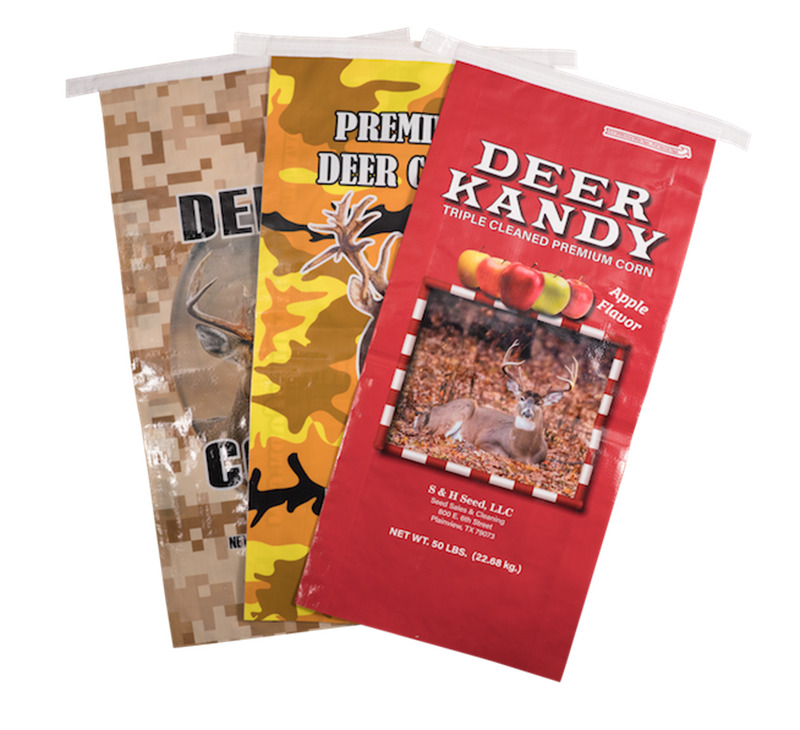
- The Power of Automation in Form-fill-seal Woven Bags
- Key Advantages of FFS PP Bags and FFS Woven Bags
- Ensuring Quality Control with High-Grade Materials
- The Importance of FFS Woven Bags Thickness and Tolerance Standards
- Specialized Printing Techniques for Durability
- The Role of Starlinger Technology in Manufacturing
- Product Parameters and Specifications
- Conclusion
In the packaging industry, Form-fill-seal Woven bags have become a critical component for businesses aiming to streamline their packaging processes and ensure the quality of their products. As industries demand greater efficiency and precision in their packaging systems, FFS Woven Bags have gained recognition for their advanced automation features and the ability to uphold high standards in product integrity. This article explores how Form-fill-seal Woven sacks integrate automation, quality control, and standardized practices to deliver superior packaging solutions. We will also focus on the importance of using high-quality materials like new PP and PE particles to guarantee durability, as well as the special printing techniques that enhance the bag’s visual appeal and longevity.
The Power of Automation in Form-fill-seal Woven Bags
The advent of automation has had a profound impact on the packaging industry, and Form-fill-seal Woven bags are at the forefront of this transformation. Through advanced machinery and technology, these bags are automatically filled and sealed during the packaging process, eliminating the need for manual labor and significantly enhancing production speed and accuracy.
The process begins when the fabric is unrolled and passed through a system of machines that perform various operations such as forming, filling, and sealing the bags. The precision of the machinery ensures that each bag is consistently produced according to specified standards, with minimal variation in size, weight, and sealing strength. This automation process is particularly valuable in industries that require bulk packaging, such as agriculture, construction, and food production.
Key Advantages of FFS PP Bags and FFS Woven Bags
One of the standout advantages of FFS PP Bags is their ability to achieve high-speed, high-volume packaging without sacrificing quality. The use of polypropylene (PP), a material known for its strength and flexibility, ensures that the bags are both durable and resistant to wear and tear. This makes them ideal for storing a wide range of products, from powders and grains to chemicals and fertilizers.
FFS Woven Bags also offer a high degree of customization, allowing businesses to tailor their packaging to suit specific needs. This includes variations in size, strength, and print design. By incorporating cutting-edge technologies like the Starlinger equipment, these bags offer a level of automation that is unmatched, making them an essential choice for companies looking to optimize their packaging efficiency and reduce operational costs.
Ensuring Quality Control with High-Grade Materials
The quality of Form-fill-seal Woven sacks is heavily influenced by the raw materials used during their production. At VidePak, the commitment to quality begins with the selection of new PP and PE pellets, which are sourced from reputable suppliers known for their high-grade materials. These raw materials play a critical role in ensuring that the final product is strong, durable, and able to withstand harsh conditions during transportation and storage.
The use of new PP and PE particles ensures that the bags are resistant to punctures, tears, and abrasions. The material’s inherent resistance to moisture and UV degradation adds another layer of protection, making these bags suitable for use in both indoor and outdoor environments. Furthermore, the thickness of the woven fabric is carefully controlled, ensuring that the bags provide ample strength without being overly bulky.
The Importance of FFS Woven Bags Thickness and Tolerance Standards
One of the key features that distinguish high-quality FFS Woven Bags from lower-quality alternatives is their consistent thickness and adherence to tolerance standards. By applying precise engineering standards, Form-fill-seal Woven bags are produced with exacting specifications in terms of thickness, weight, and strength. This ensures that the bags maintain their structural integrity even under heavy loads.
The adoption of positive tolerance standards means that every FFS PP Bag is manufactured within a tightly controlled range, eliminating the risk of production flaws. This approach prevents issues such as “bag blowouts,” a common problem that occurs when bags are underfilled or overfilled. The consistent and accurate production of FFS Woven Bags ensures that the packaging solution is both reliable and secure.
Specialized Printing Techniques for Durability
In addition to their structural qualities, FFS Woven Bags benefit from specialized printing techniques that enhance both their functionality and appearance. By using advanced printing technologies, VidePak ensures that each bag’s branding and labeling are sharp, clear, and resistant to fading. This is particularly important for companies that need to display vital information, such as product contents, handling instructions, and branding elements, on their packaging.
The durability of the prints on Form-fill-seal Woven sacks is crucial for maintaining a professional appearance throughout the product’s lifecycle. Exposure to sunlight, chemicals, and environmental factors can cause conventional prints to fade over time, but the advanced printing processes used in FFS Woven Bags ensure that they maintain their clarity and vibrancy, even after prolonged exposure.
The Role of Starlinger Technology in Manufacturing
A major factor contributing to the exceptional quality of Form-fill-seal Woven bags is the use of equipment from Starlinger, a globally recognized supplier of woven fabric production technology. Starlinger’s innovative machinery offers unparalleled precision and efficiency in the production of woven bags. By integrating this advanced equipment into the manufacturing process, VidePak is able to achieve high levels of automation, consistency, and quality in every batch of FFS Woven Bags produced.
Starlinger’s equipment ensures that each stage of the production process—from extrusion to weaving, lamination, and printing—is executed with the utmost accuracy. This technology also allows for real-time monitoring and adjustments, further enhancing the stability and quality of the final product. As a result, FFS Woven Bags produced with Starlinger machinery offer superior performance and reliability, which translates into fewer defects and a higher overall product lifespan.
Product Parameters and Specifications
To further demonstrate the superior qualities of FFS Woven Bags, let’s take a look at the typical parameters and specifications for these products:
Parameter | Specification |
---|---|
Material | New PP/PE Pellets |
Thickness | 50 to 150 microns |
Width | 300mm to 1200mm |
Length | Customizable |
Printing Type | High-resolution flexographic |
Tensile Strength | Up to 160 N/cm |
Weight | 50 to 150 grams per bag |
Sealing Type | Heat-sealed, double seams |
Tolerance | Positive tolerance standard |
UV Protection | Yes |
Moisture Resistance | Yes |
Durability | High (up to 2 years of exposure) |
Conclusion
The integration of Form-fill-seal Woven bags into the packaging process offers companies an efficient, high-quality, and automated solution to packaging needs. By utilizing new PP and PE pellets, maintaining precise thickness standards, and leveraging Starlinger technology, businesses can ensure that their packaging is both reliable and durable. The result is a packaging solution that not only protects the contents but also enhances the visual appeal and brand recognition of the product. With these advancements, the future of packaging continues to evolve, providing businesses with cost-effective and innovative solutions.
For more information about FFS PP Bags, you can explore how VidePak is enhancing packaging solutions across industries with their expertise in the field. Additionally, learn more about Form-fill-seal Woven bags and the role they play in the evolution of packaging technologies at this link.