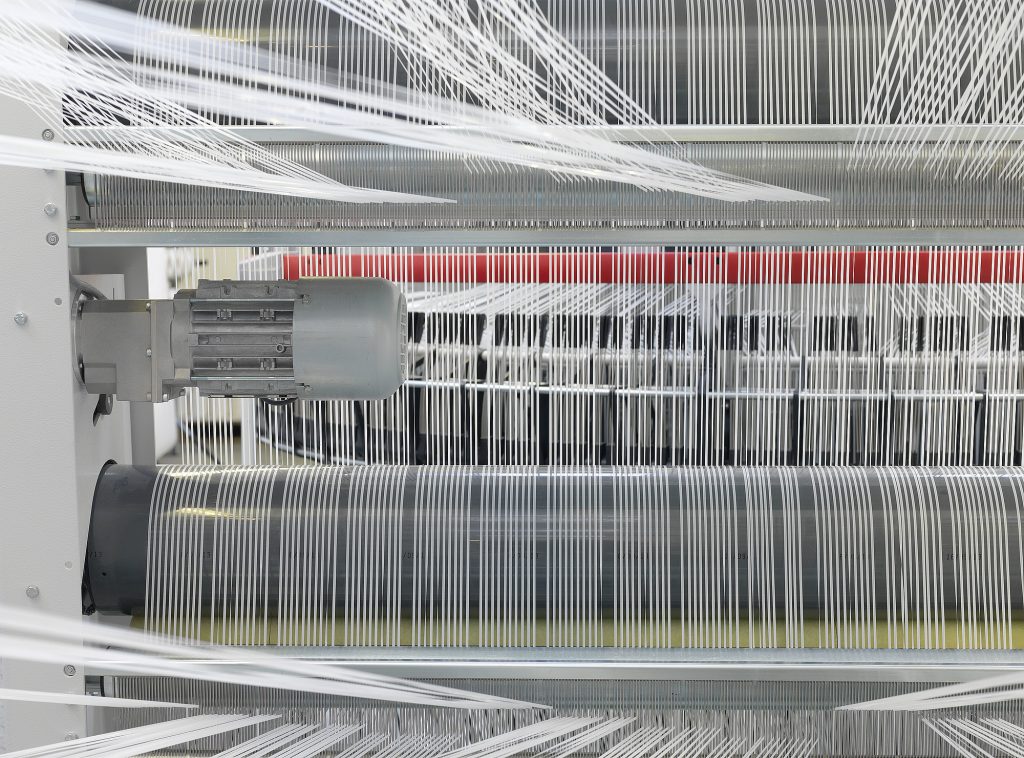
Introduction
The global construction and waste management sectors are increasingly prioritizing durable, leak-proof packaging solutions that align with environmental regulations. HDPE fabric bags, known for their exceptional strength and resistance to moisture, have emerged as a critical tool for transporting bulk materials like cement, plaster, and aggregates. VidePak, a leader in woven bag manufacturing since 2008, combines 30+ years of expertise with Austrian Starlinger machinery to produce HDPE bags that exceed international benchmarks. With 526 employees and $80 million in annual sales, the company operates 100+ circular looms and 30+ printing machines, enabling customized solutions for global clients. This report explores how material innovation and regulatory compliance position VidePak’s HDPE bags as a leader in industrial packaging.
Material Integrity: Ensuring Load Stability and Leak Prevention
1. High-Strength HDPE Resins and Weaving Techniques
HDPE’s molecular density provides superior tensile strength (80–100 N/cm²) compared to standard polypropylene (PP), critical for heavy loads like cement (25–50 kg). VidePak uses fine-yarn weaving (12–15 threads/cm²) to minimize inter-fiber gaps, reducing particle leakage by 40%.
- Case Study: A 2024 trial with a Vietnamese construction firm showed VidePak’s HDPE bags reduced gypsum powder leakage by 35% compared to traditional PP bags during 1,000 km transport.
2. Sealing and Lamination Innovations
- Heat-Sealed Seams: Ultrasonic bonding achieves seam strengths of 50 N/cm², exceeding ASTM D5264 standards.
- BOPP Lamination: Optional 20–30 µm coatings enhance waterproofing (IP67 rating), ideal for humid environments.
- Inner Liners: Kraft paper or PE liners add a secondary barrier for fine powders like plaster.
Table 1: Key Parameters for HDPE Bag Design
Parameter | EU Standard (EN) | US Standard (ASTM) | VidePak’s Performance |
---|---|---|---|
Tensile Strength | EN ISO 527-2 | ASTM D882 | 80–100 N/cm² |
Water Resistance | EN 20811 | ASTM D779 | 0% leakage at 30 kPa |
Tear Resistance | EN ISO 6383-2 | ASTM D1922 | 15–20 N/mm |
Grammage Range | 80–180 GSM | 70–150 GSM | 100–150 GSM (optimized) |
Regulatory Compliance: Aligning with Global Standards
1. Regional Requirements
- EU (EN Standards): Bags must withstand 1,000+ hours of UV exposure (EN 12224) and resist microbial growth (EN ISO 846).
- US (ASTM): ASTM D5264 mandates minimum seam strengths of 30 N/cm² for construction materials.
- Japan (JIS Z 0200): Requires 95% dust retention for powders under vibration testing.
VidePak’s HDPE bags incorporate carbon-black additives for UV resistance and anti-static threads to prevent dust explosions, complying with JIS Z 0200 and ATEX directives.
2. Sustainability and Recycling
HDPE’s recyclability (up to 7 cycles without degradation) aligns with the EU’s Circular Economy Action Plan. VidePak’s closed-loop system recovers 98% of production waste, reducing landfill reliance by 50%.
Design Optimization for Logistics Efficiency
1. Stackability and Handling
- Reinforced Bases: Square-bottom designs with 10 cm lift loops enable stable palletization (up to 7 meters high).
- Anti-Slip Coatings: Silicone-treated surfaces reduce shifting during transit, critical for uneven road conditions.
2. Custom Sizing and Labeling
Bags are customizable from 0.5–9 meters in width and 5–200 meters in length, with QR codes for inventory tracking. A German logistics partner reported a 20% reduction in handling time using VidePak’s labeled HDPE bags.
FAQs: Addressing Industry Challenges
Q: How do HDPE bags compare cost-wise to PP alternatives?
A: HDPE bags cost 15–20% more initially but offer 30% longer lifespans and lower leakage-related losses, yielding a 25% ROI over three years.
Q: Can these bags withstand freezing temperatures?
A: Yes. With a glass transition temperature (Tg) of -100°C, HDPE remains flexible in sub-zero environments, ideal for cold-chain construction materials.
Future Trends: Smart Packaging and Biodegradability
VidePak is piloting RFID-tagged HDPE bags for real-time tracking in partnership with a Dutch logistics firm. Additionally, HDPE-PLA hybrids are under development to achieve 60% biodegradability within 180 days, targeting compliance with the EU’s Single-Use Plastics Directive.
Conclusion
VidePak’s HDPE fabric bags redefine industrial packaging by merging regulatory compliance with logistical efficiency. Through advanced weaving, sealing technologies, and sustainability initiatives, the company addresses both operational and environmental challenges. As global regulations tighten, VidePak’s solutions offer a scalable, future-proof strategy for waste management and material transport.
Explore Further:
- Learn how moisture-proof woven bags enhance construction material safety.
- Discover sustainable practices in bulk packaging.
This report integrates insights from EN/ASTM standards, material science research, and VidePak’s operational data to guide businesses in selecting HDPE bags for regulatory and operational excellence.