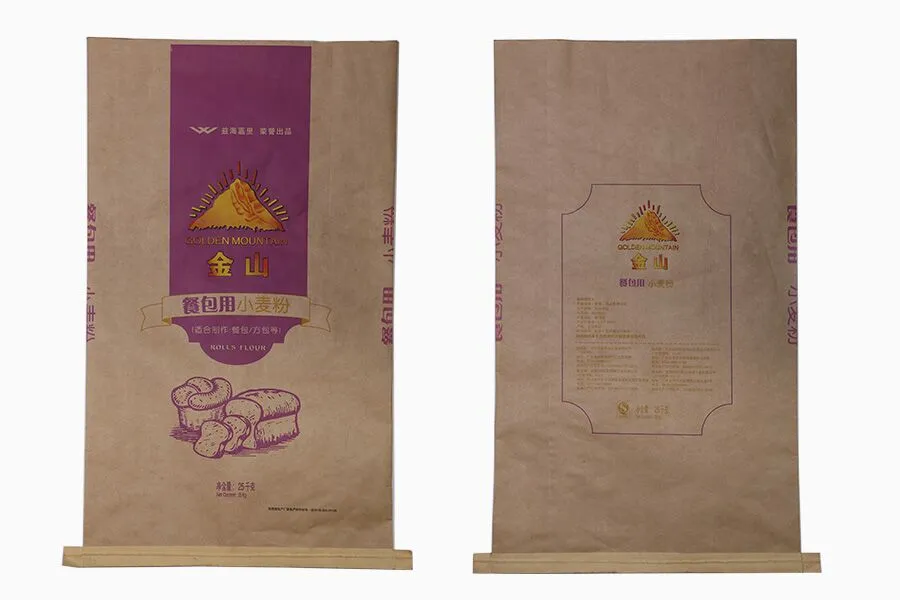
The demand for safe, durable, and efficient packaging solutions in the food industry has never been higher. Food Grade Woven Fabric Bags have emerged as a key packaging option for various food products, including grains, flour, sugar, and even some processed goods. These bags, often made from Food Grade Polypropylene (PP), offer exceptional strength, moisture protection, and the ability to be customized with features such as PE liners and a pearlescent film coating.
In this article, we will explore the entire lifecycle of Food Grade Woven Fabric Bags, from material selection and production to packaging and transportation. We will discuss the key considerations at each stage to ensure that the bags meet stringent food-grade standards. Additionally, we will highlight how combining PP woven fabric with PE liners and additional coatings enhances the bags’ functionality, providing moisture resistance, aesthetic appeal, and barrier protection.
What Are Food Grade Woven Fabric Bags?
Food Grade Woven Fabric Bags are made from polypropylene (PP) woven fabric and are designed to safely store and transport food products. They are widely used for packaging bulk commodities such as rice, flour, sugar, and grains, as well as processed food items. The term “food grade” refers to the fact that these bags meet the stringent safety standards required for direct contact with food products.
The main advantages of Food Grade Woven Fabric Bags include:
- Strength and Durability: The woven structure of PP provides high tensile strength, making the bags capable of handling heavy loads without breaking.
- Moisture Resistance: Adding PE liners and coatings can enhance the bag’s ability to protect food products from moisture and contaminants.
- Customizability: The bags can be produced in various sizes, with options for multiple layers, coatings, and closures to meet specific packaging needs.
Material Selection for Food Grade Woven Fabric Bags
Selecting the right materials is the foundation of producing Food Grade Woven sacks that meet food safety standards. Several critical factors must be considered during the material selection process, including the type of resin, additives, and coatings used in the bag’s construction.
1. Virgin Polypropylene (PP) Resin
The primary material used in Food Grade Woven Fabric Bags is virgin polypropylene (PP) resin. Virgin PP is preferred over recycled material because it ensures purity and reduces the risk of contamination. Using virgin PP also guarantees that the material is free from harmful substances that could affect the safety and quality of the food products stored within the bags.
- Key Properties of Virgin PP for Food Grade Bags:
- High tensile strength to support heavy loads.
- Chemical inertness, ensuring no interaction with the food contents.
- Light weight, making it ideal for bulk transportation.
2. PE Liners for Added Protection
Food Grade Polypropylene Bags often include an inner liner made from polyethylene (PE). PE liners provide an additional layer of protection, ensuring that the contents of the bag are shielded from moisture, dust, and other contaminants. This is especially important for hygroscopic food products like flour and sugar that can degrade when exposed to moisture.
- Advantages of PE Liners:
- Enhanced moisture resistance.
- Improved barrier protection against contaminants.
- Compatibility with food-grade standards for direct contact with food items.
3. Coatings and Laminations
To further enhance the performance of Food Grade PP Bags, manufacturers often apply external coatings, such as a pearlescent (or “pearlescent”) film. This coating not only gives the bag an aesthetically appealing finish but also improves its barrier properties, making it more resistant to moisture, oils, and other environmental factors.
- Pearlescent Film Coating Benefits:
- Provides a smooth, glossy finish that improves the bag’s visual appeal.
- Enhances moisture and oil resistance, protecting the contents during storage and transportation.
- Adds an extra layer of strength, further improving the bag’s durability.
Production Considerations for Food Grade Woven Fabric Bags
Once the appropriate materials have been selected, the production process must be carefully managed to ensure that the bags meet food-grade standards. Below are the key steps and considerations during the manufacturing process:
1. Extrusion and Weaving of PP Fabric
The production process begins with the extrusion of polypropylene resin into fine threads, which are then woven into a fabric. The weaving process must be closely monitored to ensure that the fabric maintains consistent strength and durability. Any weaknesses in the weave could compromise the bag’s ability to protect the food products inside.
2. Adding the PE Liner
After the PP fabric is woven, a PE liner is inserted into the bag. This liner serves as a barrier between the food products and the external environment. The liner is typically heat-sealed or sewn into the bag, depending on the specific design.
3. Lamination and Coating
To improve the moisture resistance and overall durability of the bag, a lamination process is applied. A pearlescent or clear film is laminated onto the outer surface of the bag, creating a smooth, moisture-resistant barrier. This lamination also enhances the bag’s appearance, making it suitable for retail packaging.
4. Customization Options
Food Grade Woven sacks can be customized in various ways to meet the needs of different food producers. For example, bags can be produced with different types of closures, such as open-mouth, valve, or zipper designs. Additionally, bags can be printed with high-quality graphics, logos, and branding information using flexographic or rotogravure printing techniques.
Packaging and Transportation
Once the bags are produced, they must be packaged and transported in a way that maintains their food-grade status. The key considerations during this stage include:
1. Clean and Hygienic Handling
During the packaging process, it is crucial to ensure that the bags are handled in a clean and hygienic environment. Any contamination during this stage could compromise the food-grade certification of the bags.
2. Proper Storage Conditions
To maintain the integrity of Food Grade Poly bags, they should be stored in a cool, dry environment. Exposure to heat or moisture could degrade the quality of the bags, potentially affecting their ability to protect the food products they contain.
3. Secure Transportation
During transportation, Food Grade Polypropylene Bags must be securely packed to prevent damage. Heavy-duty pallets, shrink wrapping, or stretch films can be used to secure the bags during transit, ensuring that they arrive at their destination in perfect condition.
Table 1: Key Parameters for Food Grade Woven Fabric Bags
Parameter | Description | Benefits |
---|---|---|
Material Composition | Virgin PP with optional PE liner | Ensures food safety and contamination-free packaging |
Moisture Resistance | PE liner and lamination | Protects food from moisture and contaminants |
Tensile Strength | High-strength woven PP fabric | Can hold heavy food products like grains and flour |
Customization | Printing, size, closure options | Tailored to specific product and branding needs |
Lamination | Pearlescent or clear film coating | Enhances durability and aesthetic appeal |
Load Capacity | Up to 50 kg | Suitable for bulk packaging of food items |
Ensuring Food Grade Standards
Producing Food Grade Woven Fabric Bags requires strict adherence to industry standards and regulations. Below are the key steps taken to ensure that these bags meet food-grade standards:
1. Raw Material Certification
Before production begins, all raw materials, including PP resin and PE liners, must be certified as food-grade by relevant regulatory bodies, such as the FDA or the European Food Safety Authority (EFSA). This certification ensures that the materials are safe for direct contact with food.
2. Hygienic Manufacturing Environment
The manufacturing environment must be kept clean and sanitary at all times. Equipment should be regularly cleaned, and employees must follow strict hygiene protocols, including wearing gloves and hairnets, to prevent contamination.
3. Quality Control Testing
Throughout the production process, samples of the bags are tested for quality control. These tests include tensile strength testing, moisture resistance testing, and checks for contamination. Bags that do not meet the required standards are rejected and not sent to customers.
4. Proper Labeling and Documentation
Once the bags are produced, they must be properly labeled as food-grade. This includes providing documentation to customers, certifying that the bags meet the required food safety standards.
Conclusion
Food Grade Woven Fabric Bags offer a robust, safe, and customizable packaging solution for the food industry. From selecting the right materials to ensuring hygienic production and secure transportation, every stage of the process is critical to meeting food-grade standards. By combining PP woven fabric with PE liners and pearlescent film coatings, manufacturers can produce bags that not only meet food safety requirements but also provide additional benefits such as moisture resistance, durability, and enhanced aesthetics.
In today’s competitive food packaging industry, ensuring that packaging solutions meet the highest standards of safety, durability, and functionality is more important than ever. Food Grade PP Bags stand out as a reliable choice, offering a combination of strength, protection, and visual appeal that meets the diverse needs of the food sector.