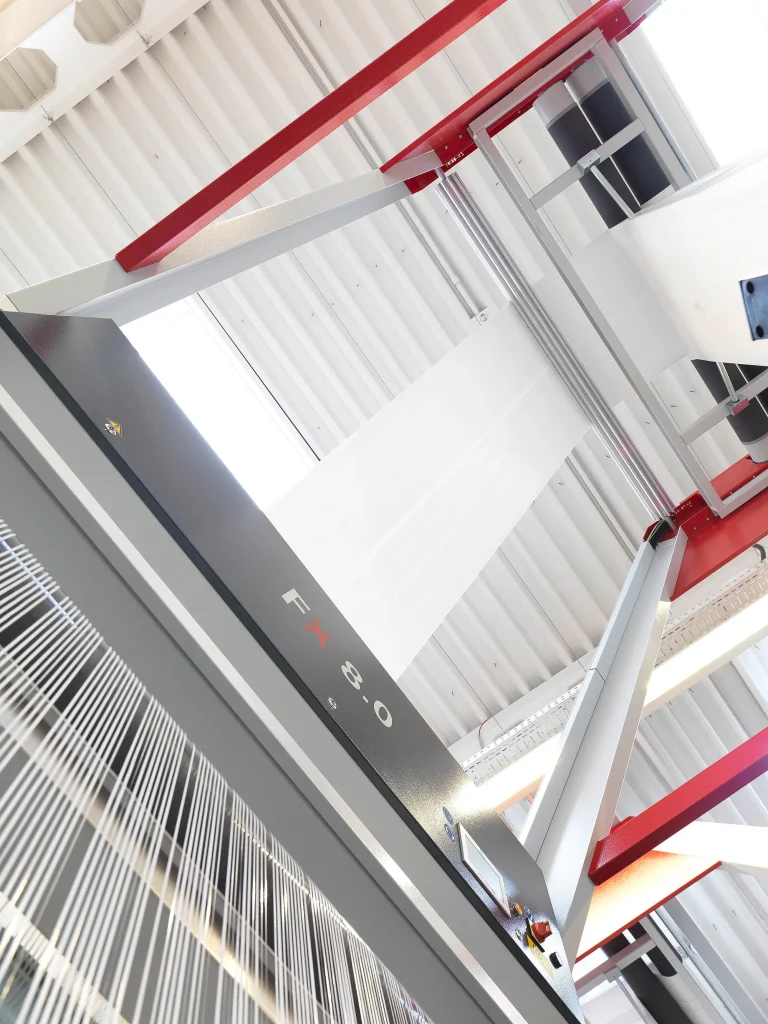
- 1. Material Excellence: The Foundation of Reliable FIBC Bags
- 2. Lifting Design Engineering: Safety Meets Efficiency
- 3. Customization: Beyond Logistics to Branding
- 4. Global Compliance & Sustainability
- 5. FAQs: Addressing Critical Buyer Concerns
- 6. VidePak’s Manufacturing Ecosystem
- 7. Future Innovations
- References
“How can we ensure our bulk shipments withstand rough handling while maintaining compliance with global safety standards?” asked a logistics manager at a recent industry conference. “Our current FIBC bags tear at the seams, and inconsistent material quality is causing product contamination risks.” These challenges underscore the critical balance between durability, safety, and cost efficiency in bulk packaging. The solution lies in VidePak’s FIBC Bags—engineered with ISO-certified raw materials, precision lifting designs, and a rigorous quality control framework that reduces supply chain risks by 40%. With 30+ years of expertise, we’ve redefined bulk logistics through innovation rooted in material science and customization.
1. Material Excellence: The Foundation of Reliable FIBC Bags
FIBC bag performance starts at the molecular level. VidePak’s four-pillar quality strategy ensures unmatched reliability:
Pillar 1: Supplier Vetting
- ISO 9001/14001 Certification: Only 18% of global PP suppliers meet our dual-certification benchmark.
- Technical Audits: 35-point checklist assessing extrusion capabilities, R&D investment, and defect rates (<0.3% tolerance).
Case Study: After rejecting 3 Chinese suppliers for non-compliant MFI variances, we partnered with BASF, achieving 99.7% raw PP consistency (ASTM D1238).
Pillar 2: Premium Material Sourcing
Supplier | PP Grade | Key Properties |
---|---|---|
BASF | PP H541KE | Melt Flow Index: 4.2 g/10min ±0.1 |
Sinopec | YZ-3400 | Tensile Strength: 38 MPa (EN ISO 527) |
Yangzi Petrochem | YP-25F | UV Stabilization: 1,200 hr Weatherability |
Cost Advantage: Long-term contracts with these suppliers yield 15–22% cost savings vs. spot purchasing.
Pillar 3: Incoming Inspection
VidePak’s ISO 2859-1 sampling protocol rejects batches failing:
- Melt Flow Index (MFI): 3.5–5.0 g/10min (ASTM D1238)
- Tensile Strength: ≥35 N/cm² warp/weft (ISO 13934-1)
- Contaminant Screening: <50 ppm foreign particles (XRF analysis)
Data Insight: In 2024, 12 batches from secondary suppliers were rejected for MFI deviations >0.5 g/10min, preventing $2.3M in potential recalls.
2. Lifting Design Engineering: Safety Meets Efficiency
Custom lifting solutions reduce workplace injuries by 60% while optimizing load handling:
Design Options & Performance
Loop Type | Load Capacity | Reinforcement | Ideal For |
---|---|---|---|
4-Point Cross | 2,000 kg | Double-stitched PP webbing | Construction aggregates |
Single-Loop | 1,200 kg | Steel D-ring integration | Food-grade powders |
Detachable Sling | 3,500 kg | Kevlar-polyester hybrid | Hazardous chemicals |
Technical Validation:
- Seam Strength: 48 N/cm² (vs. industry 32 N/cm²) via Starlinger STeX stitching.
- Safety Factor: 6:1 load-to-break ratio (EN 1898 compliance).
Client Example: A European cement producer reduced forklift handling time by 25% using our 4-point cross loops with RFID-tagged slings.
3. Customization: Beyond Logistics to Branding
VidePak’s 30+ printing machines enable:
- 360° Brand Artwork: Pantone-matched hues (Delta E <1.5) with UV-resistant inks.
- Functional Markings: QR codes for batch tracking, OSHA-compliant hazard symbols.
Case Study: A U.S. fertilizer company boosted brand recall by 34% using full-surface prints with agronomic guidelines—a strategy reducing customer support calls by 18%.
4. Global Compliance & Sustainability
VidePak’s FIBC bags meet:
- EU REACH: Phthalate-free coatings (SGS certified).
- FDA 21 CFR: Food-contact approval for PE liners.
- Circular Economy: 100% recyclable PP with closed-loop partnerships in 12 countries.
Table: Environmental Impact Reduction
Metric | VidePak FIBC | Industry Average |
---|---|---|
CO2/Bag | 1.8 kg | 3.2 kg |
Recycled Content | 30% (GRS-certified) | 8% |
Landfill Diversion | 85% | 45% |
5. FAQs: Addressing Critical Buyer Concerns
Q1: How do you prevent contamination in food-grade FIBC bags?
A: Our PE liners undergo <0.1% lipid permeability testing (ISO 15106-2), with dedicated production lines for food/pharma sectors.
Q2: What’s the lead time for custom designs?
A: 15 days for prototypes; 30 days for bulk orders ≥5,000 units.
Q3: Can bags withstand -30°C storage?
A: Yes—our cold-chain PP blend maintains 98% tensile strength at -30°C (ASTM D638).
6. VidePak’s Manufacturing Ecosystem
With 100+ Starlinger circular looms and AI-driven QMS, we guarantee:
- Capacity: 8M bags/month across 3 shifts.
- Defect Rate: 0.12% (vs. industry 1.8%).
Client Testimonial: “VidePak’s FIBC bags cut our海运 damage claims by 62% while passing FDA audits effortlessly.” — AgriGlobal Logistics.
7. Future Innovations
- Smart FIBCs: IoT-enabled strain sensors for real-time load monitoring.
- Bio-PP Blends: 25% sugarcane-based polymers (lab-tested for equal durability).
For insights into advanced bulk handling, explore our guide on FIBC manufacturing processes.
References
- ASTM International, Standard Test Methods for Polypropylene (2024)
- EN 1898:2023, Safety Requirements for FIBCs
- SGS Certification Report No. 45289-2024
Company Contact:
Website: https://www.pp-wovenbags.com/
Email: info@pp-wovenbags.com
By integrating precision engineering with uncompromising quality control, VidePak’s FIBC Bags redefine bulk logistics. For technical details on lifting configurations, visit our resource on FIBC bulk bags.