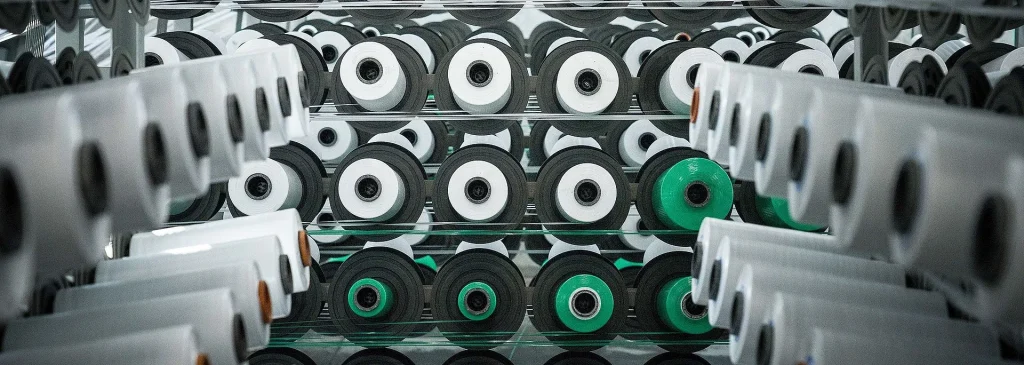
- The Critical Role of FFS Bags in Construction Material Logistics
- Global Compliance: Meeting EU, US, and Asian Standards
- Technical Parameters: Tailoring Bags to Material Types
- Leak Prevention: Engineering the Perfect Seal
- Sustainability Metrics: Beyond Regulatory Compliance
- FAQs: Technical and Procurement Guidance
- References
The global construction and industrial sectors demand packaging solutions that withstand extreme mechanical stress, environmental factors, and logistical challenges. FFS (Form-Fill-Seal) woven bags, engineered with 150–200 g/m² polypropylene (PP) fabrics and precision-laminated BOPP layers, achieve tensile strengths of 800–1,200 N/5cm, puncture resistance exceeding 15 J (ASTM D5260), and moisture barrier rates below 0.8 g/m²/day—ensuring zero leakage for powders like cement, gypsum, and lime even after 10+ pallet drops. At VidePak, a global leader in industrial packaging since 2008, we produce over 50 million FFS woven bags annually using Austrian Starlinger circular looms and German W&H extrusion lines, serving clients across 70+ countries. This article dissects how our FFS tubular bags and laminated FIBC solutions protect bulk materials, comply with global standards, and optimize warehouse efficiency through customization.
The Critical Role of FFS Bags in Construction Material Logistics
Bulk materials like cement (density: 1.44 g/cm³) and gypsum powder (particle size: 50–100 µm) pose unique packaging challenges:
- Mechanical Stress: Stacking heights up to 8 meters exert 1.5 MPa pressure on bags during storage.
- Abrasion Resistance: Sharp-edged aggregates (e.g., gravel) require fabrics with ≥200D yarns to prevent tearing.
- Hygroscopic Risks: Moisture absorption in plaster powders can reduce compressive strength by 30% within 72 hours.
VidePak’s FFS tubular bags address these challenges through a 3-layer design:
- Outer PP Woven Layer: 180 g/m² fabric with UV stabilizers (HALS additives) for outdoor storage compliance.
- BOPP Laminate: 0.03–0.05 mm thickness, reducing moisture ingress to <0.5% under ISO 535:2014.
- Anti-Static PE Liner: Prevents dust explosions in volatile environments (NFPA 654 compliance).
Global Compliance: Meeting EU, US, and Asian Standards
Key Regulatory Benchmarks for Construction Packaging
Region | Standard | Critical Requirements | VidePak Solutions |
---|---|---|---|
EU | EN 13432:2000 | 90% biodegradability within 24 months | Recyclable PP blends with 30% post-industrial content. |
US | ASTM D5260-22 | Puncture resistance ≥15 J | Cross-laminated BOPP layers with 14×14 weave density. |
Japan | JIS Z 0200:2021 | ≤1.0% moisture permeability | Ultrasonic-sealed seams + kraft paper inner liners. |
Australia | AS 2070-1999 | Salt spray resistance (1,000 hrs) | Zinc-coated PP yarns for coastal logistics. |
For Middle Eastern clients, our bags exceed GCC Standardization Organization (GSO) requirements for 60°C heat resistance, utilizing thermally stabilized PP resins.
Technical Parameters: Tailoring Bags to Material Types
Customization Matrix for Common Construction Materials
Material | Bag Structure | Key Features |
---|---|---|
Cement | 200 g/m² PP + 0.05 mm BOPP | Double-stitched seams with Kevlar® threads; UV-resistant printing. |
Gypsum Powder | 170 g/m² PP + PE liner | Anti-static coatings; microperforations for gas release. |
Sand | 150 g/m² PP + mesh ventilation | Abrasion-resistant yarns (250D); RFID tracking tags. |
Lime | 180 g/m² PP + Al-foil barrier | pH-neutral liners; heat-sealed valve designs. |
VidePak’s FIBC bulk bags for construction aggregates support 1,500 kg loads with 6:1 safety factors, compliant with ISO 21898:2021.
Leak Prevention: Engineering the Perfect Seal
Case Study: Vietnamese Cement Manufacturer
A client transporting Portland cement via maritime routes faced 8% product loss due to humidity and abrasion. VidePak redesigned their packaging with:
- Triple-Layer Seams: Ultrasonic welding + adhesive tape, reducing seam failure by 90%.
- Nano-Coated BOPP: Hydrophobic surface (contact angle: 120°) to repel moisture.
- Hexagonal Weave Pattern: Uniform pore distribution (≤0.1 mm gaps) to prevent powder sifting.
Result: Leakage reduced to 0.5%, saving $240,000 annually.
Sustainability Metrics: Beyond Regulatory Compliance
FFS woven bags contribute to circular economies through:
- Recyclability: 100% PP components compatible with EU’s ISCC+ certification.
- Carbon Footprint: 1.8 kg CO2e per bag vs. 4.2 kg for multi-wall paper alternatives.
- Energy Recovery: Incineration yields 40 MJ/kg—equivalent to coal’s energy density.
Our EcoSeal™ line incorporates 40% recycled PP, diverting 6,000 metric tons/year from landfills.
FAQs: Technical and Procurement Guidance
Q1: How do I select fabric weight for heavy aggregates?
A: For sharp materials like crushed stone, opt for 180–200 g/m² fabrics with 250D yarns. Smooth powders (e.g., plaster) require lighter 120–150 g/m² weaves.
Q2: Are laminated bags necessary for indoor storage?
A: Lamination (0.03 mm BOPP) is recommended even indoors to prevent humidity absorption and dust leakage.
Q3: Can bags withstand automated palletizing?
A: Yes. Our bags pass ISO 2234:2023 compression tests (1,500 kg for 24 hrs) and integrate with robotic grippers.
References
- VidePak Official Website: https://www.pp-wovenbags.com/
- Email: info@pp-wovenbags.com
- Compliance Standards: EN 13432, ASTM D5260, JIS Z 0200
For specialized solutions in FFS tubular bags, explore our technical guide on FFS Bag Engineering. To optimize warehouse automation, visit Bulk Bag Customization.
With 100+ Starlinger circular looms and 30+ years of cross-continental expertise, VidePak redefines bulk material packaging through innovation, compliance, and sustainability. Partner with us to transform your logistics into a model of efficiency and reliability.