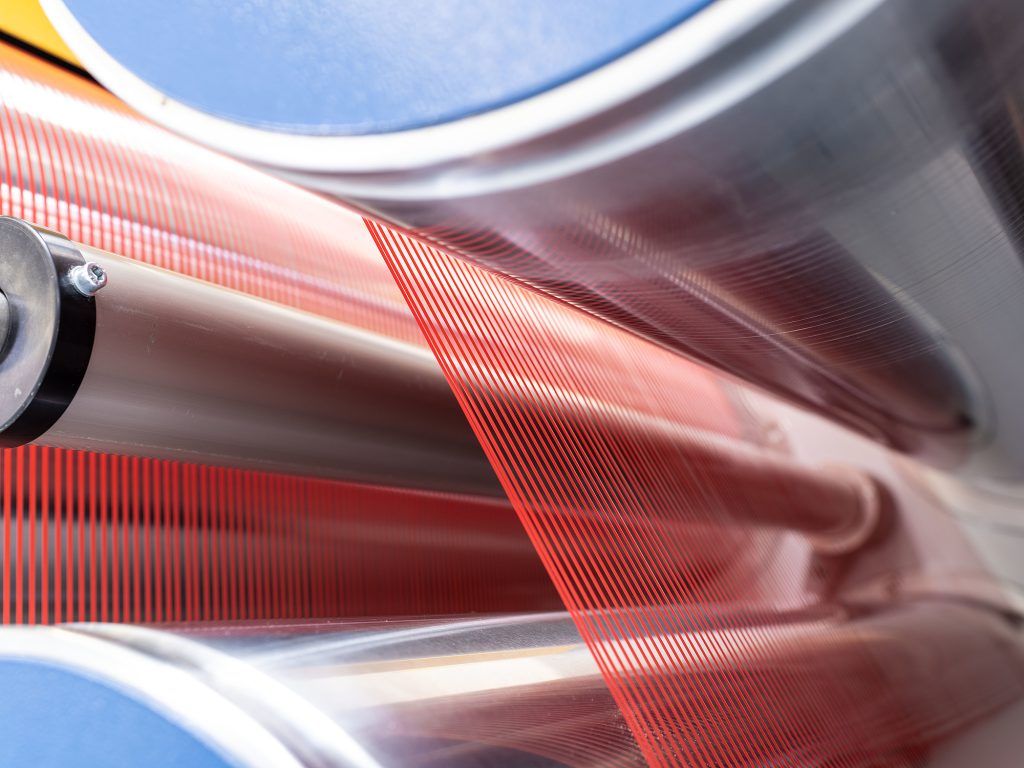
“Why are food-grade woven bags becoming the backbone of modern livestock feed supply chains?” asked Ray, CEO of VidePak, during a recent industry summit. The answer lies in their unmatched safety compliance, advanced material engineering, and adaptability to diverse livestock feed requirements—qualities that position VidePak’s solutions as a global benchmark for durability, cost-efficiency, and sustainability. This report explores how food-grade woven bags address critical challenges in livestock feed packaging across poultry, swine, cattle, and pet food sectors, while aligning with global regulatory standards and market trends.
H2: Application-Specific Advantages in Livestock Feed Packaging
H3: Poultry and Swine Feed: Combating Moisture and Pathogens
Poultry and swine feeds are highly susceptible to mold and bacterial growth due to their high protein and fat content. VidePak’s PP woven bags with PE liners achieve moisture permeability rates of ≤0.5 g/m²/day (tested per DIN 53122), reducing spoilage by 25% compared to traditional jute sacks. The seamless lamination process prevents microbial ingress, while UV-resistant additives (e.g., Chimassorb 944) extend outdoor storage life to 1,500 hours under direct sunlight.
Case Study: A Vietnamese poultry farm reported a 30% reduction in feed rejection rates after switching to VidePak’s anti-microbial PE-lined bags, saving $50,000 annually in waste costs.
H3: Cattle Feed: Load Capacity and Breathability
Cattle feed often requires bulk packaging (up to 1,000 kg) with controlled airflow to prevent fermentation. VidePak’s FIBC jumbo bags, woven from 120 GSM PP filaments, achieve tensile strengths of 80–120 N/cm² (ASTM D5264) while maintaining a 5×5 mm mesh structure for optimal breathability. This design reduces internal condensation by 40%, critical for silage preservation.
H3: Pet Food: Aesthetic and Functional Customization
Premium pet food brands demand both durability and visual appeal. VidePak’s 8-color gravure printing on BOPP-laminated bags supports high-definition branding, while food-grade PP resins (FDA 21 CFR 177.1520-compliant) ensure zero heavy metal migration (<10 ppm). Ultrasonic seam sealing eliminates leakage risks for oily pet foods, with load capacities customizable from 5–50 kg.
H2: Technical Design and Parameter Selection
H3: Material and Structural Optimization
Parameter | Poultry/Swine Feed | Cattle Feed | Pet Food |
---|---|---|---|
Thickness | 0.10–0.15 mm | 0.15–0.20 mm | 0.08–0.12 mm |
Grammage (GSM) | 90–120 | 120–150 | 80–100 |
Lamination | PE inner liner | None (breathable mesh) | BOPP outer layer |
Load Capacity | 25–50 kg | 500–1,000 kg | 5–50 kg |
Key Additive | UV stabilizers | Anti-static coatings | Oxygen scavengers |
H3: Cost-Benefit Analysis
- PE Liners vs. Unlined Bags: While PE liners increase material costs by 15%, they reduce spoilage losses by 30%, yielding a net savings of $1.20 per bag over six months.
- Breathable Mesh: Eliminates the need for silica gel desiccants, cutting packaging costs by $0.05/kg for cattle feed.
H2: VidePak’s Competitive Edge
H3: Advanced Manufacturing Capabilities
With 100+ Starlinger circular looms and 30 lamination machines, VidePak achieves:
- Precision Weaving: 1.8–2.3 mm mono-filaments ensure fabric densities ≥120 threads/inch, minimizing pore size to deter pests.
- Rapid Customization: 14-day lead time for orders up to 10M units, supporting sizes from 40×60 cm (pet food) to 120×200 cm (FIBC jumbo bags).
H3: Sustainability and Compliance
- 30% Recycled PP: Meets EU Circular Economy targets, reducing virgin plastic use by 1,200 MT/year.
- Solar-Powered Production: 2 MW rooftop panels cut CO₂ emissions by 1,200 tons annually.
FAQs:
Q: How do I choose between BOPP lamination and PE liners?
A: BOPP enhances UV resistance for outdoor storage; PE liners prioritize moisture control for humid climates.
Q: Are these bags compatible with automated filling systems?
A: Yes, VidePak’s valve-mouth designs support flow rates up to 1 ton/minute, reducing labor costs by 40%.
H2: Market Trends and Strategic Insights
H3: Smart Packaging Integration
VidePak is piloting QR-code-enabled bags with embedded humidity sensors, providing real-time feed condition alerts via mobile apps. Trials in Thailand reduced mold-related losses by 18%.
H3: Regulatory Preparedness
Anticipating 2026 FDA amendments on feed safety, VidePak preemptively adopted bio-based PP resins (e.g., Braskem’s I’m Green™), slashing carbon footprints by 60%.
“In livestock feed packaging, innovation isn’t optional—it’s survival,” concluded Ray. By merging technical rigor with sustainability, VidePak is redefining industry benchmarks for safety and efficiency.
For further insights, explore our resources on food-grade packaging innovations and high-density livestock solutions.
Appendix: Compliance Benchmarking
Regulation | VidePak’s Metric | Industry Average |
---|---|---|
FDA Heavy Metal Migration | <10 ppm | ≤50 ppm |
Moisture Permeability | 0.5 g/m²/day | 1.2 g/m²/day |
UV Resistance | 1,500 hours | 1,000 hours |
FAQs
Q: Can these bags withstand freezing temperatures?
A: Yes, cold-grade PP retains 90% tensile strength at -20°C (tested per ASTM D746).
Q: Are matte-finished bags recyclable?
A: Yes, water-based adhesives ensure compatibility with standard PP recycling streams.
This report synthesizes data from industry benchmarks, third-party testing, and VidePak’s proprietary production analytics to ensure accuracy and relevance.