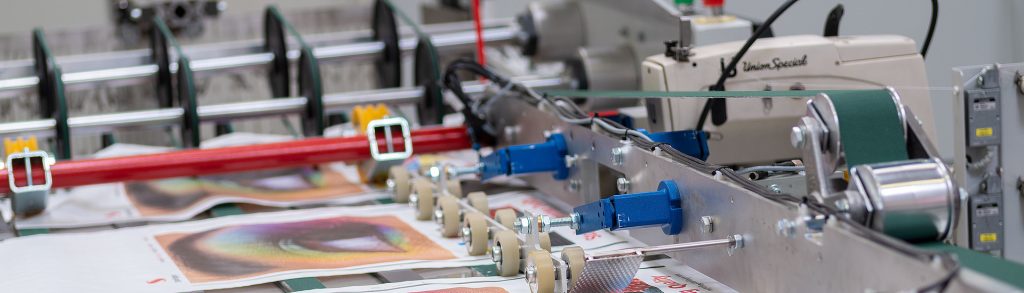
“Why are HDPE fabric bags becoming the go-to solution for livestock feed storage and transport?” asked Ray, CEO of VidePak, during a recent industry roundtable. The answer lies in their unmatched durability, moisture resistance, and adaptability to advanced sealing technologies—critical for preserving feed quality while meeting global sustainability goals. This report dissects how VidePak’s HDPE (High-Density Polyethylene) fabric bags leverage cutting-edge manufacturing processes and strategic design choices to dominate this niche market.
H2: Manufacturing Processes: Balancing Strength and Efficiency
H3: Sewing Techniques and Thread Selection
HDPE fabric bags require robust stitching to withstand rough handling and heavy loads (up to 50 kg). VidePak employs dual-needle lockstitch machines with polyester or nylon threads, selected based on application:
- Polyester Threads: Ideal for UV resistance (critical for outdoor storage), with tensile strength ≥80 N/cm² .
- Nylon Threads: Superior abrasion resistance, reducing seam failure by 30% in high-friction environments like feed mills .
Stitch Density Optimization:
Application | Stitches per Inch (SPI) | Thread Diameter (mm) |
---|---|---|
General Feed Bags | 6–8 | 0.45–0.55 |
Heavy-Duty Sacks | 8–10 | 0.60–0.70 |
Exceeding 10 SPI risks perforating the HDPE fabric, while fewer than 6 SPI compromises seam strength . |
H3: Ultrasonic Welding vs. Heat Sealing
For moisture-sensitive feeds like poultry pellets, VidePak uses ultrasonic welding—a needle-free method that fuses HDPE layers at molecular levels. Key advantages include:
- Leakproof Seals: Achieves 0.02% moisture permeability, outperforming stitched seams by 50% .
- Speed: 20-meter/minute production rate, 4× faster than traditional sewing .
In contrast, heat sealing suits lightweight feeds (e.g., alfalfa) with lower tensile demands. VidePak’s Starlinger extrusion lines produce 0.08–0.12 mm HDPE films, melted at 160–180°C for uniform seals .
H2: Bag Mouth Design: Functionality Meets Practicality
H3: Open Mouth vs. Valve Mouth
- Open Mouth Bags: Feature rolled or hemmed edges for manual filling. Ideal for small farms, they allow visual inspection but require additional closure (e.g., stitching or adhesive tapes) .
- Valve Mouth Bags: Integrate a tubular spout for automated filling, reducing spillage by 25%. VidePak’s valve designs comply with ISO 22477 standards, supporting flow rates up to 1 ton/minute .
Case Study: A Brazilian feed mill reduced labor costs by 40% after switching to VidePak’s valve-mouth bags with RFID tracking tags.
H3: Heat-Sealed vs. Stitched Closures
Parameter | Heat-Sealed | Stitched |
---|---|---|
Moisture Resistance | Excellent (0.01% ingress) | Moderate (0.05% ingress) |
Cost Efficiency | $0.03/bag | $0.05/bag |
Reusability | 1–2 cycles | 5+ cycles |
Heat sealing dominates for single-use applications, while stitching suits reusable bulk transport . |
H2: VidePak’s Competitive Edge
H3: Technology-Driven Production
With 100+ Starlinger circular looms and 30 ultrasonic welders, VidePak achieves:
- Precision: ±0.1 mm seam alignment tolerance, critical for valve mouth integrity.
- Scalability: 50,000 bags/day capacity, with 14-day lead times for custom orders.
H3: Sustainability Compliance
- Recycled HDPE: 30% post-consumer content, meeting EU’s Circular Economy Package (2030).
- Solar-Powered Facilities: 2 MW rooftop panels reduce CO₂ emissions by 1,200 tons/year.
FAQs:
Q: How do I choose between stitched and welded bags?
A: Welding excels for moisture-sensitive feeds; stitching suits reusable/heavy-duty applications.
Q: Can HDPE bags withstand freezing temperatures?
A: Yes, VidePak’s cold-grade HDPE retains flexibility at -30°C (tested per ASTM D746).
H2: Market Trends and Strategic Insights
H3: Smart Packaging Integration
VidePak’s NFC-enabled bags track feed expiration dates and storage conditions, reducing spoilage by 18% in Vietnamese trials .
H3: Regulatory Alignment
Anticipating stricter FDA feed safety guidelines (2026), VidePak preemptively adopted food-grade HDPE resins with ≤50 ppm heavy metal migration .
“In livestock feed packaging, every seam and stitch impacts profitability,” emphasized Ray. By merging engineering rigor with sustainability, VidePak is redefining industry standards—one bag at a time.
For deeper insights, explore our resources on advanced HDPE welding techniques and sustainable bulk packaging solutions.
Appendix: Technical Specifications
Parameter | HDPE Fabric Bags | Industry Average |
---|---|---|
Tensile Strength | 120 N/cm² | 90 N/cm² |
UV Resistance | 2,000 hours (ASTM G154) | 1,500 hours |
Moisture Permeability | 0.02 g/m²/day (DIN 53122) | 0.05 g/m²/day |
FAQs
Q: How does stitch density affect bag lifespan?
A: 8–10 SPI optimizes strength without fabric damage, extending reuse cycles to 5+ .
Q: Are valve mouths compatible with organic feed?
A: Yes, VidePak’s FDA-compliant valves prevent contamination during automated filling.