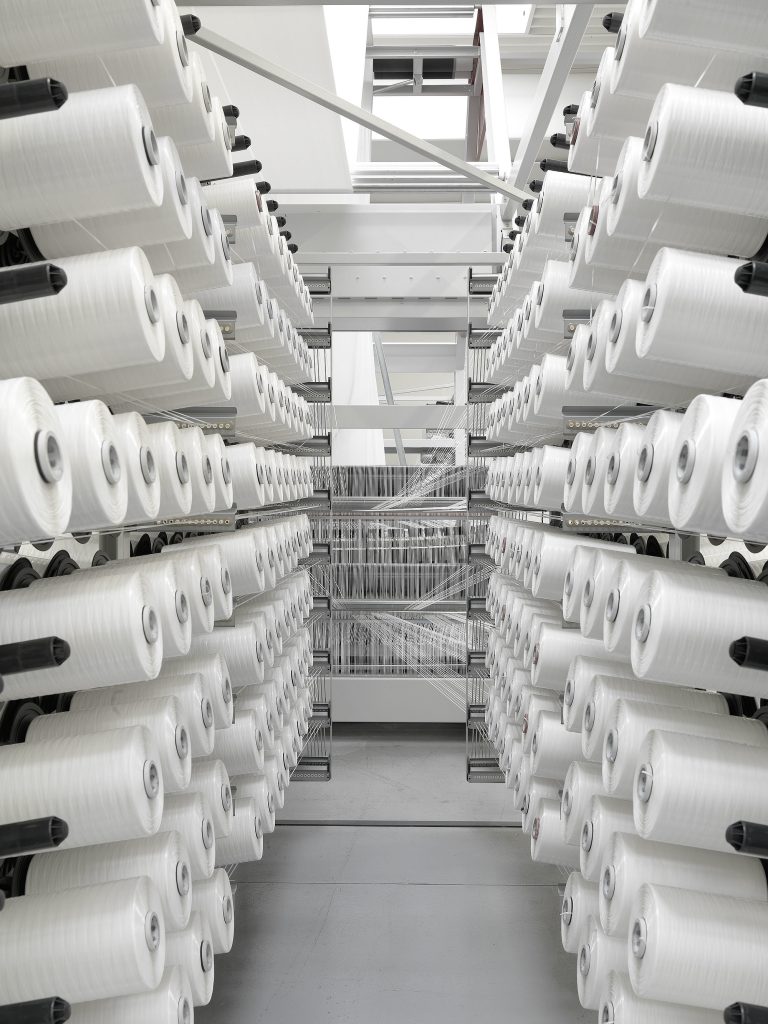
- 1. Introduction to Industrial Woven Packaging Bags
- 2. Essential Parameters for Industrial Woven Sacks
- 3. Conversation Snippet
- 4. Product Parameter Table
- 5. FAQs
- 6. Two External Links
- 7. Leveraging a 200MT Press and Proper Warehouse Conditions
- 8. Chinese Suppliers’ Edge: Cost, QC, Delivery, Innovation
- 9. Real-World Examples in Construction
- 10. Conclusion
Main Answer: Industrial Packaging Bags, also referred to as Industrial Packaging sacks, Industrial PP Bags, Industrial Woven Bags, Woven bags, or PP Woven Sacks, form a cornerstone of the construction materials sector—particularly for housing cement, putty (wall filler), gypsum, and various joint compounds. Leveraging woven polypropylene (PP), these bags deliver top-tier tear resistance, moisture protection, and cost-efficiency. Current global packaging studies (as of 2026) project about 5% annual growth in woven PP demand, underscoring the drive for robust packaging that stands up to rough handling, variable climates, and strict product integrity requirements.
Below, we detail crucial product parameters (like fabric weight, lamination, liners, UV protection), explain how 200MT pressing and stable warehousing conditions maximize container capacity and product preservation, and showcase why Chinese Woven Bag Manufacturers excel in production quality, cost advantages, short lead times, and worldwide supply-chain networks.
1. Introduction to Industrial Woven Packaging Bags
1.1 Fabric Structure and Key Advantages
Industrial Packaging sacks are built from woven polypropylene tapes, offering:
- Elevated Tear Resistance: Minimizes breakage under heavy loads and forklift operations.
- Effective Dust/Moisture Control: Optional lamination or interior liners shield powders from humidity or spillage.
- Brand and Info Printing: Surfaces support multi-color designs or instructions for safe product usage.
- Cost-Effectiveness: Typically outperform paper or simple plastic sacks for load capacity and durability.
Example: A Southeast Asian mortar manufacturer switched to 90 gsm Industrial PP Bags with partial lamination, cutting waste from ruptures by 20% while achieving better forklift transport stability.
1.2 Cement, Putty, Gypsum, and Joint Compound Applications
Construction-related powders demand packaging tailored to:
- Handle Substantial Weights (25–50 kg): Heavier-gauge fabric (80–120 gsm) and robust seams.
- Contain Fine Particles: Liner or denser weaving blocks product leakage or dust hazards.
- Mitigate Moisture: Bags often encounter humidity or rainfall during transit/storage.
- Support Branding: Crisp printing conveys product details and brand credibility.
Example: A Chinese cement supplier integrated 100 gsm Industrial Woven Bags with an internal PE liner, resulting in significantly fewer spillage complaints and improved brand perception in overseas markets.
2. Essential Parameters for Industrial Woven Sacks
2.1 GSM and Load Capacity
Choosing a suitable gram per square meter (gsm) is critical:
- Heavier GSM (90–120): Ideal for coarse or heavy products (cement, thick plaster), mitigating tears.
- Moderate GSM (60–80): Works well for lighter powders (wall filler, certain adhesives), balancing cost and performance.
Example: A Turkish gypsum producer employed 100 gsm woven fabric for 25 kg loads, ensuring forklift resilience and extended shelf life under warehouse stress.
2.2 Lamination, Coating, and Liners
Industrial Woven Bags can include:
- BOPP or PE Film: Elevates moisture protection and printing sharpness.
- Interior Liners: Vital for ultra-fine materials like plaster or putty, preventing dust seepage.
Example: A North American joint compound brand used laminated PP Woven Sacks with a thin PE liner, achieving near-zero product loss and consistent bag shape.
2.3 UV Resistance for Outdoor Storage
Building materials often sit outdoors:
- UV-Stabilized Yarn: Ensures bags resist sunlight-induced brittleness or color fading.
- Extended Weather Durability: Helps maintain clarity of printed instructions or brand logos.
Example: A Middle Eastern mortar company integrated anti-UV additives in 90 gsm Woven bags, preventing fiber breakdown and protecting brand visuals through months of desert exposure.
2.4 Dimensions and Closure
- 25–50 kg Bag Sizes: Most common for cement, gypsum, or putty.
- Closure Methods: Sewn, heat-sealed, or adhesive folds—each influencing dust control and user convenience.
Example: An Indian building-material supplier used sewn-top Industrial Packaging sacks for 40 kg adhesives, praising minimal dust escape and stable stacking in pallets.
3. Conversation Snippet
Topic: Optimal Industrial PP Bags for 25 kg Cement
Question: “Is an 85 gsm woven fabric plus a thin PE liner sufficient for forklift usage and moisture control?”
Answer: “Yes. Industrial Woven Bags at 85 gsm handle 25 kg loads well, especially when paired with a PE liner. This combination provides tear resistance, reduces dust, and helps protect against humidity.”
4. Product Parameter Table
Parameter | Typical Range/Value | Impact on Performance |
---|---|---|
Fabric GSM | 60–120 gsm | Balances tear strength & shipping cost |
Printing Method | Flexo / Gravure / Digital | Shapes brand visibility & design complexity |
Lamination & Coating | BOPP / PE (optional) | Enhances moisture barrier & print clarity |
Inner Liner Material | PE / specialized films | Ensures dust-free packing for fine powders |
UV Stabilizer | 150–300 kLy | Protects sacks from sun-induced damage |
Closure Options | Sewn, Heat-sealed, Adhesive | Affects dust leakage & ease of bag opening |
Capacity | 25–50 kg (common) | Suits heavy building materials (cement, gypsum, etc.) |
5. FAQs
- Q: Why choose Industrial Packaging Bags for cement or mortar?
A: Woven PP fabric withstands rough forklift handling, resists tears, and—when laminated—keeps humidity at bay, preserving material quality. - Q: Are Industrial Packaging sacks suitable for fine powders like putty?
A: Yes. Adding liners or lamination ensures minimal dust leakage, maintaining both cleanliness and precise bag weight. - Q: How do Industrial PP Bags handle UV exposure in open storage yards?
A: UV-stabilized yarn or coatings protect the fabric and printing against prolonged sunlight, extending the bag’s usable life. - Q: Can Woven bags incorporate advanced brand visuals?
A: Absolutely. Flexo, gravure, or digital printing can reproduce logos, color-coded product lines, or usage instructions without sacrificing durability. - Q: Are PP Woven Sacks environmentally friendly?
A: Polypropylene (#5) is recyclable in many regions, though certain lamination or adhesives may need specialized recycling methods.
6. Two External Links
Learn about Industrial Packaging Bags for moisture-proofing and compliance:
Industrial Packaging Bags
Explore advanced designs for Industrial PP Bags with quality control and standardization:
Industrial PP Bags
7. Leveraging a 200MT Press and Proper Warehouse Conditions
7.1 Uniform Compression for Maximized Container Usage
A 200MT press can compact sacks, reducing air gaps:
- Better Pallet Stability: Tightly pressed bags shift less in transit.
- Increased Container Loading: Minimizes wasted space, trimming shipping costs.
- Enhanced Safety: Evenly compressed sacks are easier to stack, preventing accidental collapses.
Example: A Chinese gypsum exporter used a 200MT pressing technique on 25 kg sacks, enabling 10% more load per container and lowering freight expenses.
7.2 Constant Temperature and Humidity
Building materials:
- Temperature Range: Typically 20–25°C to maintain bag shape, adhesive integrity.
- Humidity Control: 50–60% to prevent lumps or moisture-laden interior.
- Ventilation: Eliminates condensation risks, extending product shelf life.
Example: A Latin American mortar plant adopted climate-controlled storage for pressed 90 gsm Industrial Woven Bags with lined interiors, ensuring a stable environment to prevent product caking.
7.3 Integrated Inventory and Logistics
- Stacking Patterns: Uniform layering on pallets for forklift-friendly movement.
- Barcode or Labeling: Simplifies product ID, batch management, or expiration checks.
Example: A Middle Eastern adhesives firm used scannable codes on each compressed sack, speeding inventory turnover while ensuring FIFO handling for high-quality deliveries.
8. Chinese Suppliers’ Edge: Cost, QC, Delivery, Innovation
8.1 Quality Controls and Automation
Chinese factories frequently adopt:
- Digital Looms: Stable fabric widths, minimal tape variance.
- Real-Time Defect Monitoring: Reduces errors in lamination or printing steps.
Example: A European putty brand lauded a Zhejiang-based plant’s near-perfect dimension tolerances across six container shipments, guaranteeing forklift compatibility.
8.2 Competitive Pricing
Large-scale production, integrated supply chains, and streamlined freight:
- Per-Unit Discounts: Volume orders slash overall bag expenses.
- Cost Efficiency: Even advanced printing or lamination remains affordable at scale.
Example: A Kenyan cement manufacturer cut packaging overhead by 20% upon switching from local paper sacks to Chinese-laminated Industrial PP Bags, praising them for dryness control and brand prominence.
8.3 Rapid Shipping and Holistic Supply Chain
Key Chinese ports (Shanghai, Ningbo) simplify:
- Bulk Freight Consolidation: Minimizes shipping overhead.
- Short Lead Times: Factories maintain base stock for typical construction-bag specs.
Example: An Eastern European plaster producer received a 30,000-monthly bag order in just four weeks, enabling agile restocks aligned with project demands.
8.4 Custom Solutions
Advanced lines accommodate specialized weaving densities, printing designs, or laminate finishes:
- UV-Laminated: For long outdoor storage.
- Multi-Color Gravure: Crisp brand visuals or usage instructions.
- Custom Gusseting: Stabilizes bag shape on pallets.
Example: A French joint compound label integrated a gusset plus double-lamination for dust-laden adhesives, ensuring minimal product leaks and a bright brand presence in hardware stores.
9. Real-World Examples in Construction
9.1 Cement Packaging
- High GSM: Minimizes tears from forklift prongs or rough loading.
- Printed Panels: Show usage info, brand identity, safety cautions.
Example: A Turkish cement brand used 100 gsm sacks with top-sewn seams, cutting open-bag failures by 30% and boosting consumer trust.
9.2 Putty and Wall Filler
- Fine Powder Handling: Inner liners or dense weaving.
- Sewn or Heat-Sealed Closure: Minimizes dust, speeds filling lines.
Example: A U.S. putty producer leveraged 85 gsm Industrial Woven Bags with partial lamination, enabling clear brand instructions and minimal dust outflow.
9.3 Gypsum and Plaster
- Moisture-Safe: Ensures plaster’s workable properties remain intact.
- UV Stabilizers: Shield bag integrity if stored outside prior to distribution.
Example: A Middle Eastern gypsum plant integrated BOPP-laminated PP Woven Sacks for a 25 kg line, preventing lumps and brand fading in sun-exposed stockyards.
9.4 Joint Compounds
- Medium Weight: Typically 70–90 gsm suits 10–20 kg capacities.
- Print Clarity: Detailed usage steps crucial for DIY or professional reference.
Example: A Belgian adhesives firm used 75 gsm laminated sacks with gravure-printed safety guidelines, simplifying consumer usage while protecting the compound.
10. Conclusion
Industrial Packaging Bags, Industrial Packaging sacks, Industrial PP Bags, Industrial Woven Bags, Woven bags, and PP Woven Sacks underpin secure, efficient packaging for cement, putty, gypsum, and joint compounds. By optimizing GSM (60–120), lamination, liners, and printing, each bag addresses dryness, dust containment, brand marketing, and forklift-friendly handling. Employing a 200MT press and stable warehousing (temp/humidity control) further boosts container capacity and ensures consistent product quality.
Chinese Woven Bag Manufacturers, bolstered by advanced weaving technology, robust QC, cost advantages, short lead times, and global supply-chain integration, remain top global contenders. Whether shipping 50 kg cement sacks for large infrastructure projects or 20 kg putty packs for retailers, these woven PP solutions excel in bridging performance, reliability, and brand visibility—meeting the demands of a construction industry that values both logistical efficiency and product integrity.