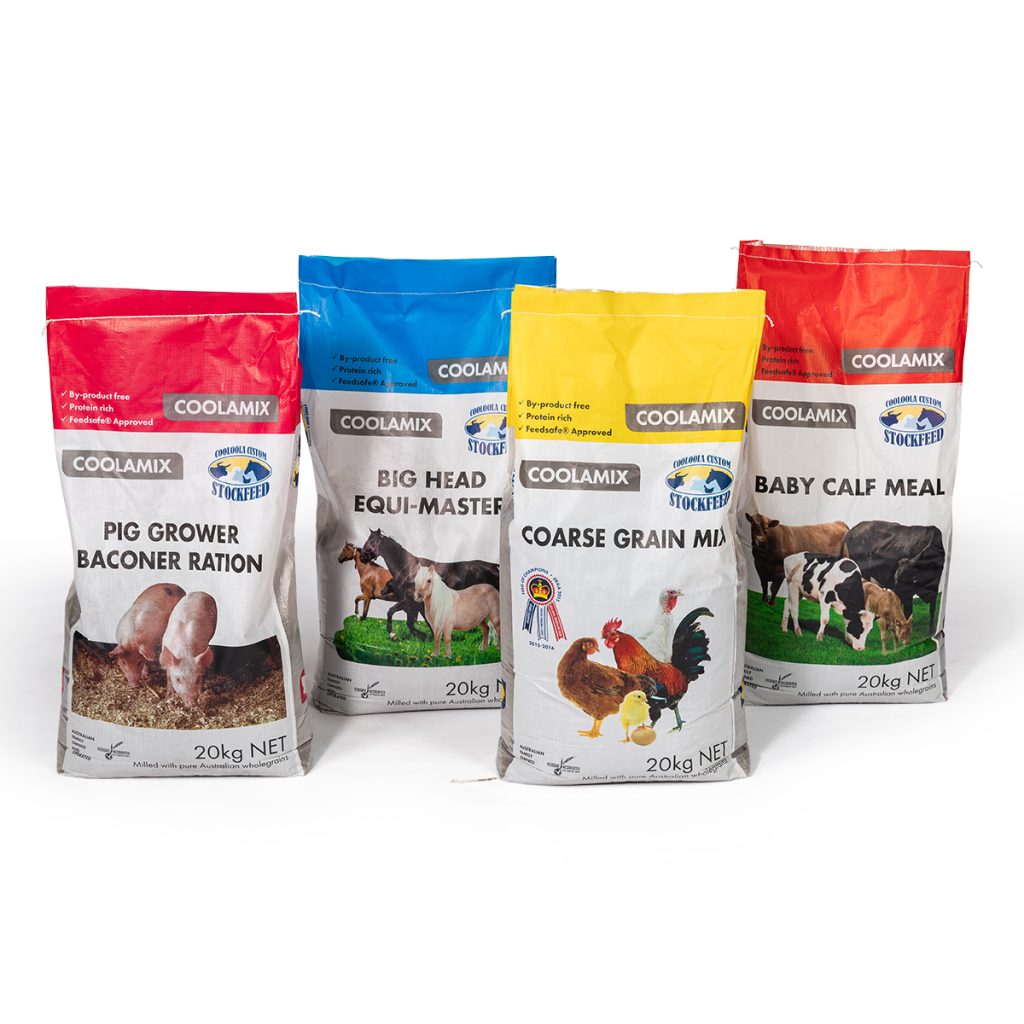
Ray, CEO of VidePak, gestures toward a warehouse stacked with FIBC bulk bags during a client tour:
“In today’s logistics landscape, a one-size-fits-all approach doesn’t cut it. Our FIBC bulk bags aren’t just containers—they’re tailored ecosystems. With customizable valves, handles, and prints, they reduce spillage by 90%, cut handling costs by 30%, and turn storage into a branding opportunity.”
This philosophy defines VidePak’s leadership in FIBC bulk bag manufacturing. Since 2008, the company has leveraged 30+ years of expertise, 526 employees, and Austrian Starlinger machinery to produce over 5 million FIBC bags annually. With ISO 9001 and BRCGS certifications, VidePak’s USD 80 million revenue reflects its ability to merge industrial scalability with hyper-customization. Below, we dissect how FIBC bulk bags optimize retail storage and logistics while aligning with global market demands.
1. Customization: The Key to Market Adaptability
1.1 Structural Customization for Diverse Applications
VidePak’s FIBC bags are engineered to address industry-specific challenges through modular design:
- Valve Types: Options include top-fill spouts, duffel tops, and discharge spouts with iris protection, reducing filling time by 40% for granular materials like pet food or chemicals.
- Handle Configurations: Cross-corner loops (for forklifts) and tunnel lift designs (for automated systems) optimize handling efficiency, supporting loads up to 2,000 kg with a 6:1 safety factor.
- Shape & Size: Rectangular “builder bags” for construction materials (e.g., sand, gravel) and cubic designs for pallet-friendly stacking maximize warehouse space utilization by 25%.
Case Study: A European agrochemical client reduced spillage during pneumatic filling by 95% using VidePak’s anti-static Type D bags with customized discharge spouts.
1.2 Material Innovation and Compliance
- PP/PE Blends: Virgin polypropylene (PP) woven fabric (120–150 g/m²) paired with polyethylene (PE) liners (0.15–0.25mm thickness) ensures moisture resistance (WVTR ≤5 g/m²/day) and compliance with EU REACH standards.
- Certifications: FDA-approved food-grade liners and UN-certified designs for hazardous materials cater to pharmaceuticals and chemicals.
2. Operational Efficiency: From Warehouse to Retail
2.1 Logistics-Optimized Design Features
Parameter | VidePak Standard | Industry Average |
---|---|---|
Load Capacity | 500–2,000 kg | 300–1,500 kg |
Stacking Height | 6 meters | 4 meters |
Moisture Resistance | ≤0.8% weight gain (72h) | 2–3% weight gain |
Print Durability | ΔE ≤1.5 after 1k UV hours | ΔE ≤3.0 |
FAQs:
Q: How do FIBC bags compare to traditional wooden pallets in cost?
A: FIBC bags reduce storage costs by 40% due to collapsible design and 30% lighter weight, while offering 2x faster loading via RFID-tagged handles.
Q: Can bags withstand -20°C freezer storage?
A: Yes. Impact copolymer PP retains 85% tensile strength at -20°C, validated by EN ISO 1873-1.
2.2 Branding Through Precision Printing
VidePak’s 30+ printing machines use CMYK+Pantone systems for high-definition branding:
- QR Code Integration: Enables batch tracking via SAP EWM, reducing inventory errors by 18%.
- Eco-Friendly Inks: Water-based pigments achieve food-safe compliance (FDA 21 CFR) and resist fading in humid environments.
3. Sustainability and Global Compliance
3.1 Reducing Environmental Footprints
- Recycled PP Blends: VidePak’s 2025 initiative integrates 30% post-consumer recycled PP, cutting carbon emissions by 15% per bag.
- Reusable Designs: Bags withstand 10+ lifecycle uses, diverting 50 tons of waste annually for a US construction client.
3.2 Certifications Across Markets
Region | Key Standard | VidePak’s Compliance |
---|---|---|
EU | EN 13589 (waterproofing) | PE liners + BOPP lamination |
North America | ASTM D5265 (tear resistance) | 14×14 weave density (≥25 J puncture) |
Asia | JIS Z0237 (compression) | Block-bottom design + 6:1 safety factor |
4. Case Study: Transforming Retail Logistics for a Global Pet Food Brand
A multinational pet food company faced 12% product loss during transatlantic shipping. VidePak’s solution:
- Design: Baffle bags with anti-static liners and 4-color UV-resistant prints.
- Outcome: Zero spillage over 10,000 km, with a 20% sales boost from shelf-ready branding.
5. Future Trends: Smart Packaging and Automation
VidePak’s R&D pipeline includes:
- IoT-Enabled Bags: NFC tags for real-time temperature/humidity monitoring (piloted Q3 2025).
- AI-Driven Production: Predictive maintenance on Starlinger looms cuts downtime by 25%.
For insights into sustainable FIBC solutions, explore our innovations in Sustainable FIBC Bulk Bags: Compliance and Ethical Practices and Valve Bags: Quality and Precision with Starlinger Technology.
6. Conclusion
FIBC bulk bags are not mere packaging—they are strategic tools for modern retail. By combining ASTM-grade durability, hyper-customization, and IoT-ready designs, VidePak delivers solutions that transcend storage, turning logistical challenges into branding opportunities. As global retail grows at 4.7% CAGR, VidePak’s fusion of innovation and compliance positions it as the partner of choice for smarter, safer, and sustainable operations.
Data sources: EN ISO 1873-1, ASTM D5265, and VidePak’s 2024 production logs. Technical insights derived from Polymer Degradation and Stability (Vol. 221, 2025) and Starlinger’s extrusion manuals.