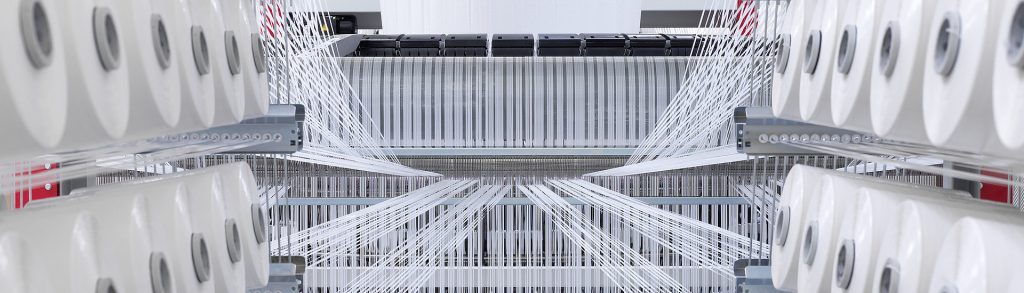
Introduction
Flexible Intermediate Bulk Containers (FIBCs) are essential in industries like agriculture, construction, and chemicals for their ability to carry heavy loads while maintaining durability and efficiency. Fine yarn technology has elevated FIBC performance by enhancing strength, flexibility, and sustainability. This report explores how the processes of extrusion, stretching, and weaving impact FIBC durability and flexibility and how advanced equipment like Starlinger and W&H ensures unmatched quality.
Key Production Processes and Their Impact on FIBCs
1. Extrusion: The Foundation of Yarn Strength
Extrusion involves melting polypropylene resin and forming it into filaments. This step determines the basic quality of the yarn and, by extension, the FIBCs.
- Temperature Control: Precise control of melt temperature is critical to avoid polymer degradation. Starlinger’s advanced extrusion systems ensure uniform melting, producing filaments with consistent strength and flexibility.
- Filament Uniformity: Uniformly thick filaments reduce weak points in the fabric, ensuring that the FIBCs maintain integrity under stress. Consistent extrusion directly translates to higher load-bearing capacity.
For example, bags designed to carry 1,000 kg loads depend on this uniformity to avoid tearing during transportation.
2. Stretching (Drawing): Strengthening the Yarn
Stretching aligns the molecular structure of the polypropylene, significantly improving tensile strength and elasticity. This process is critical for creating yarns capable of withstanding heavy and dynamic loads.
- Optimal Stretch Ratios: Controlled stretching maximizes yarn strength by aligning polymer chains without over-stretching, which could cause brittleness. W&H machinery excels in automating this process, ensuring every filament meets exact specifications.
- Elasticity Enhancement: Properly stretched yarns maintain flexibility, a vital property for bags that must endure movement and impact during handling.
For example, FIBCs used in agriculture benefit from these properties, as they need to resist tearing when loaded with sharp or irregular materials like grains and fertilizers.
3. Weaving: Balancing Durability and Flexibility
Weaving transforms yarn into fabric and determines the bag’s structural integrity and adaptability.
- Fine Weave Patterns: A tighter weave increases the fabric’s puncture resistance and reduces the risk of tears, making the FIBCs suitable for transporting sharp or heavy items.
- Customizable Density: By adjusting the weave density, manufacturers can create bags tailored to specific load capacities, balancing strength and cost-effectiveness.
For instance, a bag with a higher weave density is ideal for carrying hazardous chemicals, where both safety and containment are paramount.
Benefits of Fine Yarn Technology in FIBCs
1. Superior Durability
Fine yarn technology ensures high tensile strength while keeping the fabric lightweight. This durability comes from the precise alignment of polymer chains during stretching, which enhances load-bearing capabilities.
2. Enhanced Flexibility
The smooth surface of fine yarn fabrics allows for additional coatings, such as anti-static or UV-resistant layers, without compromising flexibility. This makes FIBCs versatile for various industries, including agriculture, chemicals, and construction.
3. Environmental Efficiency
By using less material without sacrificing strength, fine yarn technology reduces waste and supports sustainability. Recyclable polypropylene further minimizes the environmental impact of FIBC production.
Performance Parameters of FIBCs
Parameter | Why It Matters | How It’s Controlled |
---|---|---|
Tensile Strength | Determines the bag’s ability to handle heavy loads. | ASTM D5034 tensile tests. |
Elasticity | Prevents sudden tearing under dynamic stress. | ISO 13934-1 elongation tests. |
Puncture Resistance | Ensures durability when carrying sharp materials. | Puncture resistance testing. |
Fabric Density | Matches load capacity to specific industrial needs. | Dynamic load testing and density checks. |
Each parameter is crucial for ensuring that FIBCs perform reliably in demanding environments, from construction sites to agricultural fields.
Industry Trends and Innovations
Sustainability in Manufacturing
Fine yarn technology aligns with global sustainability goals by reducing raw material usage while maintaining performance. Recyclable polypropylene and energy-efficient processes further enhance the eco-friendly profile of FIBCs.
Advanced Equipment for Consistency
Starlinger and W&H machinery are pivotal in ensuring consistent quality. Starlinger’s precise temperature control during extrusion guarantees uniform filament production, while W&H’s automated stretching systems optimize molecular alignment for maximum strength. Discover more here.
Customization to Meet Diverse Needs
Industries increasingly demand tailored solutions, such as food-grade linings for agricultural use or anti-static coatings for chemical transport. Fine yarn fabrics provide the flexibility needed for these customizations.
FAQs
1. How does extrusion affect FIBC quality?
Precise extrusion ensures uniform filament thickness, which enhances the bag’s load-bearing capacity and reduces weak points.
2. Why is stretching crucial for durability?
Stretching aligns the polymer chains in the yarn, maximizing tensile strength and elasticity. This is essential for handling heavy or irregular loads.
3. How does weaving impact FIBC performance?
Weaving determines the fabric’s structural strength and flexibility. Fine weaves provide superior durability and resistance to punctures.
4. Are FIBCs made with fine yarn technology sustainable?
Yes, fine yarn reduces raw material usage and supports recyclability, making these FIBCs environmentally friendly and cost-efficient.
Conclusion
The durability and flexibility of FIBCs rely on the precision of extrusion, stretching, and weaving processes. Fine yarn technology enhances each of these stages, ensuring that the bags meet the demands of industries requiring high performance and reliability. With advanced machinery from Starlinger and W&H, companies like VidePak produce FIBCs that set new standards for quality and sustainability.
For further insights, explore:
- FIBC Bags: Revolutionizing Bulk Packaging with Ultrasonic Sealing Technology
- The Evolution and Benefits of FFS Roll Bags: A Focus on Fine Yarn Technology
Fine yarn technology represents the future of bulk packaging, offering unparalleled strength, adaptability, and environmental benefits.