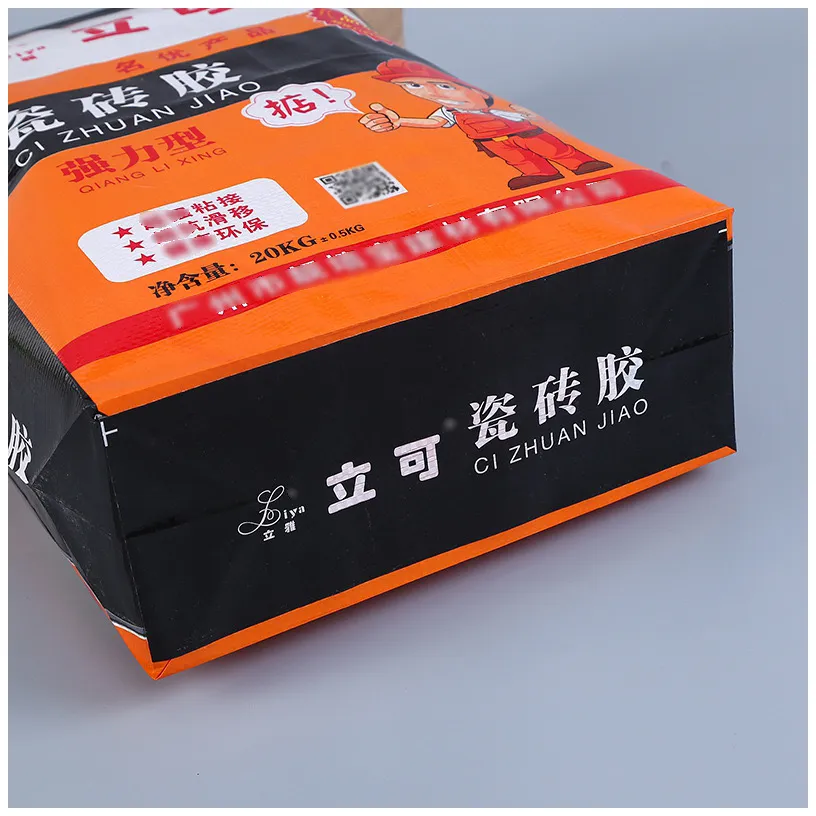
- Mechanisms for Waterproofing in Woven Bags
- Advantages of Waterproof Woven Bags for Construction Materials
- International Standards and Choosing the Right Waterproof Woven Bag Parameters
- Choosing the Ideal Waterproof Woven Bag for Your Application
- Summary Table of Waterproof Woven Bag Features and Applications
- Conclusion
In industries handling construction materials such as cement, sand, putty powder, and gypsum, effective packaging solutions are paramount to prevent material damage and leakage. Waterproof woven bags have become the preferred choice due to their high resilience, protective capabilities, and compliance with international standards. This article explores the waterproofing mechanisms in woven bags, their application in protecting construction materials, and the selection parameters that align with various standards, including European (EN), American (ASTM), Japanese (JIS), and Australian (AS) standards.
Mechanisms for Waterproofing in Woven Bags
Waterproof woven bags are specifically designed to resist moisture intrusion and environmental factors that may compromise the integrity of their contents. These bags are made using a variety of techniques and materials, which enhance their waterproofing abilities:
- Lamination of PP Woven Fabric:
One of the most effective ways to make woven bags waterproof is by laminating the polypropylene (PP) woven fabric with a layer of low-density polyethylene (LDPE) or BOPP film. This lamination layer acts as a barrier, preventing water from seeping into the bag. - Incorporation of PE Liners:
PE liners, which are placed inside the woven bag, offer an additional layer of waterproofing. These liners can either be stitched or glued, depending on the bag’s intended use. PE-lined waterproof woven sacks are ideal for products like cement and other powdered substances, ensuring that the contents stay dry even in high humidity. - Sealing Techniques:
Heat sealing or ultrasonic sealing methods are often used to seal the bags, creating a near-impenetrable barrier to water. In valve bags, this sealing can significantly enhance water resistance, especially for products that require added protection. - UV-Resistant and Anti-Static Treatments:
Additional coatings and treatments, such as UV resistance and anti-static treatments, can also be applied to the woven fabric. These treatments not only increase the durability of the bags but also prevent degradation from sunlight and static, which can indirectly affect moisture resistance.
For a detailed look at these waterproofing technologies, you can read about VidePak’s approach to Waterproof Woven Bags.
Advantages of Waterproof Woven Bags for Construction Materials
Waterproof woven bags provide crucial advantages in protecting materials, particularly powdered ones that are prone to environmental damage:
- Moisture Control: For materials like cement and gypsum, moisture exposure can lead to solidification or degradation, rendering the materials unusable. Waterproof woven bags prevent moisture from penetrating the bag, preserving material quality.
- Leakage Prevention: With secure seals and high-density woven structures, these bags contain powdered materials without any leakage, even when subjected to rough handling.
- Resistance to Tears and Punctures: The woven structure of these bags provides superior strength, making them ideal for the heavy handling typical in construction settings.
Learn more about how Waterproof Woven Sacks protect against leakage and damage.
International Standards and Choosing the Right Waterproof Woven Bag Parameters
When selecting waterproof woven bags for specific materials, it’s essential to consider the relevant standards that govern packaging quality and durability. Below is an analysis of key parameters across EN, ASTM, JIS, and AS standards:
Standard | Primary Considerations | Key Parameters |
---|---|---|
EN (Europe) | Durability, moisture resistance, recyclability | Tensile strength, water vapor transmission rate (WVTR), material thickness |
ASTM (USA) | Barrier effectiveness, puncture resistance | WVTR, puncture resistance (psi), material gauge |
JIS (Japan) | Environmental resilience, UV stability | UV resistance, tensile strength (N/m), elongation at break |
AS (Australia) | Heat resistance, tear strength | Heat seal strength, tear resistance (g), UV protection level |
- EN Standards:
European standards emphasize environmental protection and durability. WVTR (Water Vapor Transmission Rate) is a crucial parameter, especially for construction materials. European waterproof woven bags must ensure a low WVTR to maintain dryness within the bag. - ASTM Standards:
ASTM standards in the U.S. focus on barrier effectiveness and puncture resistance, essential for heavy-duty applications like cement packaging. A robust material gauge and high puncture resistance are mandatory for waterproof PP bags under ASTM standards. - JIS Standards:
Japan’s JIS standards prioritize environmental resilience. This includes a requirement for UV stability and high tensile strength, ensuring that waterproof poly bags can withstand exposure to sunlight and rough handling without compromising moisture resistance. - AS Standards:
Australian standards demand heat and tear resistance, ensuring bags can perform well under extreme conditions. This is particularly useful for materials like gypsum and putty powder, where high heat resistance helps prevent bag degradation.
For customizable options in waterproof woven bags that meet these international standards, visit VidePak’s Waterproof PP Bags.
Choosing the Ideal Waterproof Woven Bag for Your Application
Selecting the right waterproof woven bag involves considering several factors that affect both product protection and handling efficiency:
- Material Thickness:
Thicker material gauges are recommended for heavier and abrasive contents like cement and sand, while finer gauges work well for lighter, moisture-sensitive materials like gypsum powder. - Bag Capacity and Load Rating:
Depending on the quantity and weight of the material, the capacity of waterproof woven bags varies. Bulkier materials may require reinforced bags with higher load ratings, ensuring safe stacking and transportation. - Valve and Liner Options:
For powdered materials like putty powder and gypsum, valve bags with built-in liners are ideal, as they allow easy filling and sealing while preventing dust leakage. Such designs are also compliant with various international standards, making them versatile for global distribution. - UV and Static Protection:
For bags exposed to sunlight or static environments, UV-resistant and anti-static treatments are recommended. These features are often included in bags designed for European and Australian markets.
Summary Table of Waterproof Woven Bag Features and Applications
Material Type | Recommended Bag Features | Ideal Bag Specification (Example) |
---|---|---|
Cement | Thick gauge, puncture resistance, laminated exterior | BOPP-laminated, 90 GSM, UV-treated |
Gypsum Powder | Valve bags with PE liner, heat-sealed | Valve bag, 75 GSM, anti-static |
Putty Powder | Double layer, low WVTR, anti-leak seals | Double-coated, 80 GSM, heat-sealed |
Sand | Tear-resistant, reinforced handles, water barrier coating | Poly-coated, 100 GSM, UV-protected |
Conclusion
Waterproof woven bags are indispensable in the construction industry, where they safeguard valuable materials from environmental factors and prevent leakage during transportation. With advanced lamination, sealing, and material treatments, these bags provide unmatched protection and meet rigorous international standards across diverse markets. By carefully choosing waterproof woven bags that meet specific standards and applications, businesses can ensure their materials arrive intact and ready for use, optimizing efficiency and cost-effectiveness.