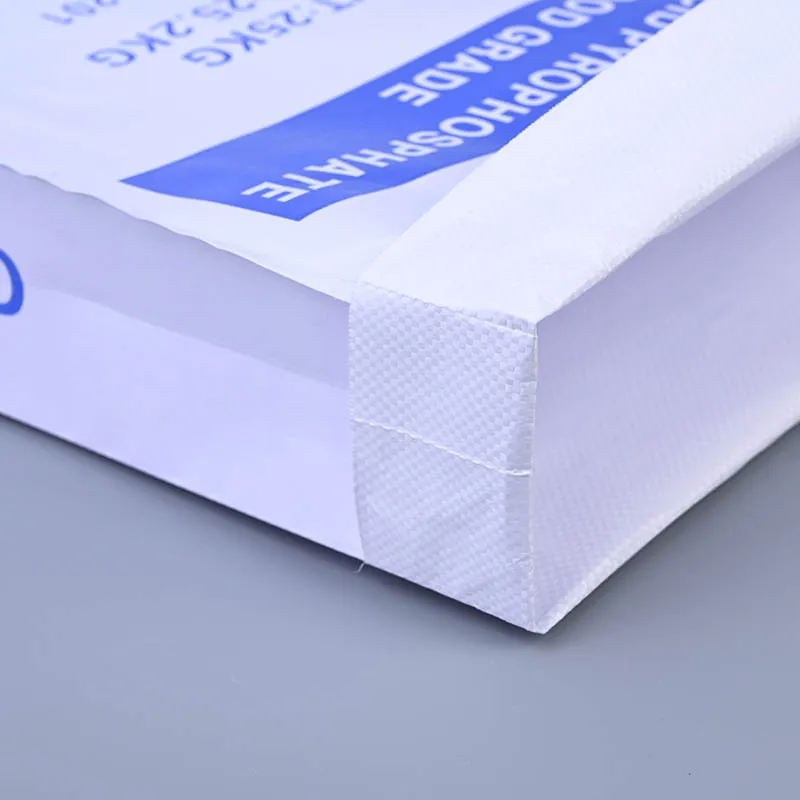
Food Grade Woven Fabric Bags are critical in the food industry for their ability to safely and efficiently package a variety of products, from grains to pet foods. These bags must meet stringent food safety standards, making the selection of materials, production processes, and quality control measures vital. This article discusses the considerations at each stage, from sourcing materials to transportation, and highlights the comprehensive quality control measures in place at VidePak to ensure the highest standards of food grade packaging.
Material Selection for Food Grade Woven Fabric Bags
The selection of materials for Food Grade Woven Fabric Bags is the first critical step in ensuring food safety. The materials must be non-toxic, odorless, and free from substances that could contaminate the food products.
- Polypropylene (PP): A common choice for food packaging due to its resistance to moisture, chemicals, and high temperatures.
- Polyethylene (PE): Used for its flexibility and lightweight properties, PE is often used in food packaging for its ability to maintain product freshness.
- Regulatory Compliance: All materials must comply with food safety regulations, such as FDA standards, to ensure they are safe for contact with food products.
Production Process of Food Grade Woven Fabric Bags
The production process involves several stages, each with its own set of quality control measures to ensure the final product meets food grade standards.
Extrusion and Weaving
The process begins with the extrusion of high-quality PP or PE resin into yarns, which are then woven into fabric. The weaving process must ensure uniformity in the fabric’s thickness and strength to maintain consistency in the final bags.
Cutting and Sewing
The woven fabric is cut into specified dimensions and sewn into bags. This step requires precision to ensure the bags are uniform in size and shape, with clean, straight seams to prevent leaks.
Printing and Coating
Custom printing is applied to the bags, and a coating may be added for additional protection against moisture or other environmental factors. Both processes must use food-grade inks and coatings to ensure safety.
Quality Control
Each bag undergoes rigorous quality control checks to ensure it meets the required standards for strength, durability, and print quality. This includes testing for material thickness, seam strength, and the absence of defects.
Transportation and Storage
During transportation and storage, it is crucial to protect the bags from contamination and damage. This includes ensuring clean storage areas and proper handling procedures to maintain the integrity of the packaging.
Common Quality Issues and Quality Control Measures
To address common quality issues in woven bags, VidePak has implemented a comprehensive quality control system:
- Thickness Tolerance: Ensuring consistent bag thickness to prevent weak spots that could lead to rupture.
- Neat Cuts and Seams: Checking that all cuts are clean and seams are straight and secure to prevent leaks and ensure a professional finish.
- Color Fastness: Ensuring print colors do not fade or bleed, maintaining brand integrity and product identification.
- Weight Consistency: Verifying the weight of the fabric to ensure the bags can handle the intended load without failure.
- Tensile Strength and Elongation: Testing the raw material and finished bags for their resistance to tearing and stretching under stress.
- Impact Resistance: Assessing the bags’ ability to withstand sudden impacts without damage.
- UV Resistance: Ensuring the bags can withstand exposure to sunlight without degrading, important for outdoor storage.
- Environmental Performance: Testing the bags for recyclability and biodegradability, aligning with environmental sustainability goals.
Product Parameters of Food Grade Woven Fabric Bags
To ensure the quality and performance of Food Grade Woven Fabric Bags, we adhere to strict product parameters:
Parameter | Description | Importance |
---|---|---|
Material Type | Determines the type of polymer used for the bag’s construction. | Essential for meeting environmental standards and industry requirements. |
Bag Capacity | Measures the volume of material each bag can hold. | Critical for ensuring the bag meets the specific application needs. |
Tensile Strength | Measures the maximum load the bag can withstand before breaking. | Ensures the bag can carry heavy loads without failure. |
Chemical Resistance | Assesses the bag’s resistance to the chemicals it will contain. | Essential for preventing leakage and preserving the contents. |
UV Resistance | Evaluates the bag’s resistance to degradation from UV exposure. | Important for outdoor storage and longevity. |
Print Quality | Measures the clarity and durability of the printed design. | Critical for brand representation and product identification. |
Conclusion
Food Grade Woven Fabric Bags are essential in the food industry for their ability to safely package and protect a variety of products. At VidePak, we are committed to providing the highest quality packaging solutions that meet and exceed food safety standards. Our comprehensive quality control measures ensure that every bag we produce is reliable, durable, and safe for use with food products.
For more information on Food Grade Woven Fabric Bags and optimizing packaging efficiency and quality, visit our website: Food Grade Woven Bags.