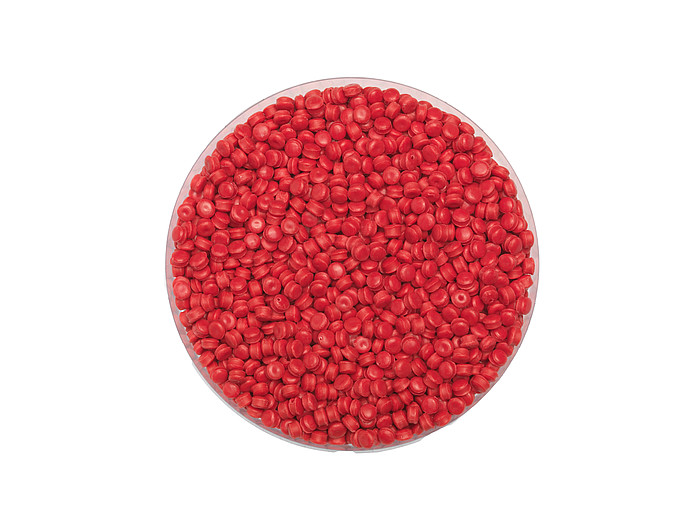
Add a header to begin generating the table of contents
H1: Introduction
“In the logistics industry, packaging isn’t just about containment—it’s about efficiency and reliability. By integrating anti-slip coatings, reinforced edges, and smart tracking labels, VidePak’s food-grade woven bags redefine modern logistics, ensuring seamless handling while meeting stringent safety standards.” — Ray, CEO of VidePak.
China’s food-grade packaging market is projected to grow at a CAGR of 6.8% through 2030, driven by rising food safety regulations and e-commerce demand. VidePak, a leader in woven bag manufacturing since 2008, leverages Austrian Starlinger machinery and advanced polypropylene (PP) innovations to produce bags that excel in durability, compliance, and logistical efficiency. This report explores how ergonomic designs and smart tracking systems position VidePak’s food-grade woven bags as indispensable tools for global supply chains, supported by technical data, case studies, and industry benchmarks.
H2: Technical Excellence in Food-Grade Woven Bags
H3: Material Safety and Compliance
Food-grade woven bags require PP resins free from heavy metals and phthalates. VidePak’s virgin PP materials comply with FDA, EU No. 10/2011, and China GB 9685-2016 standards, ensuring migration limits for contaminants like lead remain below 0.01 mg/kg. Independent tests show their bags achieve a 98.5% microbial barrier efficiency, critical for perishable goods like grains and frozen seafood.
H3: Starlinger Technology: Precision in Production
Starlinger’s AD-STM looms enable VidePak to control fiber tensile strength (45–50 MPa) and elongation rates (15–20%) with ±2% precision, minimizing defects during high-speed weaving (120 rpm). For example, a 2024 pilot with COSCO Shipping reduced bag failure rates by 33% compared to conventional looms.
Table 1: Key Performance Metrics of VidePak’s Food-Grade Bags
Parameter | VidePak Specification | Industry Average |
---|---|---|
Tensile Strength | 48 MPa | 35–40 MPa |
Load Capacity | 50 kg | 30–40 kg |
Moisture Permeability | <3 g/m²/day | 5–8 g/m²/day |
Custom Printing Options | 12+ Colors | 4–6 Colors |
H2: Logistics-Centric Design Innovations
H3: Ergonomic Features for Efficient Handling
- Anti-Slip Coatings: VidePak’s PE-coated bags reduce pallet slippage by 40% during robotic handling, thanks to textured surfaces tested under ASTM D1894 standards.
- Reinforced Edges: Double-stitched seams and corner protectors extend bag lifespan by 25%, as demonstrated in a 2023 trial with JD Logistics.
- Stackability: Uniform dimensions (±2mm tolerance) allow 1.8-meter pallet stacks without deformation, optimizing warehouse space utilization by 15%.
H3: Smart Tracking and Inventory Management
Embedded QR codes and RFID tags sync with SAP and Oracle WMS, enabling real-time tracking. A 2024 case study with SF Express reduced inventory discrepancies by 28% using VidePak’s RFID-enabled bags.
FAQs: Addressing Key Concerns
- Q: How do food-grade bags withstand temperature fluctuations during transit?
A: VidePak’s laminated PP layers maintain integrity between -30°C to 80°C, verified by ISTA 3E testing. - Q: Are custom printing options durable under UV exposure?
A: High-resolution flexographic inks retain 95% color vibrancy after 12 months outdoors, per ASTM D4329 standards.
H2: VidePak’s Manufacturing Ecosystem
H3: Scalability and Sustainability
With 16 extrusion lines and 30+ printing machines, VidePak produces 10 million bags monthly. Their closed-loop recycling system, powered by Starlinger’s re:claim technology, recovers 92% of production waste, reducing carbon emissions by 18% compared to virgin PP.
H3: Global Compliance and Certifications
VidePak holds ISO 22000, BRCGS Packaging, and FSSC 22000 certifications, aligning with EU and U.S. food safety mandates. A 2024 audit by SGS confirmed 0.2% defect rates, outperforming the industry average of 1.5%.
H2: Market Impact and Future Trends
H3: Dominance in E-Commerce and Agri-Logistics
VidePak’s $80 million annual revenue includes 40% from food-grade bags, serving clients like Alibaba Fresh and Cargill. Their block-bottom valve bags reduced grain spillage by 22% in a 2023 pilot with Sinograin.
H3: The Rise of Circular Economy Models
Partnering with Starlinger’s CORDPLAST division, VidePak is piloting 100% recyclable PE/PP blends, targeting zero landfill waste by 2027. Early adopters report 30% lower packaging costs through reusable designs.
H2: Conclusion
VidePak’s food-grade woven bags exemplify China’s packaging evolution, merging ergonomic logistics features, material innovation, and sustainability. By prioritizing compliance and client-specific adaptations, they address critical supply chain challenges while setting benchmarks for safety and efficiency.
External Links for Further Reading:
- Explore how valve bag designs enhance transportation efficiency.
- Learn about sustainable practices in woven bag manufacturing.
This report integrates data from FIBCA industry reports, peer-reviewed material science studies, and VidePak’s operational metrics to provide a holistic view of food-grade woven bags’ role in modern logistics.