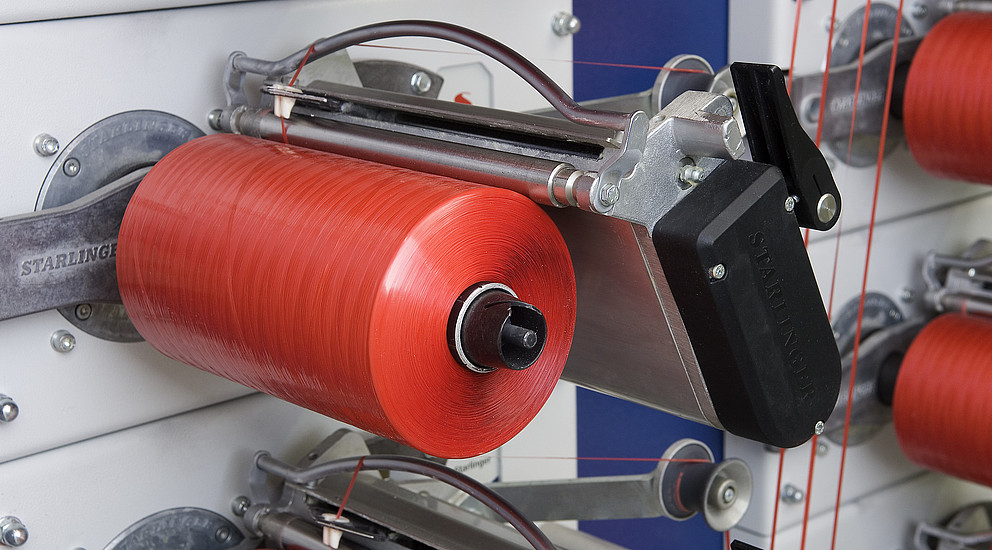
Form-fill-seal (FFS) woven bags are a vital part of packaging for many industries, particularly those dealing with bulk materials like cement, sand, plaster powder, and gypsum. These bags provide essential protection during transport and storage, ensuring that the materials stay intact and undamaged. In this article, we’ll discuss the key design factors that influence the effectiveness of FFS woven bags, explain why these factors matter, and highlight the importance of following international standards.
What Makes FFS Woven Bags Special?
FFS woven bags are made from high-density polypropylene (HDPE) or low-density polyethylene (LDPE), which are woven together to create a strong, durable fabric. The “form-fill-seal” process refers to the automated system that shapes, fills, and seals the bags in one continuous motion. This process helps ensure high-quality, efficient packaging for bulk materials.
Here are some key features of FFS woven bags:
- Strength and Durability: The woven fabric offers superior strength, which is essential for holding heavy materials without tearing. For instance, cement, which can weigh up to 50 kg per bag, needs a robust package that won’t split under pressure.
- Moisture Resistance: Many FFS woven bags are lined with polyethylene (PE) or laminated films to prevent moisture from seeping in, especially when packaging moisture-sensitive products like cement or gypsum.
- Leak-Proof Design: These bags are designed to keep fine powders, such as plaster and gypsum, from leaking out during storage or transport. This is especially important for industries where product loss can be costly.
- Cost-Effective: FFS bags are a cost-efficient packaging option, offering durability and protection at a lower cost than other alternatives.
Protecting Materials During Transport
FFS woven bags play an important role in protecting bulk materials during transport and storage. Products like cement, plaster powder, and gypsum are fragile and can easily become damaged or contaminated if not packaged correctly.
Take cement, for example. Cement is highly sensitive to moisture, and if it becomes damp, it can harden prematurely, making it unusable. Using a moisture-resistant FFS woven bag prevents this from happening, ensuring the cement remains dry and ready for use. Similarly, fine powders like plaster or gypsum can easily spill out of improperly sealed packaging, resulting in product loss. The strong, secure seals of FFS woven bags prevent this issue.
Choosing the Right FFS Bag for Your Needs
When selecting FFS woven bags, it’s crucial to choose the right material and design based on the specific requirements of the product being packaged. There are global standards that can help guide this decision-making process, ensuring that the bags are strong, secure, and compliant with industry regulations.
European Standards (EN)
In Europe, packaging regulations, such as EN 15593, require that materials used in packaging meet hygiene and safety standards. For example, FFS woven bags used for cement must be strong enough to hold up to 50 kg of weight and resistant to water, so the cement doesn’t harden prematurely. Bags must also be durable enough to withstand harsh transportation conditions.
American Standards (ASTM)
In the United States, ASTM F88 is a standard for testing the strength of seals in flexible packaging. This is crucial for FFS woven bags used to package fine powders like gypsum, as the seal must remain intact to prevent leakage. ASTM standards ensure that the bags can endure the stresses of handling and transport without breaking open.
Japanese Standards (JIS)
Japan’s packaging standards (JIS Z 0238) place a strong emphasis on environmental sustainability. FFS woven bags sold in Japan must be recyclable and have the necessary strength to protect products while minimizing environmental impact. This makes the choice of materials especially important.
Australian Standards (AS)
Australia’s AS 4130 standards focus on the durability of packaging in outdoor environments. FFS woven bags intended for construction use, for example, must be UV-resistant to prevent degradation when exposed to sunlight over time.
Important Design Considerations
When designing FFS woven bags, several factors must be taken into account to ensure they meet both performance and safety standards.
- Material Selection: Choosing the right material is essential for ensuring the bag’s strength and moisture resistance. Polypropylene (PP) is commonly used for its durability, while polyethylene (PE) liners are often added to provide an additional layer of moisture protection.
- Bag Size and Strength: FFS woven bags typically hold between 20 to 50 kg of product, but the size and strength needed will depend on the weight and density of the material being packed. For example, bags designed for cement must have high tensile strength to avoid breaking under the weight of the load.
- Seal Integrity: One of the most important features of FFS woven bags is their ability to remain sealed during transport and storage. Heat or ultrasonic sealing methods are used to bond the fabric, ensuring that the bags stay closed and prevent leakage.
- Ventilation: For some applications, such as fertilizers, the bags need to be ventilated to prevent condensation inside. Ventilated FFS woven bags allow air to flow through the material, preventing moisture buildup.
Product Parameter Comparison Table
Parameter | Cement & Construction | Agricultural Products | Chemicals & Powders |
---|---|---|---|
Material | Woven PP + PE Liner | Woven PP + PE Liner | Woven PP + Laminated Film |
Tensile Strength (kg) | 350-400 | 250-300 | 300-350 |
Moisture Resistance | High | Medium | High |
UV Resistance | Medium to High | Low to Medium | High |
Leak Resistance | Excellent | Medium | Excellent |
Customization Options | High | Medium | High |
Standard Compliance | EN 15593, ASTM F88 | JIS Z 0238, AS 4130 | EN 15593, ASTM F88 |
FAQs
Q1: Why is moisture resistance important in FFS woven bags? Moisture resistance is crucial for products like cement and gypsum, which can harden or degrade when exposed to water. A moisture-resistant bag ensures these materials stay in good condition and remain usable.
Q2: What happens if the seal of a FFS woven bag breaks? If the seal breaks, powders like cement or gypsum can leak out, leading to product loss and contamination. A strong seal ensures that the bag remains intact throughout transport and storage.
Q3: Can FFS woven bags be customized? Yes, FFS woven bags can be customized with printed logos, designs, and text, offering a branding opportunity for businesses. Customization also helps differentiate products in the marketplace.
Q4: Are FFS woven bags eco-friendly? Many FFS woven bags are made from recyclable materials, such as polypropylene, which makes them an eco-friendly option for businesses looking to reduce their environmental footprint.
Conclusion
FFS woven bags are a reliable and cost-effective solution for packaging a variety of materials. Their strength, moisture resistance, and leak-proof design make them ideal for industries like construction, agriculture, and chemicals. By understanding the key design considerations and selecting the right bags based on global standards, businesses can ensure that their products are safely packaged and ready for transport. As the demand for sustainable packaging grows, FFS woven bags continue to offer an eco-friendly, efficient solution for bulk material packaging.
For more information on advanced packaging solutions, explore Industrial Woven Packaging Bags: Aligning with Policies and ESG Standards and Laminated Woven Bags: Advanced Manufacturing and the Path to Brand Excellence in the Chinese Market.