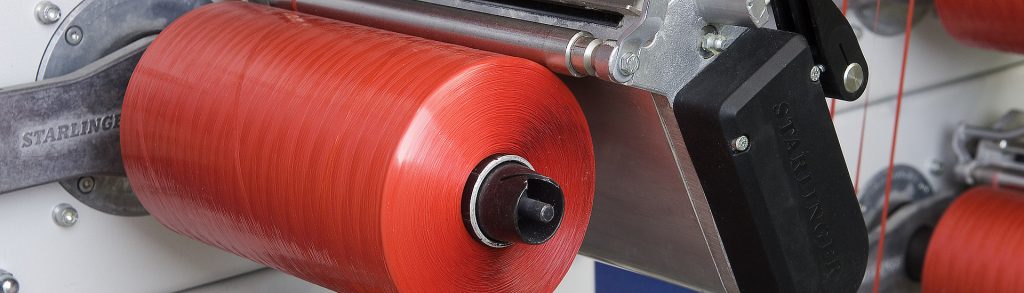
Introduction
Heavy-duty woven polypropylene (PP) bags have become indispensable for livestock feed packaging. With their exceptional strength, durability, and versatility, these bags ensure safe transport and storage while protecting feed from environmental factors. VidePak leverages state-of-the-art equipment from global leaders Starlinger (Austria) and W&H (Germany) to produce woven bags that meet the rigorous requirements of the livestock feed industry.
Key Stages of Production and Quality Control
The production of heavy-duty woven bags involves several critical stages, each with precise quality controls to ensure consistency and performance.
1. Extrusion
In this stage, polypropylene granules are melted and extruded into fine filaments.
- Technology and Quality Control: Starlinger extruders ensure accurate temperature regulation, resulting in uniform filaments with optimal tensile strength. The use of virgin polypropylene ensures purity, which directly enhances the bag’s durability and resistance to wear.
2. Filament Drawing
The extruded filaments are stretched to align the polymer chains, enhancing their strength.
- Process Details: Precise draw ratios are maintained to maximize the tensile properties without over-stretching.
- Quality Impact: Filaments with aligned chains exhibit higher load-bearing capacity, crucial for heavy-duty applications like livestock feed packaging.
3. Weaving
The drawn filaments are woven into durable fabric using automated circular looms.
- Technology Advantage: W&H looms produce tightly woven fabric with consistent density, reducing the likelihood of tears.
- Performance: The woven structure provides a high strength-to-weight ratio, making the bags ideal for carrying up to 50 kg.
4. Lamination
A polyethylene layer is applied to the woven fabric to enhance its moisture resistance and structural integrity.
- Innovation: Starlinger’s lamination systems ensure uniform application, minimizing weak spots.
- Outcome: This layer prevents moisture penetration, keeping livestock feed dry and extending its shelf life.
5. Printing
Graphics and labeling are applied using advanced flexographic printing.
- Technology Highlight: High-resolution W&H printing machines enable vibrant, multi-color prints that enhance brand visibility.
- Benefit: Clear, detailed labels improve product identification, meeting regulatory requirements for feed packaging.
6. Bag Formation
The laminated fabric is cut, stitched, or heat-sealed into the final bag shape.
- Precision Techniques: Ultrasonic sealing ensures strong closures without compromising bag flexibility.
- Quality Monitoring: Automated inspection systems check for consistent seam strength and dimensional accuracy.
Advantages of Heavy Duty Woven Bags in Livestock Feed Packaging
Feature | Benefits |
---|---|
Exceptional Strength | Handles up to 50 kg, reducing the need for additional packaging. |
Moisture Resistance | Lamination and optional inner liners protect feed from humidity. |
Tear Resistance | Durable woven structure withstands handling and transport stresses. |
Customizability | Available in various sizes and colors, with customizable printing. |
Breathability | Optional vented designs prevent mold growth, maintaining feed quality. |
Detailed Analysis of Feed Packaging Applications
Heavy-duty woven bags are ideal for packaging various types of livestock feed, including poultry, cattle, and pig feed. Their application is driven by specific performance attributes:
- Cost Efficiency:
Woven PP bags are highly cost-effective due to their recyclability and lower production costs compared to alternatives like paper or plastic. - Strength and Durability:
The tightly woven fabric resists tears and punctures, ensuring feed safety during transport and storage. - Moisture Protection:
Laminated surfaces and optional inner liners shield feed from humidity, a critical factor for preserving feed nutrients and preventing spoilage. - Hygienic and Anti-Mold Properties:
The breathable structure of vented bags minimizes condensation, reducing the risk of mold and bacterial growth.
Selecting the Right Bag Specifications
Parameter | Recommendation |
---|---|
Fabric Weight | 100–120 GSM for maximum durability. |
Bag Size | Standard sizes of 25 kg and 50 kg; customizable for specific needs. |
Inner Liners | Recommended for high-humidity regions. |
Lamination | Essential for outdoor storage and enhanced water resistance. |
Printing Options | Multi-color printing for branding and regulatory compliance. |
Industry Trends and Innovations
- Sustainability Focus:
VidePak’s woven bags are made from 100% recyclable materials, aligning with global sustainability goals. - Automated Quality Control:
Our Starlinger and W&H equipment enables real-time monitoring, reducing defects and improving production efficiency. - Custom Solutions for Branding:
With advanced printing capabilities, VidePak helps customers enhance their brand visibility through high-quality, customizable designs.
FAQs
1. What makes heavy-duty woven bags ideal for livestock feed packaging?
Their high tensile strength, moisture resistance, and customizability make them perfect for securely storing and transporting feed.
2. Are the bags environmentally friendly?
Yes, VidePak’s woven bags are 100% recyclable, contributing to reduced environmental impact.
3. How does VidePak ensure quality consistency?
We use advanced equipment from Starlinger and W&H to control every stage of production, from extrusion to bag formation.
Case Study: Livestock Feed Packaging Optimization
A major feed supplier partnered with VidePak to replace traditional packaging with heavy-duty woven bags. The results included:
- 30% reduction in packaging costs due to the durability and reusability of woven bags.
- Increased feed shelf life in humid regions, attributed to superior moisture resistance.
- Enhanced brand recognition through high-quality custom printing.
Conclusion
VidePak’s commitment to quality and innovation ensures our heavy-duty woven bags are the ideal solution for livestock feed packaging. By combining advanced manufacturing techniques with cutting-edge equipment from Starlinger and W&H, we deliver reliable, customizable, and cost-effective packaging solutions.
Learn more about heavy-duty woven bag solutions or explore our innovative manufacturing processes to understand why VidePak is a trusted industry leader.