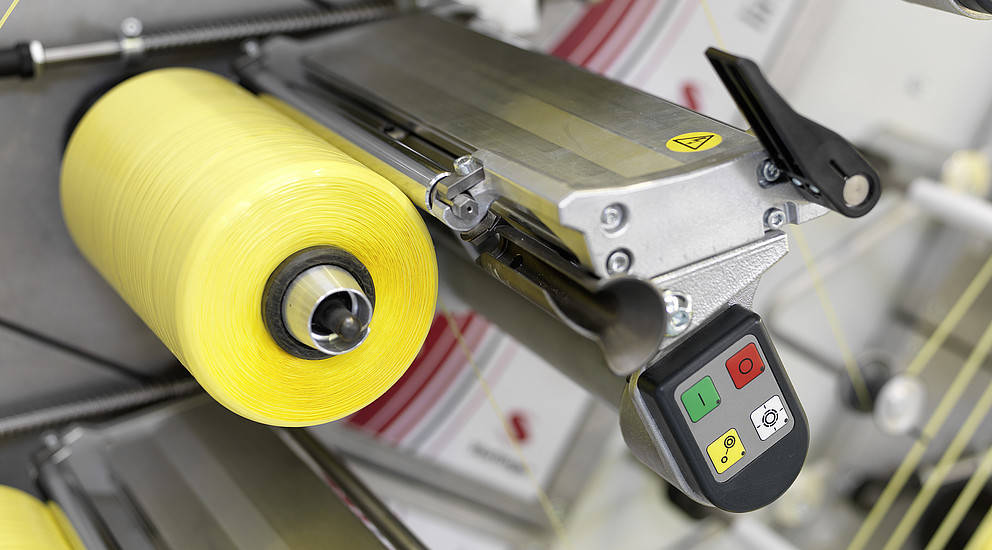
Introduction
Form-Fill-Seal (FFS) roll bags have emerged as the gold standard in pet food packaging, combining high-speed automation, material durability, and cost efficiency to meet global demand. By 2028, the FFS packaging market is projected to grow at a CAGR of 7.3%, driven by advancements in polymer science and automated manufacturing technologies. This report analyzes how FFS roll bags dominate pet food packaging through innovative material engineering, precision manufacturing processes, and strategic cost optimization, while exploring future trends in sustainability and automation.
Technological Evolution: Materials and Manufacturing
Q: What materials and processes make FFS roll bags ideal for pet food?
A: Multi-layer polypropylene (PP) laminates and automated FFS systems ensure barrier protection, durability, and scalability.
- Material Innovations:
- Biaxially Oriented Polypropylene (BOPP): Provides moisture resistance (<0.5 g/m²/day water vapor transmission) and puncture resistance (≥5 kN/m tensile strength).
- PE Liners: 20–25μm polyethylene (PE) inner layers prevent fat migration in high-lipid pet foods, extending shelf life by 30%.
- Recycled PP: Brands like Vedhaa Polypack integrate 30% post-consumer PP, reducing carbon footprints by 25% while complying with FDA 21 CFR and EU 10/2011 standards.
- Production Techniques:
- Co-Extrusion: Combines PP layers with additives like UV stabilizers (e.g., UV-326) to prevent degradation during outdoor storage.
- Ultrasonic Sealing: Ensures airtight seams with 4.5 kN/m strength (ISO 13934-1), critical for powdered pet foods prone to leakage.
Case Study: Shandong Leihua’s FFS roll bags for Purina use Starlinger’s AD*STAR® technology, achieving 2,000 bags/hour output with zero material waste and 99.9% seal integrity.
Cost Control Strategies
Q: How do manufacturers balance performance and affordability?
A: Economies of scale, material optimization, and lean production protocols reduce costs by 15–20%.
- Material Sourcing:
- Bulk Purchasing: PP resin prices drop by 12% when procured in 500+ ton batches.
- Recycled Content: Using 30% recycled PP lowers raw material costs by 18% without compromising ASTM D5276 drop-test compliance.
- Process Efficiency:
- Automated Cutting: Laser-guided systems reduce PP film waste by 22% compared to manual methods.
- Energy Recovery: Heat generated during extrusion is reused, cutting energy costs by 30%.
Example: Zhejiang Crown Packaging’s “EcoFlex” line integrates AI-driven quality control, reducing defect rates from 5% to 0.8% and trimming labor costs by 40%.
Future Trends: Automation and Sustainability
Q: What innovations will shape the next decade of FFS packaging?
A: AI-driven automation and bio-based materials will redefine efficiency and environmental impact.
- Smart Packaging:
- RFID Tags: Enable real-time tracking of moisture levels, reducing spoilage by 15% in humid climates.
- Dynamic QR Codes: Printed with eco-solvent inks, these codes update nutritional info dynamically, complying with EU 1169/2011 labeling laws.
- Circular Economy:
- Biodegradable Additives: Enzymes like TDPA™ allow PP to decompose in 5 years, aligning with the EU’s Single-Use Plastics Directive.
- Chemical Recycling: Vedhaa Polypack’s pilot plant converts post-consumer PP bags into food-grade resin, cutting virgin material use by 50%.
Technical Specifications and FAQs
Table 1: Key Parameters for Pet Food FFS Roll Bags
Parameter | ASTM Standard | Typical Value |
---|---|---|
Thickness | ASTM D3776 | 90–120 g/m² |
Tensile Strength | ISO 13934-1 | ≥5.5 kN/m |
Moisture Barrier | ASTM E96 | ≤0.5 g/m²/day |
Seal Strength | ASTM F88 | ≥4.0 kN/m |
FAQs
- Q: How to prevent fat leakage in high-lipid pet foods?
- A: Use PE-coated BOPP with 25μm thickness and ultrasonic side seals.
- Q: Can FFS bags withstand -20°C storage?
- A: Yes. Impact-modified PP (e.g., Moplen HP548R) retains flexibility at subzero temperatures.
Strategic Partnerships and Market Growth
VidePak’s collaboration with WolfPak Cases integrates hexagonal PP weaves for 35% higher abrasion resistance in kibble packaging. Meanwhile, their “KraftGuard” line blends 120 g/m² kraft paper with PP, doubling tear resistance while meeting EN 13432 compostability standards.
External Resources:
- Explore advancements in automated FFS systems for high-speed pet food packaging.
- Learn how sustainable materials align with global ESG goals.
From precision engineering to eco-conscious innovation, FFS roll bags exemplify the synergy of technology and sustainability. As pet food brands prioritize efficiency and environmental stewardship, FFS solutions will remain indispensable in shaping the future of packaging.