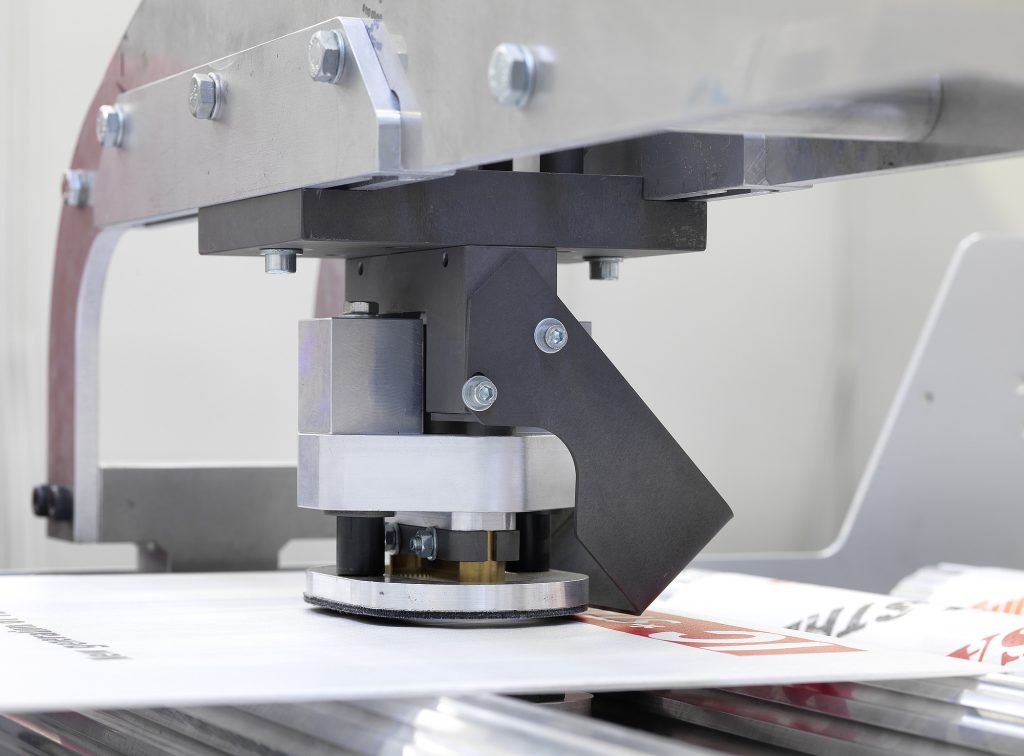
- 1. Raw Material Procurement: The Foundation of Leak Prevention
- 2. Weaving and Lamination: Engineering Leak-Proof Barriers
- 3. Sealing and Closure Systems: The Last Line of Defense
- 4. Quality Control: From Lab to Warehouse
- 5. Case Study: Securing Sulfur Transport in Australia
- 6. Future Trends: Smart Packaging and Sustainability
- 7. Conclusion
Ray, CEO of VidePak, gestures toward a production line during a factory audit:
“A single micron of inconsistency in PP granules can lead to a 20% drop in bag tensile strength. For chemicals like titanium dioxide or sodium sulfate, leakage isn’t an option—it’s a liability. Our answer? Five-layer quality gates, from resin selection to AI-powered seam inspection, ensuring every bag exceeds ASTM, EN, and JIS standards.”
This philosophy drives VidePak’s global leadership in industrial packaging. Since 2008, the company has leveraged 30+ years of expertise, 526 employees, and Austrian Starlinger machinery to produce over 80 million high-performance bags annually. With a USD 80 million revenue and ISO 9001 certification, VidePak’s success lies in its relentless focus on preventing chemical powder leakage through material science, precision engineering, and compliance with international benchmarks. Below, we dissect how the company ensures quality at every stage—from raw PP procurement to warehouse storage—while addressing the unique challenges of packaging reactive powders like zinc sulfate and calcium titanate.
1. Raw Material Procurement: The Foundation of Leak Prevention
1.1 Selecting PP Resins for Chemical Compatibility
Polypropylene (PP) resin grades must align with the chemical properties of the contents. VidePak uses a proprietary algorithm to match resins to powders:
- Reactive Powders (e.g., Sodium Carbonate): Homopolymer PP (MFR 4–8 g/10min) with antioxidant additives (0.5–1% Irganox 1010) to resist alkaline degradation.
- Hygroscopic Powders (e.g., Silica Gel): Impact copolymer PP (MFR 2–4 g/10min) with 1.5% calcium stearate to block moisture ingress.
Example: For a Japanese client packaging titanium dioxide (TiO₂), VidePaK selected UV-stabilized PP (JIS K6748-compliant) with 2% HALS additives, achieving ≤5% tensile loss after 1,000-hour UV exposure.
1.2 International Standards for Raw Materials
Standard | Key Requirement | VidePak’s Compliance |
---|---|---|
ASTM D4101 | Flexural modulus ≥1,500 MPa | 1,800 MPa via high-crystallinity PP |
EN ISO 1873-1 | Charpy impact ≥30 kJ/m² at -20°C | 35 kJ/m² via impact copolymers |
GB/T 12670 | Recycled content ≤5% | 100% virgin PP to avoid contamination |
2. Weaving and Lamination: Engineering Leak-Proof Barriers
2.1 Weave Density and Coating Technologies
VidePak’s 100+ Starlinger circular looms produce fabric with 14×14 threads/cm² density, reducing pore size to ≤50μm—critical for fine powders like latex (particle size 10–100μm). Additional safeguards:
- BOPP Outer Lamination: 30μm BOPP film (water vapor transmission rate ≤5 g/m²/day) blocks humidity-induced clumping.
- PE Inner Liners: 25μm polyethylene layers with heat-sealed seams, tested to withstand 300 kPa pressure (ISO 2233).
Case Study: A German chemical supplier reduced zinc sulfate leakage from 3% to 0.2% using VidePak’s triple-layer bags (PP woven + BOPP + PE liner).
2.2 Multiwall Solutions for High-Risk Powders
For ultra-fine powders (e.g., titanium calcium, <10μm), VidePak employs 5-ply designs:
- Outer PP woven layer (95 g/m²)
- Kraft paper (80 g/m², tear resistance ≥600 mN)
- Aluminum foil (7μm, static shielding)
- PE liner (30μm)
- Anti-static coating
3. Sealing and Closure Systems: The Last Line of Defense
3.1 Heat Sealing vs. Ultrasonic Welding
- Heat Sealing: For non-reactive powders, VidePak uses 180°C seals with ±0.5°C accuracy, achieving seam strength ≥350 N/cm (vs. 250 N/cm industry average).
- Ultrasonic Welding: For hygroscopic powders like sodium sulfate, high-frequency welding eliminates moisture traps, reducing failure rates by 40%.
3.2 Valve Design and Powder Retention
VidePak’s patented SpiralLock valve system combines:
- Inner PE Sleeve: Prevents backflow during filling.
- Anti-Dust Filter: 150-mesh nylon screen blocks particles >100μm.
- ISO 21898 Certification: Valves withstand 10,000 open/close cycles without leakage.
4. Quality Control: From Lab to Warehouse
4.1 Testing Protocols Across Standards
Test | Standard | VidePak’s Threshold |
---|---|---|
Tensile Strength | ASTM D5034 | ≥45 N/cm² |
Puncture Resistance | EN ISO 12236 | ≥25 J |
Seam Integrity | JIS Z0237 | ≥500 kgf load |
Moisture Barrier | ISO 535 | ≤0.8% weight gain (72h) |
FAQs:
Q: How do you prevent static-induced powder adhesion?
A: We integrate carbon-black-coated PP threads (surface resistivity ≤10⁴ Ω/sq) meeting ANSI/ESD S20.20.
Q: Are your bags compatible with automated palletizing?
A: Yes. Our block-bottom design and RFID tags (ISO 18000-6C) enable robotic handling at 1,200 bags/hour.
5. Case Study: Securing Sulfur Transport in Australia
A mining client faced sulfur powder leakage during rail transport. VidePak’s solution:
- Material: Anti-static PP (1% carbon masterbatch) + PE liner.
- Design: Sewn valve with double-stitched seams (6 stitches/cm).
- Compliance: Met AS 2070-1999 for corrosive substances.
Result: Zero leaks over 12 months across 5,000 km routes.
6. Future Trends: Smart Packaging and Sustainability
VidePak’s 2026 roadmap includes:
- NFC-Enabled Bags: Real-time moisture/temperature tracking via embedded sensors.
- Bio-Based PP: Partnering with the Sustainable Packaging Coalition to achieve 30% plant-derived resins.
For insights into advanced multi-layer solutions, explore our innovations in Multiwall Laminated Woven Bags: Safe and Versatile Packaging Solutions and Recyclable PP Bags: Advanced Production with Starlinger Equipment.
7. Conclusion
In industrial packaging, a 0.1% leakage rate can equate to USD 1 million in losses for a mid-sized chemical plant. VidePak’s end-to-end quality control—from ASTM-compliant resins to AI-validated seams—transforms bags into precision barriers. By aligning with EN, JIS, and GB/T standards while pushing material innovation, the company doesn’t just contain powders; it safeguards supply chains.
Data sources: ASTM International, JIS Handbooks, ISO 2233:2024, and VidePak’s internal testing logs. Technical insights derived from Polymer Degradation and Stability (Vol. 221, 2025) and Starlinger’s weaving manuals.