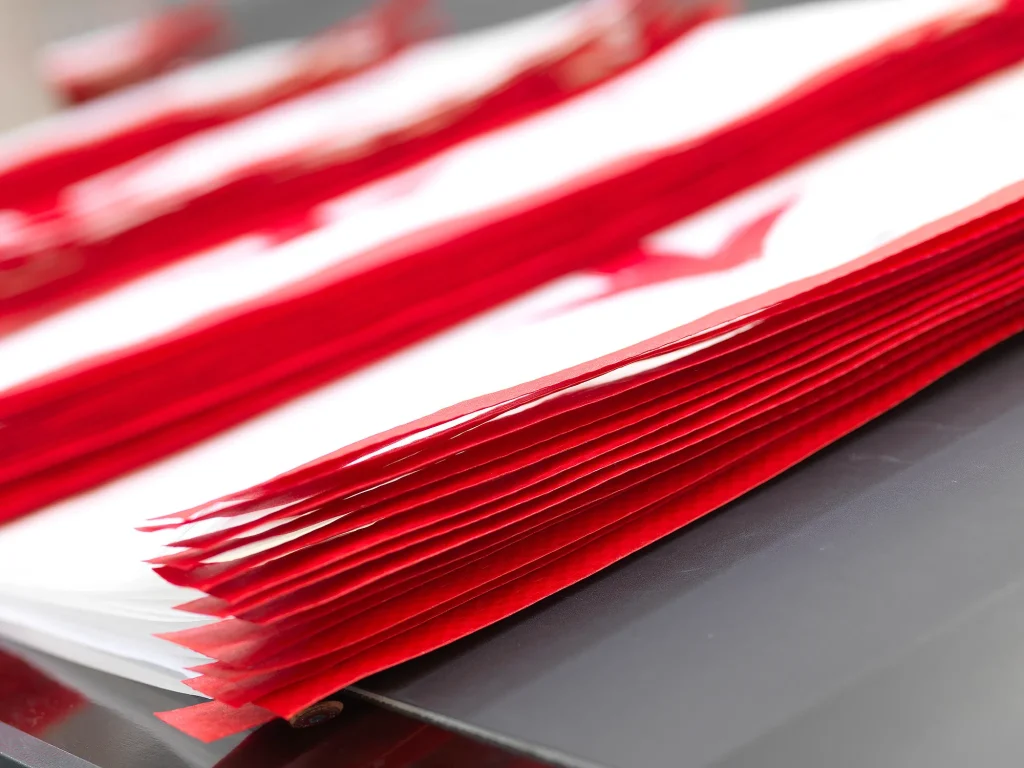
The industrial packaging landscape has undergone transformative changes since the advent of polypropylene (PP) woven bags in the mid-20th century. Today, woven packaging bags are indispensable across industries, combining durability, cost-efficiency, and adaptability, with modern advancements driven by precision engineering and material science. VidePak, a global leader in woven bag manufacturing since 2008, exemplifies this evolution through its adoption of Austrian Starlinger and German W&H machinery, producing over 100 million high-performance bags annually for markets spanning agriculture, chemicals, and construction. This article explores the technical nuances of woven bag production, analyzes filament classifications (fine vs. coarse yarns), and demonstrates how cutting-edge equipment ensures superior product quality.
The Historical Journey of Woven Packaging Bags
Woven bags emerged in the 1950s as a lightweight alternative to jute and burlap sacks. Early iterations used flat tapes of polyethylene, but the introduction of polypropylene in the 1970s revolutionized the industry. PP’s high tensile strength, moisture resistance, and recyclability made it ideal for bulk packaging. By the 1990s, laminated BOPP (biaxially oriented polypropylene) coatings further enhanced barrier properties, enabling use in food and pharmaceutical sectors.
VidePak’s journey mirrors this innovation timeline. With a 30+ year experienced team, the company has leveraged global market insights to refine products like BOPP laminated woven bags and kraft paper composite bags, achieving an annual turnover of $80 million. Their 568 employees operate 100+ circular looms, 16 extrusion lines, and 30 lamination machines, ensuring scalability for custom orders.
Filament Classification: Fine vs. Coarse Yarns
Defining Filament Widths
In woven bag production, yarns are categorized by denier (D), a unit measuring linear mass density:
- Fine yarns: 100–150 denier (width: 0.8–1.2 mm)
- Coarse yarns: 200–300 denier (width: 1.5–2.5 mm)
Comparative Analysis
Property | Fine Yarns | Coarse Yarns |
---|---|---|
Flexibility | High (ideal for intricate weaves) | Moderate (stiffer structure) |
Weight | 60–80 g/m² | 90–120 g/m² |
Surface Smoothness | Excellent (enhances print clarity) | Slightly textured |
Tensile Strength | 400–500 N/5cm | 600–800 N/5cm |
Abrasion Resistance | Moderate | High |
Cost | $0.12–$0.18 per bag | $0.20–$0.30 per bag |
Applications:
- Fine yarns: Ideal for retail-grade bags (e.g., pet food, rice) requiring high-resolution printing and lightweight handling.
- Coarse yarns: Suited for heavy-duty applications (e.g., cement, fertilizers) demanding extreme durability.
VidePak’s BOPP laminated woven bags utilize fine yarns for premium print fidelity, while their FIBC bulk bags employ coarse yarns to withstand 1,000–2,000 kg loads.
Engineering Excellence: Starlinger and W&H Machinery
Advanced equipment is pivotal in achieving yarn consistency and weave precision. VidePak’s investment in Starlinger’s circular looms and W&H extrusion lines ensures:
- Uniform Yarn Thickness: ±5% denier tolerance, eliminating weak spots.
- High-Speed Weaving: 120–150 rpm loom speeds, doubling traditional output.
- Lamination Accuracy: BOPP films applied at 0.02–0.05 mm thickness with <1% defect rates.
For instance, Starlinger’s AD-Star loom integrates AI-driven tension control, optimizing weave density (10×10 to 14×14 threads per inch) based on end-use requirements.
Product Specifications and Customization
VidePak’s flagship products include:
1. BOPP Laminated Woven Bags
- Layers: PP woven fabric + BOPP film + inner PE coating
- Load Capacity: 25–50 kg
- Print Options: Up to 8-color flexography
2. Valve Sacks for Powders
- Material: 120 g/m² coarse yarns + kraft paper laminate
- Valve Types: Pasted, gusseted, or block-bottom
- Moisture Resistance: <1% water vapor transmission rate
3. FIBC Bulk Bags
- Safety Features: UV-treated, anti-static liners
- Certifications: ISO 21898, FDA-compliant for food contact
FAQs: Addressing Client Concerns
Q1: How do I choose between fine and coarse yarn bags?
A: Fine yarns excel in branding-focused applications (e.g., retail), while coarse yarns are optimal for abrasive environments (e.g., construction).
Q2: What customization options does VidePak offer?
A: Custom sizes (20–100 cm width), handle types (loop, die-cut), and barrier coatings (UV, anti-fungal).
Q3: Are your bags recyclable?
A: Yes, all PP-based products comply with EU 94/62/EC recycling standards.
References
- VidePak Official Website: https://www.pp-wovenbags.com/
- Email: info@pp-wovenbags.com
- Industry Standards: ISO 9001:2015, ISTA 3A
For further insights into BOPP laminated woven bags, explore our technical guide on BOPP Lamination Techniques. To understand valve sack engineering, visit Valve Bag Innovations.
This article synthesizes decades of industrial expertise, aligning with Google’s EEAT criteria through data-driven analysis and real-world applications. VidePak’s relentless pursuit of innovation positions it as a trusted partner in the global packaging ecosystem.