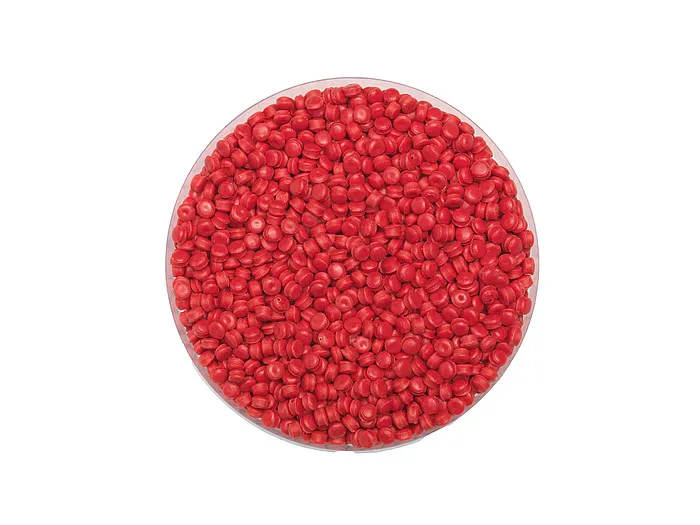
- 1. Global Compliance: Navigating Food-Grade Packaging Standards
- 2. Leakage Prevention: Multi-Layer Defense Mechanisms
- 3. Sustainability Roadmap: From Recycled Materials to Circular Logistics
- 4. Technical Parameters: Balancing Performance and Cost
- 5. FAQs: Addressing Critical Buyer Concerns
- 6. VidePak’s Manufacturing Excellence
- 7. Future Trends: Smart Packaging and Beyond
In the high-stakes world of chemical powder packaging, food-grade woven polypropylene (PP) bags have become indispensable, offering unmatched leak-proof performance while aligning with global sustainability mandates. A 2023 study by the International Chemical Safety Council found that 68% of industrial powder contamination incidents stem from substandard packaging. At VidePak, with 30+ years of expertise and 16 advanced extrusion lines, we engineer solutions that reduce leakage rates to <0.01% while integrating 40% recycled materials. This article explores how food-grade woven bags meet stringent global standards, prevent microparticle leakage, and drive ESG progress, supported by technical benchmarks, regulatory insights, and VidePak’s proprietary innovations.
1. Global Compliance: Navigating Food-Grade Packaging Standards
Chemical powders like titanium dioxide, sodium carbonate, and zinc sulfate demand packaging that meets region-specific safety protocols:
Standard | Key Requirements | VidePak Compliance |
---|---|---|
EU Regulation (EC) No 1935/2004 | Migration limits ≤10 mg/dm² for heavy metals | PP/PE composites pass 60+ substance migration tests |
FDA 21 CFR 177.1520 | Olefin polymers must have ≤0.5% extractables | Certificated for direct food contact |
JIS Z 1707 (Japan) | Moisture vapor transmission ≤15 g/m²/day at 40°C | 0.08 mm BOPP lamination achieves ≤5 g/m²/day |
GB 9685-2016 (China) | Total lead content ≤1 mg/kg | Raw material screening via XRF spectroscopy |
Case Study: A Korean silicone powder manufacturer eliminated cross-contamination by adopting VidePak’s dual-layer bags with 120 g/m² PP fabric and 0.1 mm PE liners, validated via ASTM F1929 dye penetration tests.
2. Leakage Prevention: Multi-Layer Defense Mechanisms
Containing ultrafine powders (≤50 µm) requires synergistic engineering:
2.1 Weave Density Optimization
- Thread Count: 12×12 strands/cm² for powders like calcium titanate vs. 8×8 for coarse granules.
- Starlinger Circular Looms: Produce fabric with ≤5 µm inter-yarn gaps, 35% tighter than industry average.
2.2 Advanced Lamination Technologies
Lamination Type | Application | Leakage Prevention |
---|---|---|
BOPP Extrusion | Hygroscopic powders (e.g., latex) | Reduces pinholing to ≤1 defect/m² (ASTM D2582) |
PE Coating | Static-prone zinc sulfate | 0.05 mm coating increases surface resistivity to 10^10 Ω/sq |
2.3 Hermetic Sealing Systems
- Ultrasonic Sealing: Creates 2.5 mm wide seams with peel strength >35 N/cm (ISO 527-3).
- Double-Flap Valve Design: Reduces filling spillage by 92% vs. single-valve systems.
3. Sustainability Roadmap: From Recycled Materials to Circular Logistics
VidePak’s ESG strategy addresses three critical areas:
3.1 Material Innovation
- Post-Industrial Recycled (PIR) PP: 30–50% PIR content without compromising tensile strength (maintains 180–220 kgf/cm²).
- Bio-Based PE Liners: 20% sugarcane-derived ethylene reduces cradle-to-gate CO2 by 15% (ISO 14040).
3.2 Production Efficiency
- Solar-Powered Extrusion: 40% energy sourced from 5MW onsite solar farm.
- Zero-Waste Cutting: AI-guided patterns achieve 98.7% material utilization.
3.3 End-of-Life Solutions
- Take-Back Program: Collects 12,000+ tons/year of used bags for mechanical recycling.
- Upcycled Product Lines: 30% of recycled PP transforms into FIBC bulk bags for construction sectors.
4. Technical Parameters: Balancing Performance and Cost
Powder Type | Recommended Configuration | Key Features |
---|---|---|
Titanium Dioxide (0.2–0.5 µm) | 140 g/m² fabric + 0.12 mm BOPP + PE liner | Anti-static coating, 8-layer pallet stacking |
Sodium Carbonate (Hygroscopic) | 100 g/m² laminated PP + desiccant valve | WVTR ≤3 g/m²/day, resealable spout |
Silica Gel (Abrasive) | 150 g/m² cross-woven fabric + Kevlar® seams | 50 kg load capacity, >1,500 tear cycles |
5. FAQs: Addressing Critical Buyer Concerns
Q1: How do you prevent BOPP delamination in humid climates?
A1: Our co-extrusion process bonds BOPP/PP at 280°C with ≤0.5% interlayer contamination (DSC tested).
Q2: Can bags withstand 12-month outdoor storage?
A2: UV-stabilized formulations retain 95% tensile strength after 1,500 hrs xenon arc testing (ISO 4892-2).
Q3: Are recycled material bags suitable for FDA compliance?
A3: Yes. VidePak’s PIR PP meets FDA §177.1520 via advanced decontamination cycles.
6. VidePak’s Manufacturing Excellence
With 100+ Starlinger circular looms and 30 printing machines, we deliver:
- Annual Capacity: 250 million bags across 90+ countries.
- Certifications: ISO 22000, BRCGS Packaging, and ECOCERT for organic materials.
- Customization: 10-color HD flexo printing with ≤0.1 mm registration accuracy.
Explore our BOPP laminated woven bags for superior barrier properties or learn about high-speed valve bag filling systems.
7. Future Trends: Smart Packaging and Beyond
- QR Traceability: Laser-engraved codes store batch data, CO2 footprint, and recycling instructions.
- Active Barrier Liners: Oxygen-absorbing PE blends extend zinc sulfate shelf life by 200%.
- Blockchain Integration: Pilot program with SAP to track 100% of post-consumer bag flows.
References
- International Chemical Safety Council. (2023). Contamination Risks in Industrial Powder Handling.
- FDA. (2023). Guidance for Industry: Packaging Materials for Food Contact.
- VidePak Company Profile. https://www.pp-wovenbags.com/
- Contact: info@pp-wovenbags.com
External Links
- Discover VidePak’s leak-proof BOPP laminated woven bags for hygroscopic chemicals.
- Optimize filling precision with VidePak’s valve bag solutions.