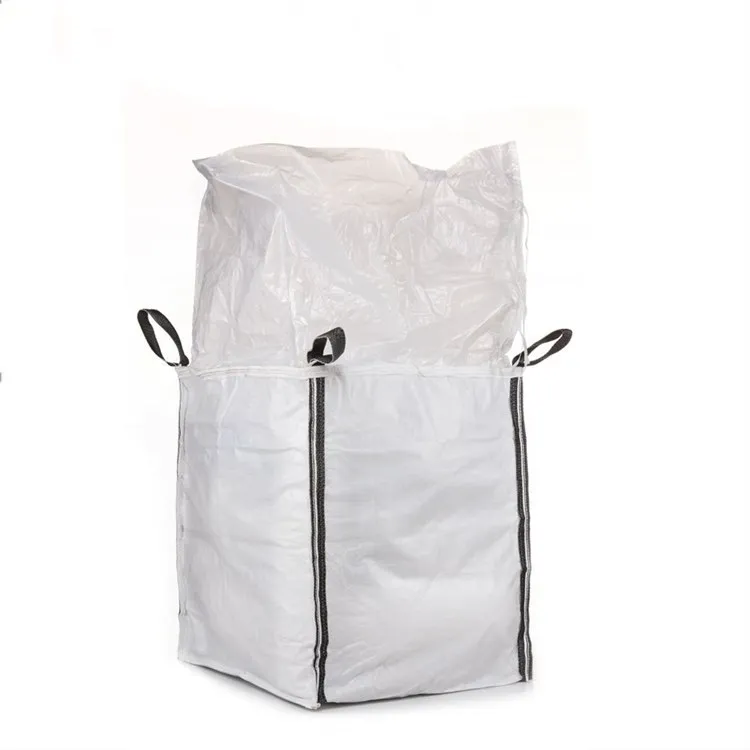
In industries where heavy-duty bulk handling is essential, Heavy Duty Woven Bags provide an optimal solution for the packaging, storage, and transport of various chemical powders. From titanium dioxide and calcium titanate to silica, latex, sodium carbonate, and zinc sulfate, the storage of these materials in woven bags ensures stability, safety, and efficient handling. Designed to withstand loads ranging from 500 kg (1,100 lbs) to 2,000 kg (4,400 lbs), these bags are increasingly popular in sectors requiring robust, leak-proof packaging solutions. To learn more about how Heavy Duty Woven Bags provide advanced, leak-proof packaging, see this comprehensive article here.
Understanding Heavy-Duty Woven Bags
Ton Woven Bags, Jumbo Bags, Bulk Bags, and FIBC Bags are all large-scale woven bags designed to handle substantial weights, making them ideal for handling high-volume chemical powders. The bags’ construction involves a combination of materials like polypropylene (PP) and polyethylene (PE), renowned for their strength, flexibility, and resilience. These materials are crafted using techniques that allow the bags to safely contain powdered contents, prevent contamination, and reduce the risk of leakage during transportation and storage.
Below is a table outlining some essential properties and specifications of heavy-duty woven bags used in chemical industries:
Property | Description | Value/Feature |
---|---|---|
Material | High-strength polypropylene and polyethylene | Durable, flexible, recyclable |
Load capacity | Supports between 500 kg to 2,000 kg | 1,100 lbs to 4,400 lbs |
Lamination options | Optional inner and outer layers | Enhanced strength and waterproofing |
Closure methods | Heat sealing, ultrasonic sealing, and sewn seams | Provides secure containment |
Structural design | Circular/tubular, square-bottom, gusseted | Improves stacking, reduces storage space |
Anti-static properties | Additive treatments to prevent static buildup | Enhanced safety in handling powders |
UV resistance | UV-stabilized materials | Withstands outdoor storage conditions |
Certifications | Compliance with international quality standards | ISO, UN certification available |
Preventing Leakage in Heavy Duty Woven Bags
For industries handling fine powders, even minimal leakage can lead to product loss, contamination, and safety hazards. Therefore, advanced techniques are employed to enhance the woven bags’ durability and minimize any chance of leakage. Some primary methods for leak prevention include:
1. Outer Layer Lamination
Lamination, usually done with a layer of polyethylene, adds an outer seal to the bag. This seal improves water resistance and helps to contain fine particles that could otherwise escape through the woven fabric. The lamination can be customized to various thicknesses, depending on the requirements, which also protects against moisture and environmental factors that might otherwise degrade the quality of the contents.
2. Inner Bag Liners
Incorporating a secondary liner inside the Heavy Duty Woven Bags adds a layer of protection against leakage. These liners, made from materials like PE or multi-layer co-extruded films, are designed to fit snugly within the woven bag, creating a barrier against powder particles. Liners are essential for powders like calcium titanate and latex powders, which are particularly fine and prone to leakage without added containment.
3. High-Density Weaving
The weaving process itself plays a vital role in creating bags that are highly durable. Advanced weaving techniques enable tighter weaving patterns, which are essential in holding fine powders without allowing them to escape through the fabric. Increasing the weave density enhances the bag’s structural integrity, making it robust enough to hold large quantities while preventing dust or powder particles from leaking.
4. Ultrasonic and Heat Sealing
Closure techniques, such as ultrasonic sealing or heat sealing, are crucial in ensuring that the contents remain securely contained within the bag. Traditional stitching may sometimes create tiny gaps that allow for fine particles to escape; however, ultrasonic or heat-sealed seams provide a smooth, continuous bond that effectively seals any possible openings. These methods are particularly valuable for bags intended for high-purity chemical powders where leak-proof storage is critical.
Specialized Features of Woven Bags for Chemical Powders
Given the requirements of chemical powder packaging, certain custom features are often integrated to enhance bag functionality and safety:
- Anti-static Properties: Many chemical powders, particularly those prone to static charges, can create unsafe handling conditions. Anti-static properties added to Jumbo Bags or Bulk Bags reduce the risks associated with static buildup, which is especially important when handling fine, flammable powders.
- UV Resistance: For chemicals requiring outdoor storage, UV-resistant properties in woven bags ensure that they can withstand prolonged sun exposure without degrading. This durability helps to maintain the integrity of the stored powders over time.
- Valve and Closure Options: Valves provide a controlled method for filling and emptying bags, while effective closure options, such as Velcro or zipper-style closures, ensure minimal exposure to external contaminants.
Applications in Chemical Packaging
Heavy-duty woven bags with these specialized features have transformed chemical packaging, particularly for industries involved with powders requiring strict containment. Some of the common chemical powders packed in these bags include:
- Titanium Dioxide (TiO₂): Used extensively in paints, coatings, and plastics, titanium dioxide requires protection against both moisture and static.
- Calcium Titanate: A fine powder often used in the manufacturing of ceramics, this material benefits from woven bags with anti-static properties.
- Silica Powder: Common in electronics and glass production, silica powder packaging must be secure to prevent contamination.
- Latex Powder: This powder, used in adhesives and other industrial applications, is moisture-sensitive, making inner liners and sealing methods critical.
Environmental Considerations
VidePak places a strong emphasis on sustainability. Heavy Duty Woven Bags, Ton Woven Bags, and Jumbo Bags produced by VidePak are made from 100% recyclable polypropylene, minimizing environmental impact without compromising quality. Additionally, woven bags offer a lower carbon footprint compared to other bulk storage options, as they are reusable and require less energy to produce and recycle.
Conclusion
The advancements in woven bag technology have made them an invaluable asset for handling, storing, and transporting chemical powders. By employing techniques such as outer lamination, inner liners, dense weaving, and ultrasonic sealing, these bags provide a reliable and leak-proof packaging solution for high-volume chemical materials.