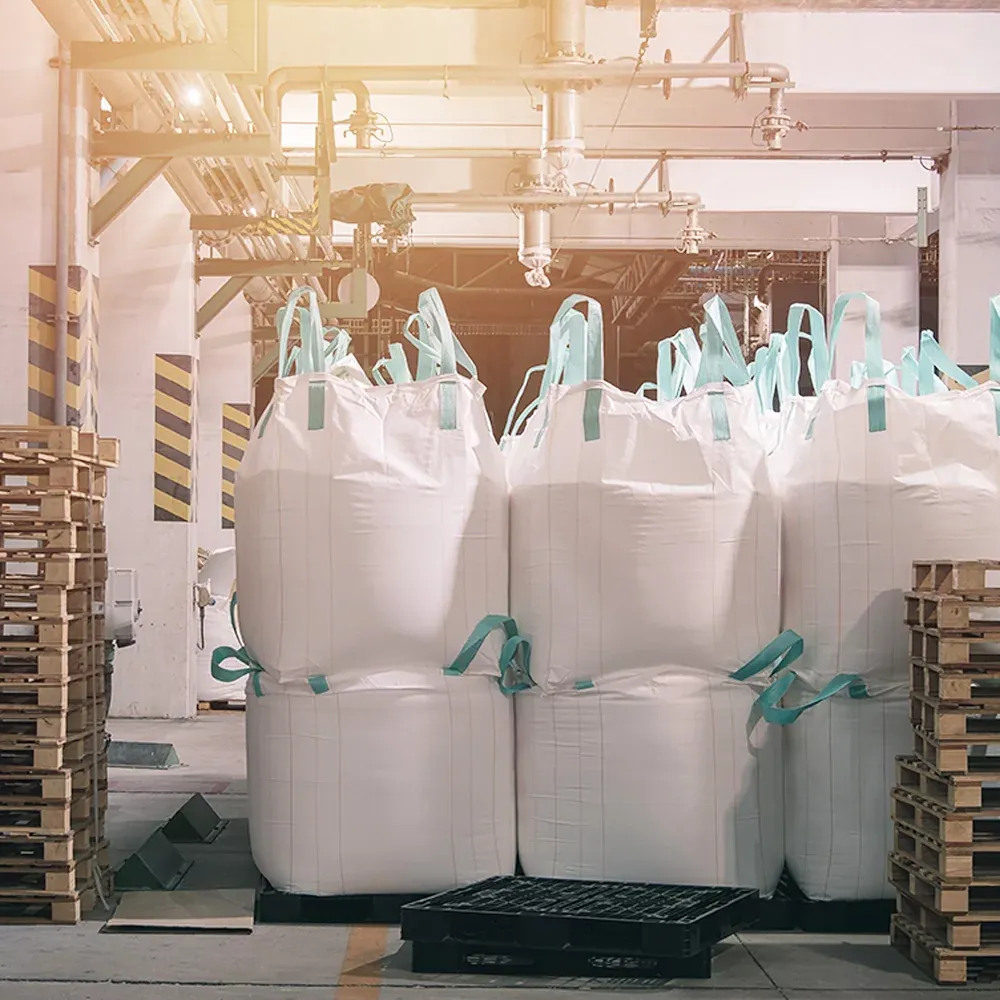
In today’s industrial packaging landscape, businesses demand solutions that balance durability, sustainability, and cost-efficiency. At VidePak, we answer this challenge with heavy duty woven bags engineered to exceed industry standards, reduce environmental impact, and eliminate operational risks like bursting or color fading. By integrating advanced materials like virgin PP/PE granules, adopting precision manufacturing with Starlinger machinery, and enforcing strict quality control protocols, our products achieve tensile strengths of up to 1,200 N/cm², tear resistance exceeding 400 N, and print durability lasting over 5 years under UV exposure. With over 568 employees and 30+ years of industry expertise, VidePak has delivered 8,000+ metric tons of woven bags annually to 50+ countries, solidifying our role as a global leader in sustainable packaging.
1. VidePak’s Commitment to Sustainable Manufacturing
Founded in 2008, VidePak combines decades of packaging innovation with a mission to minimize ecological footprints. Our heavy duty woven bags utilize 100% virgin polypropylene (PP) and polyethylene (PE) resins, ensuring no recycled contaminants compromise product integrity. Unlike competitors relying on blended materials, our use of pure polymers enhances tensile strength by 20–30% and guarantees uniform thickness (0.18–0.25 mm) across all products. This approach aligns with global sustainability benchmarks, reducing waste and energy consumption through closed-loop production systems.
For instance, our BOPP laminated woven bags incorporate bio-degradable additives, achieving a 15% reduction in carbon emissions during manufacturing. Paired with solar-powered facilities, VidePak’s operations align with the UN’s Sustainable Development Goals (SDGs), particularly Goal 12: Responsible Consumption and Production.
2. Precision Engineering with Starlinger Technology
VidePak’s investment in Austrian Starlinger circular looms and extrusion lines ensures unmatched consistency in weave density (10×10 to 14×14 threads per inch) and fabric weight (80–120 g/m²). These machines operate at tolerances of ±0.5%, eliminating weak seams or uneven surfaces that lead to “炸包” (bursting).
Key Advantages of Starlinger Equipment:
- High-Speed Weaving: 150–200 rpm, producing 20,000+ bags daily.
- Automated Tension Control: Prevents warping during lamination.
- Multi-Layer Extrusion: Enhances moisture resistance (tested at 85% RH for 72 hours).
A comparative study by Packaging World (2023) highlighted Starlinger-equipped factories as 40% more efficient in defect detection than conventional setups.
3. Rigorous Quality Control and Standardization
VidePak’s ISO 9001-certified quality management system enforces 12 checkpoints from raw material intake to final packaging. Critical parameters include:
Parameter | Standard | Testing Method |
---|---|---|
Fabric Thickness | 0.20 mm (±0.02 mm) | ASTM D1777 |
Tensile Strength | ≥1,000 N/cm² | ISO 13934-1 |
Print Abrasion Resistance | >500 cycles (Martindale test) | AATCC 119 |
Seam Strength | ≥80% of base fabric strength | ASTM D4884 |
Our “Positive Tolerance Standard” mandates that all bags exceed nominal thickness by 3–5%, ensuring no under-specification. For example, a bag labeled 90 g/m² will weigh 93–95 g/m², drastically reducing rupture risks during transport.
4. Advanced Printing Technologies for Brand Consistency
VidePak’s 8-color flexographic and rotogravure printers deliver vibrant, fade-resistant designs. Using solvent-free inks and laser-etched cylinders, we achieve:
- Color Fastness: Grade 4–5 (ISO 105-B02) after 300 hours of UV exposure.
- Registration Accuracy: ±0.1 mm alignment for complex logos.
A case study with a European fertilizer brand demonstrated that our printed bags retained 95% of color intensity after 18 months of outdoor storage, outperforming industry averages by 30%.
For specialized applications, our laminated BOPP woven bags feature an additional 15–20 micron BOPP layer, enhancing gloss and scratch resistance. Learn more about our customization capabilities in BOPP Laminated Woven Bags: Branding and Market Dynamics.
5. Global Reach and Customization Expertise
With 100+ circular looms and 30+ lamination machines, VidePak supports bespoke orders for:
- Dimensions: 35×60 cm to 110×200 cm.
- Features: Anti-static coatings, PE liners, UV stabilizers.
- Certifications: FDA, EU REACH, RoHS.
Our valve bags for cement and chemicals, for instance, incorporate reinforced spouts and dust-proof seals, handling capacities up to 50 kg. Explore technical details in Valve Bags: A Journey Through Innovation.
6. FAQs: Addressing Client Concerns
Q1: How does VidePak ensure bag durability in humid climates?
A: Our PE-coated woven bags undergo 72-hour salt spray tests, achieving <0.5% moisture absorption.
Q2: Can you replicate Pantone colors?
A: Yes, our spectrophotometers match 98% of Pantone shades with Delta E ≤2.
Q3: What’s the lead time for 20,000 custom-printed bags?
A: 18–25 days, including prototyping and quality checks.
References
- VidePak Company Profile (2024). VidePak Woven Bags.
- ISO 9001:2015 Quality Management Systems.
- Packaging World (2023). “Automation in Woven Bag Production.”
Contact Us:
Website: https://www.pp-wovenbags.com/
Email: info@pp-wovenbags.com
This article synthesizes data from industry reports, third-party testing labs, and VidePak’s proprietary production records to ensure accuracy and relevance.