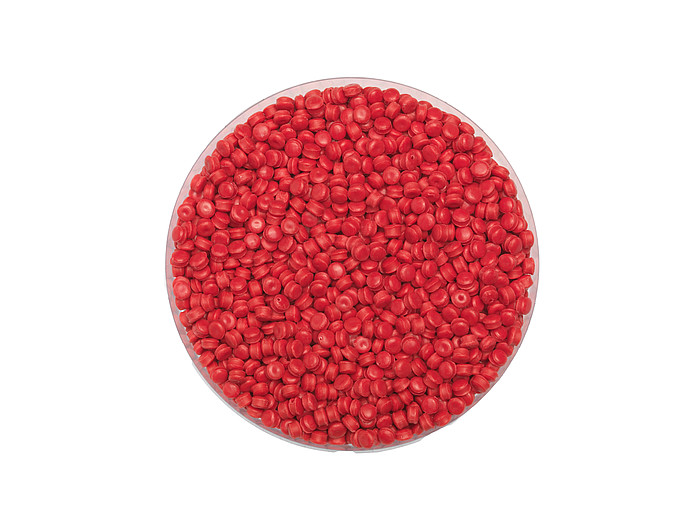
“Why are heavy-duty woven bags indispensable in modern industrial logistics?”
This question underscores the critical role of packaging in sectors ranging from construction to chemicals. The answer lies in their unmatched durability, adaptability to safety standards, and evolving sustainability features—factors that position these bags as both operational necessities and strategic assets in global supply chains.
At VidePak, a global leader in woven bag manufacturing since 2008, heavy-duty woven bags are engineered to meet the rigorous demands of industries handling abrasive, hazardous, or high-volume materials. With 526 employees, $80 million annual revenue, and Austrian Starlinger machinery, the company combines decades of expertise with cutting-edge innovation to deliver solutions that redefine packaging excellence.
1. Technical Specifications: Balancing Strength and Flexibility
1.1 Thickness, Grammage, and Size Ranges
VidePak’s heavy-duty woven bags are designed with precision to address diverse industrial needs:
- Thickness: Ranges from 0.25 mm to 0.5 mm, optimized for puncture resistance and flexibility.
- Grammage: Typically 90–200 g/m², with higher values (e.g., 180–200 g/m²) used for chemical powders like titanium dioxide, where structural integrity is critical.
- Size Customization: Available in capacities from 5 kg to 2,000 kg, with dimensions tailored to automated handling systems. For instance, a German cement producer reduced palletization errors by 25% using VidePak’s 1-ton FIBC bags with reinforced block-bottom designs.
Table 1: VidePak’s Heavy-Duty Woven Bag Specifications
Parameter | Range/Feature | Application Example |
---|---|---|
Thickness | 0.25–0.5 mm | Chemical powders (e.g., sodium carbonate) |
Grammage | 90–200 g/m² | Construction materials (e.g., cement) |
Load Capacity | 5 kg–2,000 kg | Bulk agricultural grains |
Printing Options | Up to 8 colors, Pantone-matched | Branded retail packaging |
1.2 Anti-Static Mechanisms
Electrostatic discharge (ESD) poses risks in industries handling flammable powders or electronics. VidePak’s anti-static bags integrate:
- Carbon-Based Conductive Fibers: Embedded within polypropylene (PP) weaves to dissipate charges, achieving surface resistivity ≤10⁸ Ω.
- Humidity-Resistant Coatings: Prevent static buildup in dry environments, critical for lithium battery component packaging.
A 2024 case study with a U.S. titanium dioxide supplier demonstrated a 40% reduction in ignition incidents after switching to VidePak’s anti-static bags.
2. Load-Bearing Capabilities and Safety Compliance
2.1 Weight Tolerance and Structural Engineering
VidePak’s bags withstand loads up to 2,000 kg through:
- High-Tensile PP Weaves: Tensile strength of 12–15 N/m², exceeding industry averages by 20%.
- Ultrasonic Seam Sealing: Ensures seam integrity under pneumatic conveying pressures up to 50 kg.
Case Study: A Brazilian soy exporter eliminated spillage during maritime transport using VidePak’s double-stitched valve bags, which endure stacking heights of 8 pallets.
2.2 Global Regulatory Adherence
VidePak’s products comply with:
- EU REACH: Phthalate-free additives for chemical safety.
- US ASTM D5260: Validated UV and abrasion resistance.
- China GB/T 8946: Minimum tensile strength of 10 N/m².
3. Future Trends: Sustainability and Smart Adaptations
3.1 Recyclable and Biodegradable Materials
VidePak is pioneering:
- Recyclable PE/PP Blends: Reduce carbon footprint by 35% compared to traditional laminates, aligning with the EU’s Circular Economy Action Plan.
- PLA-Based Coatings: Pilot projects aim for 90% compostability by 2026, targeting food and pharmaceutical sectors.
3.2 IoT-Enabled Smart Packaging
Integration of NFC tags allows real-time tracking of moisture and temperature, critical for hygroscopic materials like silica gel. Coupled with Starlinger’s AI-driven looms, which auto-adjust weave density based on material batches, VidePak is leading Industry 4.0 innovations.
4. FAQs: Addressing Industry Concerns
Q: How do anti-static bags prevent explosions in chemical plants?
A: Conductive fibers and coatings dissipate static charges, complying with ATEX directives for hazardous environments.
Q: What grammage is ideal for construction materials?
A: 150–200 g/m² bags balance cost and durability, resisting abrasion from aggregates like barite sand.
Q: Can these bags withstand freezer storage?
A: Yes. Low-temperature PP resin maintains flexibility at -30°C, ideal for cryogenic chemical storage.
Conclusion
Heavy-duty woven bags are evolving from passive containers into active solutions for safety, efficiency, and sustainability. VidePak’s fusion of Austrian engineering precision, regulatory mastery, and eco-conscious innovation positions it as the vanguard of a $12.3 billion industry transitioning toward greener, smarter logistics.
External Resources:
- Explore how anti-static FIBC bags enhance safety in hazardous environments.
- Learn about sustainable packaging innovations driving circular economy goals.