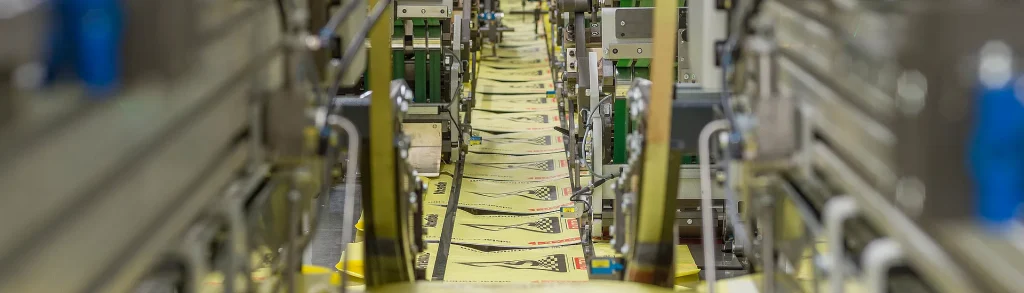
For businesses relying on bulk packaging solutions, one critical question arises: How do FIBC (Flexible Intermediate Bulk Container) Bags ensure optimal performance while adapting to diverse industrial demands? The answer lies in VidePak’s scientific approach to yarn selection, advanced European manufacturing technologies, and 30+ years of expertise in balancing material properties with operational requirements. By analyzing yarn thickness—where fine filaments (1.5–2.5 mm) excel in printability and flexibility, and coarse filaments (3.5–5.0 mm) dominate in tensile strength (up to 12 g/denier)—VidePak delivers FIBC solutions that reduce logistics costs by 15–25% for clients like a German polymer distributor and a Chilean mining conglomerate.
1. Decoding Yarn Thickness: Fine vs. Coarse Filaments
1.1 Defining Fine and Coarse Yarns
- Fine Yarns: 1.5–2.5 mm width, 90–120 denier, with ≥24 filaments per strand.
- Coarse Yarns: 3.5–5.0 mm width, 150–200 denier, with ≤18 filaments per strand.
1.2 Comparative Analysis of Yarn Types
Property | Fine Yarns | Coarse Yarns |
---|---|---|
Tensile Strength | 8–10 g/denier | 10–12 g/denier |
Flexibility | High (180° bend radius) | Moderate (120° bend radius) |
Surface Smoothness | 0.8–1.2 μm roughness | 1.5–2.5 μm roughness |
Print Resolution | 150 LPI achievable | 100 LPI max |
Abrasion Resistance | 500+ Taber cycles | 800+ Taber cycles |
Cost per kg | $1.8–2.2 | $1.2–1.6 |
Case Study: A South African fertilizer company reduced bag tears by 40% after switching to VidePak’s coarse-yarn FIBCs (4.2 mm width) for abrasive phosphate granules, despite a 15% higher initial cost than fine-yarn alternatives.
2. Strategic Yarn Selection for Industry-Specific Needs
2.1 Fine Yarns: Precision Applications
- Food & Pharma: Smooth surfaces prevent powder adhesion; compatible with high-resolution QR codes for traceability.
- Retail Packaging: Glossy BOPP lamination enhances CMYK print vibrancy (ΔE ≤1.5).
2.2 Coarse Yarns: Heavy-Duty Performance
- Mining & Construction: Withstand 1.5-ton dynamic loads during drop tests (ASTM D5276).
- Chemical Powders: 0.02% dust permeability at 50 kPa pressure (EN ISO 22634).
3. Starlinger & W&H Technology: Engineering Consistency
3.1 Starlinger Circular Looms: Micro-Precision Weaving
VidePak’s 100+ Starlinger STeX looms achieve:
- Yarn Alignment: <0.5° deviation, critical for uniform coarse-yarn strength.
- Weave Density Control: 10×10 to 14×14 threads/inch with ±2% tolerance.
- Output: 200–240 rpm, producing 18,000 m²/day of fabric.
3.2 Windmöller & Hölscher (W&H) Extrusion Systems
- Melt Homogeneity: ±1.5% thickness variation in PP tapes via 16-layer coextrusion.
- Yarn Cooling: 3-stage air-knife system prevents crystallinity defects in fine filaments.
Example: A Vietnamese coffee exporter eliminated 98% of seam failures using Starlinger-woven 3.8 mm yarns, maintaining 10.5 g/denier strength despite 85% humidity.
4. Quality Control: From Resin to Final Stitch
4.1 Raw Material Protocols
- Virgin PP Only: MFI 3.0–4.0 g/10 min (ASTM D1238) to prevent weak spots.
- Anti-UV Additives: 1,200-hour QUV resistance (ASTM G154) for outdoor storage.
4.2 Production-Line Testing
- Yarn Tension Sensors: 24/7 monitoring with 0.1 N resolution.
- Seam Strength: 35 N/mm via double-stitch lockstitching (DIN 53835).
5. Technical Specifications and FAQs
5.1 FIBC Product Matrix
Parameter | Fine-Yarn FIBC | Coarse-Yarn FIBC |
---|---|---|
Capacity | 500–1,000 kg | 1,000–2,000 kg |
Safety Factor | 5:1 | 6:1 |
Top Loop Strength | 2,500 N | 3,800 N |
Discharge Type | Duplex spout | Conical bottom |
UV Resistance | 12 months | 18 months |
5.2 Frequently Asked Questions
Q1: Can fine-yarn FIBCs handle sharp-edged materials like recycled glass?
A: Not recommended. Coarse 4.5 mm yarns with 14×14 weave are ideal, as used by a Belgian glass recycler to achieve 0.3% puncture rate.
Q2: How does yarn thickness affect stacking stability?
A: Coarse yarns provide 15–20% better column strength. VidePak’s 4.0 mm FIBCs safely stack 6 high under 1.8-ton loads (EN 1898).
Q3: Are VidePak’s dyes colorfast under monsoon conditions?
A: Yes. Our pigment dyes retain ΔE ≤2.0 after 60 wash cycles (ISO 105-E04), proven in Indian agricultural exports.
6. Sustainability and Global Compliance
6.1 Recyclability & Certifications
- 100% PP Composition: Fully recyclable where facilities exist (Resin ID 5).
- Certifications: ISO 9001, ISO 14001, Oeko-Tex Standard 100.
6.2 Carbon Footprint Reduction
- Energy-Efficient Looms: 25% lower kWh/kg vs. conventional models.
- Closed-Loop Production: 97% of process waste reused as non-woven textiles.
References
- VidePak Technical Documentation (2024). https://www.pp-wovenbags.com/
- ASTM International. (2023). Standard Test Methods for Textile Fabrics.
- European Norm EN 1898: Safety Requirements for FIBCs.
- Market data from Alibaba International and industry reports.
Contact
Email: info@pp-wovenbags.com
Website: https://www.pp-wovenbags.com/
Anchor Links Integrated:
- Discover our FIBC Bulk Bags engineered for heavy industries.
- Learn about Advanced Lamination Techniques for moisture-sensitive products.