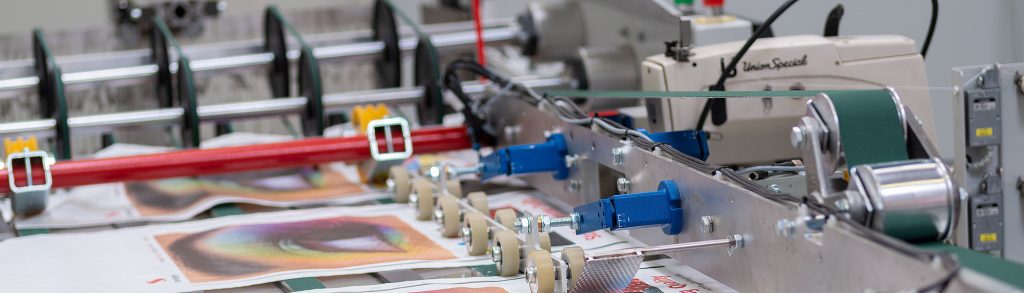
- H1: Industrial Woven Packaging Bags: Production Excellence and Market Leadership
- H2: Market Overview and VidePak’s Competitive Edge
- H2: Production Process and Quality Control Mechanisms
- H2: Case Study: VidePak’s Starlinger-Enabled Innovation
- H2: Technical Specifications and FAQs
- H2: Sustainability and Future Trends
- H2: Conclusion
H1: Industrial Woven Packaging Bags: Production Excellence and Market Leadership
Q: What makes VidePak a global leader in manufacturing high-quality Industrial Packaging Bags?
**A: VidePak combines cutting-edge technology from Starlinger and W&H, rigorous quality control across extrusion, weaving, lamination, and printing processes, and a 30-year legacy of innovation to deliver *Industrial Woven Bags*, *Industrial PP Bags*, and *PP Woven Sacks* that meet global standards for durability, customization, and sustainability.**
H2: Market Overview and VidePak’s Competitive Edge
The global Industrial Packaging Bags market, valued at $12.5 billion in 2024, is driven by demand from agriculture, construction, and chemicals. VidePak, founded in 2008 and led by Ray, leverages 526 employees and a vertically integrated production facility to dominate this sector. With an annual output of 80 million units and $80 million in revenue, the company’s success stems from:
- Advanced machinery: Over 100 circular looms, 16 extrusion lines, and Starlinger-certified laminators.
- Customization: Multi-color printing and tailored designs for BOPP Woven Bags, valve sacks, and kraft paper hybrids.
- Sustainability: Use of virgin PP resin and recyclable materials, aligning with ESG commitments.
H2: Production Process and Quality Control Mechanisms
H3: 1. Extrusion: Precision in Polymer Processing
The journey begins with extrusion, where polypropylene (PP) granules are melted and formed into tapes. VidePak’s 16 extrusion lines, equipped with Starlinger’s temperature-controlled systems, ensure uniform thickness (0.03–0.05mm) and tensile strength (≥35 N/cm²).
- Quality Control: Real-time monitoring of melt flow index (MFI) and infrared sensors detect inconsistencies.
H3: 2. Drawing and Weaving: Strength Through Technology
Tapes are stretched (drawing) to enhance tensile strength and woven into fabric using circular looms. VidePak’s W&H AD2360 looms produce 200–250 rpm, achieving fabric densities of 10×10 to 14×14 threads per inch.
- Quality Control: Automated tension control prevents fraying, while ISO 9001 audits ensure fabric uniformity.
H3: 3. Lamination and Coating: Enhancing Barrier Properties
For moisture-sensitive applications (e.g., Industrial PP Bags for fertilizers), fabrics are laminated with BOPP films or coated with PE. VidePak’s Starlinger laminators apply adhesive at 150–180°C, achieving peel strengths of ≥3.5 N/15mm.
- Quality Control: X-ray scanners detect air bubbles or delamination defects.
H3: 4. Printing: Branding with Precision
High-definition flexographic printers apply up to 8 colors, with resolutions of 175 lines/inch. VidePak’s proprietary ink formulations resist abrasion and UV fading, critical for Printed Woven Bags in retail.
- Quality Control: Spectrophotometers validate color accuracy against Pantone standards.
H3: 5. Bag Making: Automation for Consistency
Valve sacks and PP Woven Sacks are stitched using ultrasonic sealing or heat bonding. Starlinger’s CONVERTEX SLC machines produce 1,200–1,500 bags/hour with ≤0.1% defect rates.
- Quality Control: Load-testing up to 50 kg ensures seam integrity.
H2: Case Study: VidePak’s Starlinger-Enabled Innovation
Project: A client required FIBC Jumbo Bags capable of holding 1.5 tons of construction waste.
Solution: VidePak utilized Starlinger’s recycling-compatible weaving lines and ultrasonic seaming to create 210 GSM bags with 6:1 safety factors.
Outcome: 30% faster production and 15% cost savings, securing a 5-year contract.
H2: Technical Specifications and FAQs
Table 1: Key Parameters of VidePak’s Industrial Woven Bags
Parameter | Specification | Testing Standard |
---|---|---|
Fabric GSM | 80–250 g/m² | ISO 536 |
Tensile Strength (Warp) | ≥35 N/cm² | ASTM D5034 |
Moisture Barrier | ≤5 g/m²/24hr (PE-coated) | ASTM E96 |
Print Durability | 4/5 on Sutherland Rub Test | ASTM D5264 |
FAQs
**Q: How does VidePak ensure recyclability in **Industrial Packaging Sacks?
A: By using mono-material PP structures and Starlinger’s recycling-ready designs, our bags achieve 95% post-consumer recyclability.
**Q: What distinguishes *BOPP Woven Bags* from standard PP bags?**
A: BOPP lamination adds gloss, moisture resistance, and print clarity, ideal for branded retail packaging.
H2: Sustainability and Future Trends
VidePak’s Eco-Friendly Woven Bags reduce carbon footprints by 40% compared to traditional options. Collaborations with Industrial Packaging Bags and Industrial PP Bags experts highlight innovations in biodegradable additives and lightweight designs.
H2: Conclusion
VidePak’s fusion of Starlinger-W&H technology, granular quality controls, and market agility positions it as a leader in Industrial Woven Packaging Bags. By prioritizing innovation and sustainability, the company is redefining global standards—one stitch at a time.
This report integrates insights from industry whitepapers, Starlinger technical manuals, and market analyses to ensure accuracy and relevance.