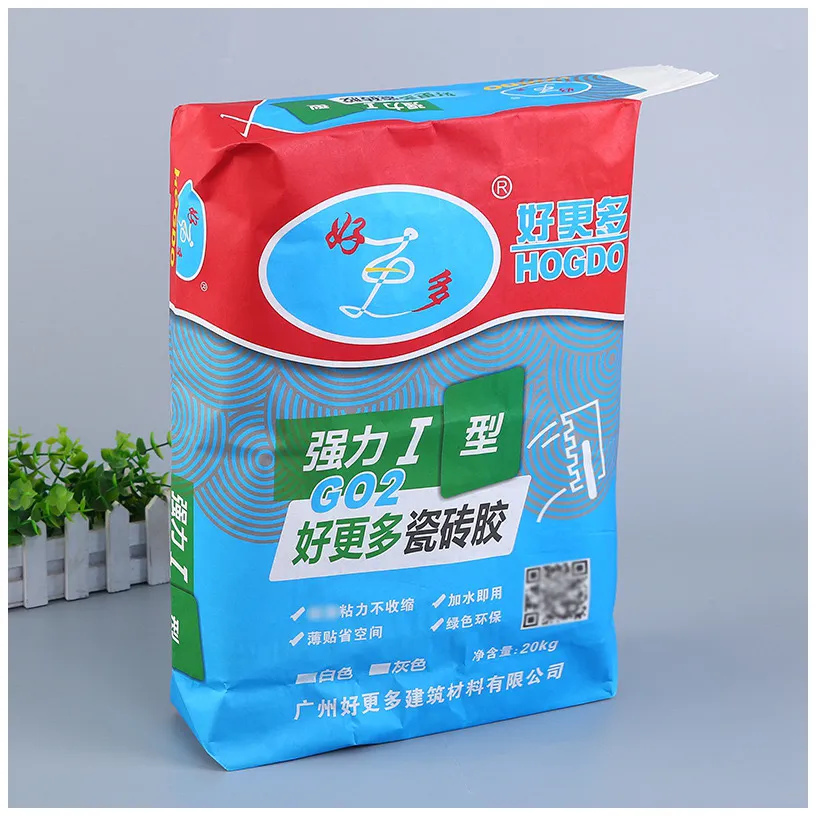
Pasted Valve Bags are an integral packaging solution for various industries due to their high durability, versatile applications, and innovative valve designs. These bags cater to the needs of manufacturers who require efficient and effective packaging for a range of products, including cement, fertilizers, chemicals, and construction materials. In this article, we delve into the unique features and benefits of Pasted Valve Bags and outline the advanced production processes employed at VidePak using high-tech equipment from Starlinger and W&H.
Key Features of Pasted Valve Bags
Pasted Valve Bags, also known as Pasted Valve Sacks or Valve PP Bags, provide exceptional strength and versatility due to their distinctive features:
Feature | Description |
---|---|
Durability | Made with high-quality polypropylene (PP), these bags offer excellent strength, ensuring they can withstand rough handling and various environmental conditions. |
Moisture Resistance | With optional lamination, Pasted Valve Bags provide superior moisture resistance, which is ideal for protecting contents sensitive to moisture. |
Block Bottom Design | The block bottom construction enables the bags to stand upright, providing stability and efficient stacking, which maximizes storage and transport efficiency. |
Customizable Valves | The valve options allow for quick and easy filling, ideal for high-speed filling lines. Valves can be designed for manual or automated filling processes. |
Printing Options | High-quality printing is available for clear branding and product information, enhancing brand visibility and customer recognition. |
Eco-Friendly Options | Made from recyclable polypropylene, these bags support environmental sustainability efforts by reducing waste and resource usage. |
Pasted Valve Bags are available in a range of specifications to cater to various needs, including block bottom and sewn open mouth versions. The next sections will explore the sophisticated, automated manufacturing process that VidePak uses to produce these high-quality bags efficiently.
Advanced Manufacturing Process for Pasted Valve Bags
The production of Pasted Valve Bags involves a series of precise, automated steps, including extrusion, weaving, cutting, printing, coating, and quality inspection. At VidePak, this entire process is powered by cutting-edge machinery from Austria’s Starlinger and Germany’s W&H, which ensures high-speed, high-precision production with minimal human intervention. The following is an in-depth overview of each stage in the manufacturing process.
1. Extrusion and Tape Production
The process begins with the extrusion of polypropylene (PP) granules. In this stage, PP resin is melted and passed through extrusion lines, where it is shaped into thin, durable tapes that will be woven into fabric. The tape lines at VidePak can reach speeds of up to 200 tapes per minute, ensuring high productivity and consistent quality.
- Starlinger Extruders: Known for their reliability and efficiency, these extruders deliver uniform tape quality and allow for adjustments in thickness and width, providing flexibility for different bag specifications.
- Cooling and Winding: After extrusion, the tapes are rapidly cooled and wound onto spools, ready for the weaving process.
2. Weaving
The woven fabric is created using circular looms, which interlace the tapes into a durable and flexible structure. The weaving process is essential to achieving the desired tensile strength and flexibility in the bags.
- Circular Looms: VidePak employs 150 high-speed circular looms from Starlinger. These looms operate in a fully automated manner, significantly enhancing output and consistency.
- Block Bottom Technology: This technology is incorporated at this stage, ensuring the bags can stand upright when filled, which improves handling and stacking capabilities.
3. Cutting and Sewing
Once the fabric is woven, it is cut and sewn to form the basic bag shape. This stage includes forming the valve for easy filling and sealing.
- High-Speed Cutting Machines: Automated cutting equipment ensures precision in sizing, and the multi-bag output feature allows VidePak to produce up to 200 bag sections per minute.
- Valve and Block Bottom Formation: The fabric is folded and pasted to create the block bottom and valve opening. This design supports quick filling and enhances the bag’s structural integrity.
4. Printing and Coating
VidePak offers advanced printing options to cater to branding and product information needs. Using state-of-the-art Starlinger and W&H printing machines, bags can be printed in vibrant, multi-color designs, maintaining clarity even after rough handling.
- Flexographic and Offset Printing: These printing methods allow for detailed graphics and text, ideal for product branding.
- Lamination and Coating: An optional step, coating provides extra protection for moisture-sensitive contents. VidePak’s lamination machines, totaling 32 units, apply a thin PP layer to the fabric, enhancing durability and moisture resistance.
Quality Control and Inspection
To maintain the high standards expected of Pasted Valve Bags, VidePak employs rigorous quality control at every stage of production. Automated inspection systems and regular manual checks ensure that each bag meets the company’s high standards for durability, strength, and appearance.
Quality Parameter | Inspection Method | Frequency |
---|---|---|
Tensile Strength | Automated tensile testing machines | Sampled from each batch, ensuring durability against wear and tear. |
Moisture Resistance | Moisture ingress tests | Tested for coated bags, ensuring sufficient protection for sensitive products. |
Print Quality | Visual and automated inspection | Each batch is checked to maintain brand standards and ensure clarity and visibility. |
Valve Functionality | Manual and automated fill testing | Ensures the valve’s efficiency during filling and secures a firm seal post-filling. |
Bag Dimensions | High-precision measurements | Regular checks for consistent sizing, which is crucial for fitting onto filling machinery. |
Packaging and Delivery
After passing all quality inspections, the Pasted Valve Bags are packaged for delivery. The packaging process is automated and ensures that each bag remains in optimal condition until it reaches the client.
- Automated Packing Lines: VidePak utilizes automated packing lines that streamline the packaging process, ensuring efficient and accurate packing for large orders.
- Shipping and Distribution: With a strong distribution network, VidePak serves clients in major global markets, including North America, Europe, and Asia. The packaging process is optimized for safe and secure transport.
Applications and Versatility of Pasted Valve Bags
Pasted Valve Bags serve a wide range of industrial applications due to their customizable design and robust construction. These bags are especially popular in sectors that demand high-quality, durable, and user-friendly packaging solutions.
- Construction Materials: Ideal for packaging cement, sand, and other construction materials, Pasted Valve Bags offer durability and moisture protection.
- Chemical and Fertilizer Packaging: The valve and block bottom design allows for easy filling and reliable sealing, which is essential for powdery or granular materials.
- Food and Agricultural Products: Safe for non-food-grade and industrial applications, these bags can also be customized with food-grade liners for agricultural products.
- Retail and Wholesale Distribution: With customizable printing options, the bags are suitable for direct-to-consumer packaging, enhancing brand visibility and ease of use.
Conclusion
VidePak’s Pasted Valve Bags stand out in the packaging industry due to their durable construction, versatile applications, and customizable features. Leveraging advanced machinery from Starlinger and W&H, VidePak achieves a high level of automation and efficiency, producing bags that meet diverse client needs across global markets. For companies seeking a high-performance packaging solution, these Valve PP Bags provide unmatched reliability, efficiency, and customizability, ensuring safe and effective storage for a wide range of products.