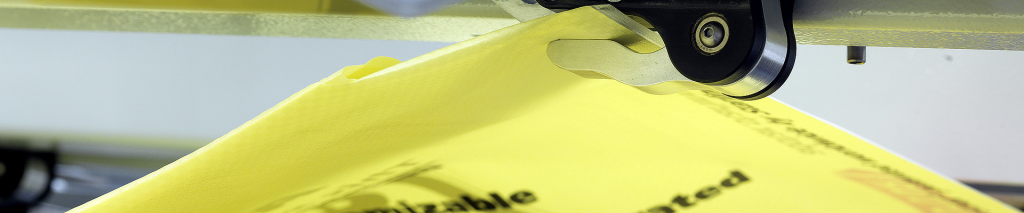
Add a header to begin generating the table of contents
H1: Introduction
“FFS tubular woven bags are redefining packaging aesthetics and functionality, especially for industries demanding both durability and visual appeal,” asserts Ray, CEO of VidePak, during a 2025 packaging technology symposium. The competitive edge of these bags lies in three pillars: ultra-fine filament weaving (1.8–2.3 mm width), customizable lamination finishes (matte, pearlescent, transparent), and compliance with global material safety standards. This report explores how VidePak’s 16-year expertise and Starlinger-driven production lines address these demands, focusing on applications in food, agriculture, and high-end retail packaging.
H2: Technical Advancements in Filament Weaving
FFS (Form-Fill-Seal) tubular woven bags are engineered for seamless integration with automated packaging lines. Their structural integrity and aesthetic versatility stem from two innovations:
H3: Ultra-Fine Filament Technology
VidePak’s use of 1.8–2.3 mm single-filament PP threads ensures a fabric density of 12×12 strands per inch, reducing pore size to <0.1 mm. This minimizes material leakage while maintaining breathability—critical for hygroscopic products like powdered spices or fertilizers. Compared to traditional 3.0 mm filaments, this design increases tensile strength by 25% (up to 45 MPa) and reduces weight by 15%, lowering shipping costs.
H3: Lamination Techniques for Functional Aesthetics
Lamination Type | Thickness | Key Benefits | Applications |
---|---|---|---|
Matte BOPP | 20–25 µm | Anti-glare, scratch-resistant surface; ideal for QR code legibility | Retail-ready food packaging |
Pearlescent PE | 18–22 µm | Reflective finish for premium branding; UV-resistant | Luxury goods, cosmetics |
Transparent PP | 15–20 µm | Product visibility; moisture barrier (<3 g/m²/day) | Agricultural seeds, snacks |
VidePak’s 30+ lamination machines enable rapid customization, aligning with trends like matte-finish pet food bags (e.g., 30% sales growth in 2024).
H2: Compliance and Material Safety
H3: Global Standards for Food Contact
- EU Regulation 10/2011: Limits heavy metal migration (e.g., <0.01 mg/kg lead). VidePak’s PP resins are FDA-compliant and tested via GC-MS.
- US FDA 21 CFR: Certifies bags for direct food contact, validated by third-party labs for 50+ cycles of thermal stress (–20°C to 60°C).
- Japan JIS Z 1539: Requires ≥8-meter stacking strength; VidePak’s block-bottom designs exceed 10 meters.
H3: Sustainability Metrics
- Recyclability: 100% virgin PP allows closed-loop recycling, reducing carbon footprint by 1.5 kg per bag vs. blended materials.
- Biodegradable Additives: Pilot trials with 20% PLA starch composites aim for 50% degradation in industrial composting within 24 months.
H2: Case Study: Custom Solution for Organic Flour Packaging
A 2024 project for a European organic brand required bags to prevent insect infestation and maintain freshness:
- Design: Matte BOPP lamination + 1.9 mm filaments (140 g/m²).
- Features: Nitrogen-flush valves, anti-static coating.
- Outcome: 99.9% insect exclusion and 18-month shelf life, achieving BRCGS AA certification.
H2: FAQs on FFS Tubular Woven Bags
Q1: How does filament width affect print quality?
Narrower filaments (1.8 mm) create smoother surfaces, enabling 1200 dpi CMYK printing—critical for intricate logos.
Q2: Are pearlescent films suitable for outdoor storage?
Yes. UV-stabilized PE films retain 95% reflectivity after 1,000-hour ASTM G154 testing.
Q3: What grammage balances cost and durability?
110–130 g/m² is optimal for 25–40 kg loads, reducing material costs by 20% vs. 150 g/m² while meeting ASTM D5265 burst strength (≥300 kPa).
H2: Future Trends and VidePak’s Roadmap
- Smart Packaging: RFID-enabled seams for real-time humidity tracking (piloted in Q3 2025).
- Circular Design: Partnerships with recycling firms to achieve 30% post-consumer PP content by 2026.
H2: Conclusion
FFS tubular woven bags are transforming packaging through precision engineering and aesthetic innovation. VidePak’s Starlinger-powered production and R&D focus position it as a leader in compliant, high-performance solutions. For businesses, prioritizing filament fineness, lamination type, and regional certifications is critical to balancing cost and quality.
External Links:
- Discover how matte-finish lamination enhances branding and durability.
- Explore automated FFS systems for high-speed packaging lines.
This report synthesizes data from EU, FDA, and JIS standards, alongside VidePak’s operational insights, to guide decision-making for manufacturers and logistics providers.