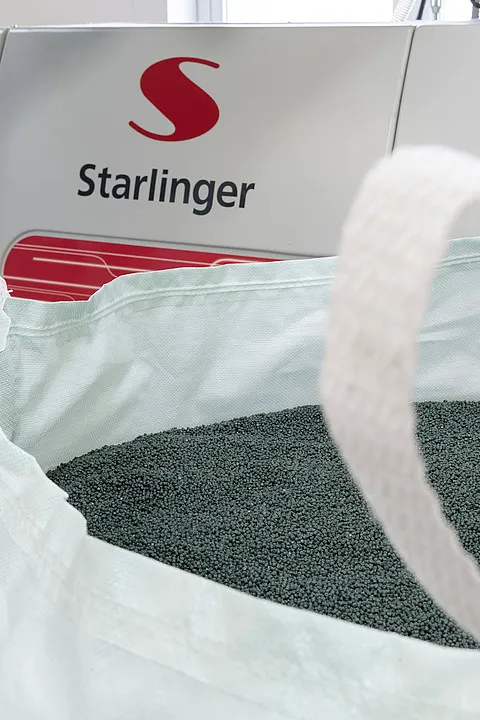
- Introduction
- Technical Specifications: Precision in Design
- Comparative Analysis: FFS Bag Parameters by Application
- FAQs: Addressing Procurement Concerns
- VidePak’s Innovation: Aligning with China’s Manufacturing Vision
- References
- What Are FFS Woven Bags?
- The Role of FFS Woven Bags in Modern Packaging
- Challenges in the Chinese Woven Bag Industry
- VidePak: Leading the Way with Innovation and Branding
- The Future of the Chinese Woven Bag Industry
- Conclusion: A Competitive Edge in FFS Woven Bags
- Keywords in Action
The primary answer this article provides is: FFS (Form-Fill-Seal) woven bags combine cutting-edge automation with customizable durability, offering thickness ranges of 0.08–0.15 mm, fabric weights of 80–220 g/m², and load capacities up to 2,500 kg. Anti-static variants integrate conductive carbon threads or coatings to dissipate charges below 10^6 Ω, ensuring safety in explosive environments. VidePak’s 30+ years of expertise, ISO-certified production, and Starlinger machinery enable us to deliver precision-engineered solutions for industries ranging from agriculture to chemicals, with a global annual output exceeding 200 million units.
Introduction
In an era where packaging efficiency and sustainability are paramount, FFS woven bags have emerged as a cornerstone of modern logistics. These bags, designed for automated filling and sealing, are revolutionizing bulk material handling by minimizing human intervention and maximizing consistency. For industries like agriculture, chemicals, and construction, selecting the right FFS bag involves balancing technical specifications—such as fabric weight, anti-static properties, and load capacity—with environmental and operational demands.
VidePak, founded in 2008 by CEO Ray, leverages 30+ years of industry expertise and advanced Austrian Starlinger machinery to produce FFS bags that meet rigorous global standards. With a workforce of 568 employees and annual sales of $80 million, we serve clients across 50+ countries, delivering solutions that align with China’s shift toward high-quality, innovation-driven manufacturing.
Technical Specifications: Precision in Design
1. Thickness, Fabric Weight, and Size Ranges
FFS woven bags are engineered for versatility, with parameters tailored to specific applications:
- Thickness: 0.08–0.15 mm, optimized for puncture resistance without compromising flexibility. Thinner bags (0.08 mm) suit lightweight powders like flour, while thicker variants (0.15 mm) handle abrasive materials like cement.
- Fabric Weight: 80–220 g/m². Lower weights (80–120 g/m²) are ideal for retail packaging, whereas heavy-duty applications (180–220 g/m²) require reinforced weaves for tensile strengths exceeding 35 N/cm².
- Size Range: Customizable from 20 cm × 30 cm (small-seed packaging) to 100 cm × 150 cm (bulk chemical storage), with seam designs ensuring airtight seals.
Example: A Brazilian fertilizer producer reduced spillage by 40% using VidePak’s 0.12 mm thick, 180 g/m² FFS bags with double-stitched seams.
2. Anti-Static Mechanisms: Safeguarding Hazardous Environments
Static electricity poses risks in industries handling flammable powders or solvents. Anti-static FFS bags employ two primary technologies:
- Conductive Threads: Carbon-infused polypropylene threads woven into the fabric create a continuous conductive network, dissipating charges to maintain surface resistivity below 10^6 Ω.
- Coating Solutions: Anti-static agents (e.g., glycerol monostearate) are applied to the bag’s surface, reducing static buildup by attracting ambient moisture.
Case Study: A Korean chemical company eliminated electrostatic discharge incidents by adopting VidePak’s conductive-thread FFS bags, achieving compliance with IEC 61340-4-4 standards.
3. Load Capacity: Engineering for Heavy-Duty Demands
FFS bags support weights from 10 kg to 2,500 kg, depending on fabric density and structural design:
- Light Loads (10–500 kg): Single-ply bags with 80–120 g/m² fabric for retail grains or pet food.
- Medium Loads (500–1,500 kg): Laminated BOPP layers enhance durability for construction materials like sand or gravel.
- Heavy Loads (1,500–2,500 kg): Cross-laminated PP woven fabric with 4-panel designs, tested to a safety factor (SF) of 6:1 for industrial minerals.
Comparative Analysis: FFS Bag Parameters by Application
Application | Thickness (mm) | Fabric Weight (g/m²) | Load Capacity (kg) | Anti-Static Solution |
---|---|---|---|---|
Agricultural Seeds | 0.08–0.10 | 80–100 | 10–50 | Non-conductive |
Chemical Powders | 0.12–0.15 | 150–220 | 1,000–2,500 | Conductive threads |
Construction Sand | 0.10–0.12 | 120–180 | 500–1,500 | Anti-static coating |
Food Additives | 0.08–0.10 | 100–130 | 20–200 | FDA-approved coatings |
FAQs: Addressing Procurement Concerns
Q1: How does fabric weight impact cost and durability?
Higher g/m² fabrics (e.g., 220 g/m²) increase material costs by 15–20% but extend lifespan by 3–5 years in abrasive environments. For non-abrasive goods like flour, 100 g/m² bags offer optimal cost-efficiency.
Q2: Are anti-static bags reusable?
Yes, provided they undergo rigorous inspection for wear. VidePak’s conductive-thread bags withstand up to 15 reuse cycles, per ISO 22442 guidelines.
Q3: What certifications ensure food safety?
FFS bags for food require FDA, EU 10/2011, and BRC certifications. VidePak’s laminated BOPP variants meet these standards, with moisture barriers (<0.5% permeability) for hygroscopic products like sugar.
Q4: Can FFS bags withstand tropical climates?
UV-stabilized PP resin and laminated PE layers prevent degradation in humid or high-temperature environments. VidePak’s bags retain 95% tensile strength after 12 months in 40°C/90% RH conditions.
VidePak’s Innovation: Aligning with China’s Manufacturing Vision
China’s manufacturing sector, now prioritizing quality over quantity, relies on automation and R&D—a vision embodied by VidePak’s FFS solutions. Key advancements include:
- Starlinger Machinery: 16 extrusion lines and 100+ circular looms enable production speeds of 1,200 bags/hour, with ±0.5 mm dimensional accuracy.
- Eco-Friendly PP: Recyclable polypropylene reduces carbon footprint by 30% compared to traditional PE blends.
- Custom Printing: 10-color rotary printers support Pantone-matched branding, with MOQs as low as 5,000 units.
References
- VidePak Company Profile: https://www.pp-wovenbags.com/
- Industry Standards: ISO 9001, BRC Packaging, IEC 61340-4-4.
- Technical Guides: FFS Bag Design for Hazardous Materials (Global Packaging Alliance, 2025).
For inquiries, contact info@pp-wovenbags.com.
External Resources:
- Explore FFS tubular bag applications in our technical guide: FFS Tubular Bags: Optimizing Automated Packaging Systems.
- Learn about key parameters for FFS woven bags: Understanding FFS Woven Bags: Specifications and Customization.
Authored by VidePak’s R&D Team | Updated: March 2025
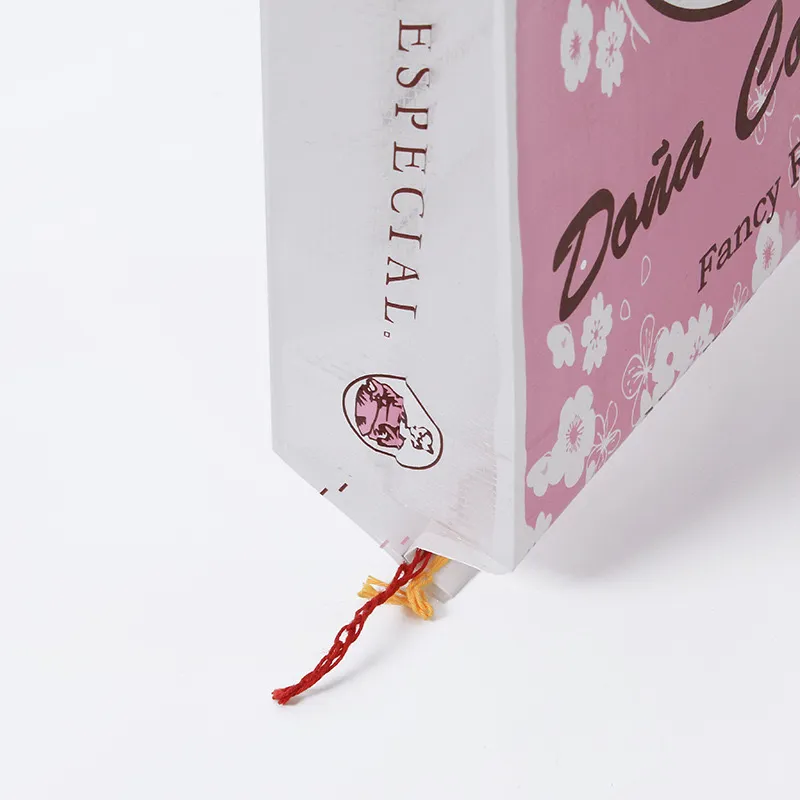
- Introduction
- Technical Specifications: Precision in Design
- Comparative Analysis: FFS Bag Parameters by Application
- FAQs: Addressing Procurement Concerns
- VidePak’s Innovation: Aligning with China’s Manufacturing Vision
- References
- What Are FFS Woven Bags?
- The Role of FFS Woven Bags in Modern Packaging
- Challenges in the Chinese Woven Bag Industry
- VidePak: Leading the Way with Innovation and Branding
- The Future of the Chinese Woven Bag Industry
- Conclusion: A Competitive Edge in FFS Woven Bags
- Keywords in Action
Form-Fill-Seal (FFS) Woven Bags are a crucial packaging solution widely used across industries such as agriculture, chemicals, construction, and food processing. FFS technology involves an automated process that fills and seals the bags simultaneously, increasing efficiency and reducing packaging time. In this article, we will dive into the features of FFS Woven Bags and analyze the future of the woven bag industry in China from a technological and brand-building perspective. We’ll also discuss how companies like VidePak, with over 20 years of experience, set themselves apart from other manufacturers through quality, innovation, and branding.
What Are FFS Woven Bags?
FFS Woven Bags are high-strength woven polypropylene (PP) or polyethylene (PE) bags designed for automated packaging systems. These bags are used with FFS machines that form, fill, and seal the bags in a single, continuous process, making them ideal for high-speed packaging applications.
The key features of FFS Woven Bags include:
- Durability: Woven PP bags are incredibly durable and capable of withstanding heavy loads and harsh environments.
- Customizability: They are available in various sizes, colors, and printing designs, making them suitable for branding and product differentiation.
- Moisture and UV Resistance: Many FFS woven bags are laminated or lined for enhanced moisture protection, and optional UV treatments can extend their shelf life outdoors.
- Eco-friendly: Many FFS woven sacks are recyclable, making them a more sustainable packaging option compared to single-use plastic bags.
Parameter | Specification |
---|---|
Material | Woven PP, optional PE liner |
Weight Capacity | 10kg to 50kg |
Available Sizes | Customizable based on customer requirements |
Printing | Up to 8 colors, suitable for full-color branding |
Lamination | Available for moisture and UV resistance |
Sealing Method | Heat-sealable with FFS machines |
Strength | High tensile strength, suitable for heavy loads |
The Role of FFS Woven Bags in Modern Packaging
FFS woven bags offer a more efficient and cost-effective packaging solution compared to traditional methods. The automated system used in FFS machines significantly reduces the manual labor required in packaging, allowing for higher throughput and more consistent product sealing.
For industries such as agriculture, where products like grains, fertilizers, and seeds need to be packaged quickly and in bulk, FFS Woven sacks provide the speed and strength required to ensure efficiency and durability. The bags’ woven structure provides additional tear resistance, preventing punctures and damage during transit, while the option for moisture barriers ensures product integrity, especially for materials that are sensitive to water exposure.
Challenges in the Chinese Woven Bag Industry
China is one of the world’s largest producers of woven bags, with thousands of manufacturers spread across the country. However, the industry faces several challenges, particularly regarding technological innovation, brand building, and market differentiation.
1. Lack of Brand Awareness
Most woven bag manufacturers in China operate with a short-term focus on volume production rather than long-term brand building. These manufacturers often emphasize price competitiveness at the cost of quality, leading to inconsistent products and a lack of customer loyalty.
Without a strong brand identity, companies struggle to differentiate their products in the global marketplace. Branding is crucial for attracting high-quality clients who value consistency, durability, and customizability. However, many manufacturers in China have not yet fully embraced this concept.
2. Limited Technological Innovation
While there are many manufacturers in China, only a few focus on upgrading their machinery and adopting the latest production technologies. Most manufacturers use outdated equipment that hinders their ability to produce high-quality products at scale. This lack of innovation creates challenges in meeting the growing demand for customized and specialized packaging solutions like Tubular Woven Bags and FFS PP Bags.
Moreover, the lack of proper investment in research and development (R&D) results in slower product improvement cycles. With global packaging requirements continuously evolving, manufacturers need to be agile and responsive to market demands, which requires a focus on innovation and technological advancement.
3. Inconsistent Quality Control
Another challenge faced by many Chinese manufacturers is inconsistent quality control. While some manufacturers adhere to strict international standards, many do not implement rigorous testing and inspection processes. As a result, the quality of their FFS Woven Bags can vary widely, leading to customer dissatisfaction and a higher return rate.
VidePak: Leading the Way with Innovation and Branding
Unlike many other manufacturers in China, VidePak has recognized the importance of technological innovation, quality control, and brand building. With over 20 years of industry experience, we have become a trusted supplier of FFS Woven sacks, PP Tubular Woven bags, and other woven packaging solutions.
1. Commitment to Quality and Innovation
At VidePak, we understand that staying ahead of the competition requires continuous investment in new technologies and equipment. Our entire production line is equipped with cutting-edge machinery from Starlinger, a world-renowned supplier of advanced packaging equipment. This ensures that every product we manufacture meets international quality standards and is produced with maximum efficiency.
Starlinger’s advanced technology, combined with our commitment to using only the highest-quality raw materials, allows us to produce FFS Woven Bags that are not only durable but also customizable to meet the specific needs of our clients. This includes a wide range of printing options, allowing businesses to incorporate branding elements and design choices that differentiate their products in the marketplace.
2. Focus on Technological Iteration
Unlike many competitors that rely on outdated technology, VidePak prioritizes innovation through continuous upgrades to our machinery and production processes. Our investment in Starlinger’s equipment ensures that we stay at the forefront of the industry, producing woven bags with precise quality and meeting the evolving needs of our customers.
One example of this is our use of the multi-layer co-extrusion process for creating Tubular Woven Bags. This process ensures superior strength, flexibility, and moisture resistance, making these bags ideal for industries such as chemicals and construction.
3. Rigorous Quality Control
Quality control is a cornerstone of VidePak’s manufacturing process. From the initial selection of raw materials to the final inspection of the finished product, we implement strict quality control measures to ensure that every bag we produce meets the highest standards.
We source only the best PP and PE granules, ensuring that our products are durable, flexible, and resistant to tearing and punctures. Our quality control team conducts multiple tests throughout the production process, including tensile strength testing, moisture barrier testing, and visual inspections.
By adhering to these rigorous standards, we can offer our clients consistently high-quality products that meet international specifications, whether they are looking for FFS PP Bags, multi-wall woven bags, or other packaging solutions.
Parameter | Specification |
---|---|
Raw Material | 100% virgin PP/PE |
Equipment Used | Starlinger full production line |
Production Capacity | High-speed, fully automated |
Quality Control | Strict adherence to international standards |
Innovation | Multi-layer co-extrusion, advanced lamination |
The Future of the Chinese Woven Bag Industry
The future of the Chinese woven bag industry lies in its ability to embrace technological innovation and build strong, recognizable brands. As global demand for customized and high-quality packaging continues to rise, manufacturers must focus on improving product quality, adopting advanced technologies, and creating value through branding.
1. Technological Advancements
The industry will need to shift towards greater automation and innovation in production techniques. Companies that invest in advanced machinery, like VidePak with its Starlinger-equipped production lines, will have a competitive edge. These technologies allow for greater efficiency, lower production costs, and the ability to produce higher-quality products that meet international standards.
2. Brand Building
To succeed in the long term, Chinese woven bag manufacturers must focus on building a strong brand presence. Companies like VidePak have recognized the importance of creating a recognizable brand that stands for quality, reliability, and innovation. By consistently delivering high-quality products and excellent customer service, manufacturers can build trust with clients and differentiate themselves from competitors.
Conclusion: A Competitive Edge in FFS Woven Bags
In an increasingly competitive global market, companies that focus on technological innovation, quality control, and brand building will thrive. At VidePak, we have over 20 years of experience in the woven bag industry and are committed to providing the highest-quality FFS Woven Bags and other packaging solutions. Through continuous innovation, rigorous quality control, and a focus on customer satisfaction, we remain at the forefront of the industry, setting new standards for excellence in packaging.
Keywords in Action
- FFS Woven Bags
- FFS Woven sacks
- Tubular Woven bags
- PP Tubular Woven bags
- FFS PP Bags