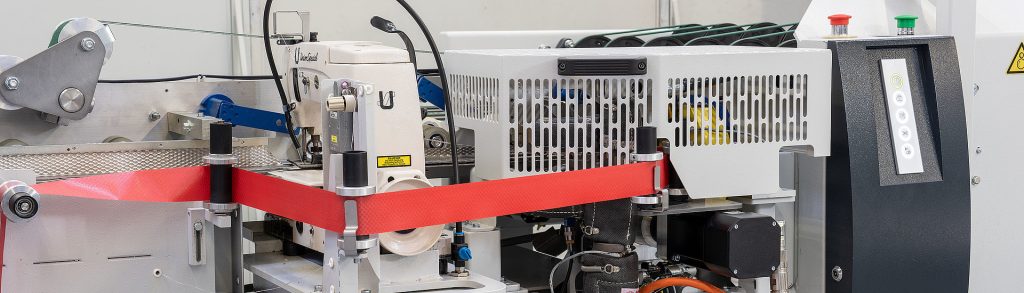
Leakproof woven bags play an essential role in industries requiring reliable containment, offering secure and efficient packaging solutions for products sensitive to leakage. In achieving effective leak prevention, VidePak utilizes advanced equipment and carefully selected materials that enhance the bags’ structural integrity. This article will explore how leakproof woven bags achieve their exceptional performance, comparing fine and coarse yarn choices, and the importance of using high-quality machinery from Starlinger and W&H.
Key Components of Leakproof Woven Bags
Leakproof woven bags, also known as leakproof woven sacks or leakproof PP bags, are made from polypropylene (PP), a lightweight, durable material that withstands environmental stress while ensuring product safety. Our company’s expertise lies in manufacturing these bags to the highest standards of leak resistance, making them suitable for bulk storage and transportation of various materials, including foodstuffs, chemicals, and construction materials. The leakproof capabilities of these bags hinge on multiple factors:
- Material Composition and Yarn Selection: Fine or coarse polypropylene yarns are selected based on their characteristics and the intended application, providing a balance between strength and flexibility.
- Advanced Equipment: Starlinger and W&H machinery enhances the precision in manufacturing, ensuring uniformity in the bag structure and maximizing leakproof performance.
- Customization Options: The bags can be customized with different closures and valve systems, which reduce leak risks during handling and transport.
Leakproof Woven Bags are in high demand globally, especially where bulk handling of granules, powders, and liquid products requires secure, efficient packaging.
Fine vs. Coarse Yarn: Performance and Selection
The choice between fine and coarse yarn in manufacturing leakproof woven bags significantly influences the bag’s properties. Fine yarn offers a smoother finish and tighter weave, which is ideal for applications where minimal air permeability is critical. Coarse yarn, in contrast, provides enhanced strength, making it suitable for heavy-duty applications that require durability over prolonged usage. Below is a comparative analysis of fine and coarse yarn in leakproof woven bags:
Yarn Type | Properties | Applications | Advantages |
---|---|---|---|
Fine Yarn | Tighter weave, smoother texture | Ideal for storing powders, small granules, and liquids | Better for leakproofing, smooth print surface |
Coarse Yarn | Rougher texture, looser weave | Suitable for heavy, abrasive materials like gravel, sand | High durability, resistance to puncture |
The choice of yarn directly impacts the bag’s leakproof capabilities and functionality. Fine yarn enhances the leakproof quality due to its denser structure, making it more effective in reducing leakage of fine or liquid materials. Meanwhile, coarse yarn bags offer durability and resistance to tearing, albeit with slightly reduced leakproofing.
The Role of Advanced Equipment in Leakproofing
The precise construction of leakproof woven sacks depends on the high-tech equipment used in their production. At VidePak, we utilize Starlinger’s circular looms and W&H’s extrusion and printing technology, ensuring that every bag produced meets stringent quality standards.
1. Starlinger Circular Looms:
Starlinger’s circular looms are renowned for their efficiency in producing woven fabrics with consistent weave density. This consistency is critical for leakproof applications, where even minor variations in weave can compromise bag integrity. Starlinger looms offer adjustable settings that allow fine control over the yarn tension and weave, ensuring that both fine and coarse yarns are woven precisely.
2. W&H Extrusion and Lamination Machines:
Extrusion lines by W&H are vital in the production of durable polypropylene sheets. By using W&H’s lamination machinery, VidePak adds protective layers to our leakproof poly bags, creating a reliable barrier against moisture and other environmental factors. Lamination also contributes to structural strength and provides an additional leak-resistant layer, making these bags suitable for handling sensitive or hazardous materials.
3. Printing and Customization with W&H Technology:
High-quality printing on leakproof woven bags enhances brand visibility while maintaining the integrity of the material. W&H printing machines ensure accurate, high-resolution prints on the bags without compromising the leakproof qualities. Customizations, such as valve closures and gusseted designs, are also enabled by W&H’s technology, catering to specific requirements that reduce leakage risks in various environments.
Leakproof Woven Sacks from VidePak leverage these advanced technologies, providing consistent quality and customized solutions for various industries.
Leakproof Bag Testing and Quality Assurance
Leakproof woven bags undergo stringent quality control processes to ensure leak prevention and durability under different conditions. Quality assurance measures include:
- Strength Testing: Ensures the fabric’s tensile strength is adequate for the specified load, especially for coarse-yarn woven bags designed to carry heavy materials.
- Leakage Testing: Tests include air-tightness assessments and moisture resistance to guarantee leakproof performance.
- Seam Integrity: Strong seams are essential to prevent leakage, particularly for bags handling liquid or powdered contents. Starlinger and W&H machinery facilitate seamless welding and precision sewing, improving seam durability.
These quality control processes guarantee that each bag meets VidePak’s high standards for leakproofing, ensuring safety and reliability for our customers.
Product Variations and Customization for Different Applications
Leakproof woven bags, often customized based on industry needs, offer versatile solutions for specific applications. Below are some key customization options that enhance leakproof qualities:
Customization | Benefit | Example |
---|---|---|
Lamination | Adds a water-resistant layer | Suitable for agriculture and chemical industries |
Valve Closure | Reduces leakage during handling | Used in bags for cement and fine powders |
Gusseted Design | Increases capacity and leakproof ability | Popular in animal feed and construction materials |
Fine Yarn Construction | Enhances barrier against moisture | Ideal for food packaging and pharmaceutical storage |
Such flexibility in customization ensures that Leakproof PP Bags can meet the unique demands of various industries, from food and pharmaceuticals to agriculture and chemicals.
Conclusion
In conclusion, the manufacturing of leakproof woven bags is a precise process that combines material selection, advanced equipment, and customization to meet the demands of multiple industries. Fine and coarse yarns offer distinct advantages, catering to applications requiring either enhanced leakproofing or robust durability. Advanced machinery, particularly from Starlinger and W&H, plays a critical role in achieving the desired quality and precision in every bag, enabling VidePak to provide high-quality, reliable leakproof woven bags.