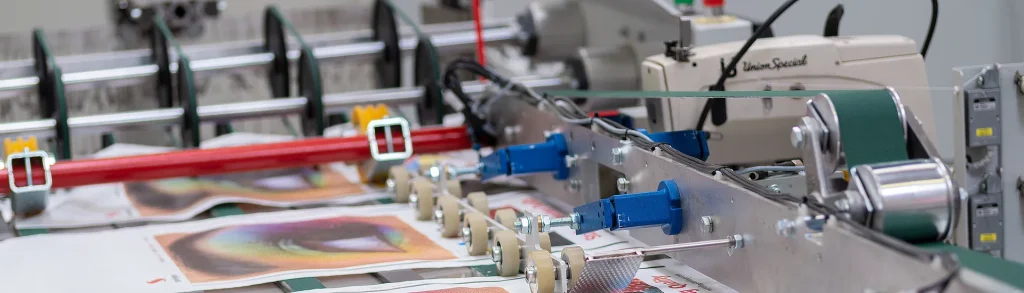
In the construction industry, where durability, cost-efficiency, and adaptability are non-negotiable, woven polypropylene (PP) packaging bags stand as a cornerstone for material handling. With over 30 years of industry expertise, VidePak has emerged as a global leader in manufacturing high-performance woven bags, serving clients across construction, agriculture, and food processing sectors. Our research reveals that selecting the right woven bag can reduce material loss by 15–20%, lower logistics costs by 10–12%, and enhance brand visibility through customized printing solutions. For instance, a construction firm in Germany reduced cement spillage by 18% after switching to VidePak’s laminated BOPP woven bags with reinforced seams.
1. The Role of Woven Bags in Construction: Beyond Basic Packaging
Woven PP bags are engineered to withstand extreme conditions, from heavy loads to outdoor storage. Key advantages include:
- High Tensile Strength: Bags with a 90–120 g/m² fabric density can hold up to 50 kg of cement or sand without tearing.
- UV Resistance: Laminated BOPP layers protect contents from sunlight degradation, critical for chemicals stored on construction sites.
- Moisture Barrier: Inner polyethylene (PE) liners prevent moisture ingress, preserving materials like gypsum or adhesives.
VidePak’s Austrian Starlinger machinery ensures precision in weaving and lamination, enabling production capacities of 8 million bags monthly. Our BOPP laminated woven bags, for example, combine a 90 g/m² PP fabric with a 20-micron BOPP layer, achieving a burst strength of 35 kPa—ideal for abrasive materials like gravel.
2. Tailoring Solutions for Food and Agricultural Products
While construction demands robustness, food-grade applications require stringent safety and compliance. Below is a comparative analysis of requirements across sectors:
Product Type | Key Requirements | Recommended Bag Specifications |
---|---|---|
Flour | – FDA/ISO 22000 certification | 80–100 g/m² PP fabric, PE inner liner |
– Anti-static properties to prevent dust | 4-color flexo printing for branding | |
Sugar | – Moisture resistance (≤0.5% permeability) | Laminated BOPP layer (15–20 microns) |
– Smooth surface for easy cleaning | Valve design for automated filling | |
Spices | – Aroma retention | Aluminum foil laminated layers |
– Lightweight (60–80 g/m²) | ZIP closure for resealability | |
Crop Powders | – UV protection for outdoor storage | 120 g/m² fabric, UV-stabilized additives |
– High breathability to prevent condensation | Mesh panels for ventilation |
For instance, a spice exporter in India reduced waste by 22% using VidePak’s aluminum foil-lined woven bags, which block oxygen and light while maintaining aroma integrity.
3. Critical Parameters for Optimal Selection
A. Fabric Weight and Thickness
- 50–80 g/m²: Suitable for lightweight products like flour or additives.
- 100–150 g/m²: Ideal for construction materials (e.g., cement, sand).
VidePak’s customizable valve bags with 100 g/m² fabric and 18-micron BOPP lamination are widely used for powdered concrete additives, offering a 30% faster filling speed compared to traditional open-mouth designs.
B. Lamination and Liners
- BOPP Lamination: Enhances printability and UV resistance. A 20-micron layer increases durability by 40%.
- PE Liners: Provide moisture barriers, critical for hygroscopic materials like fertilizers.
C. Printing and Branding
VidePak’s 8-color rotary printing machines achieve 150-line/inch resolution, enabling photorealistic designs. A construction materials supplier in Brazil reported a 25% increase in customer engagement after adopting full-color printed FIBC bags.
4. FAQs: Addressing Client Concerns
Q1: Are VidePak’s bags compliant with food safety standards?
Yes. Our FDA-certified BOPP laminated bags meet ISO 22000 and EU Regulation 10/2011 for direct food contact.
Q2: What is the minimum order quantity (MOQ)?
MOQ starts at 10,000 bags, with discounts for orders exceeding 100,000 units.
Q3: How do I choose between sewn and heat-sealed closures?
- Sewn closures: Cost-effective for non-hygroscopic materials.
- Heat-sealed closures: Superior moisture protection for chemicals or food.
5. VidePak’s Commitment to Excellence
Founded in 2008, VidePak leverages 30+ years of industry expertise under CEO Ray’s leadership. With 568 employees and a global footprint spanning Europe, Asia, and Africa, we operate:
- 100+ circular looms for high-speed weaving.
- 30 lamination machines for BOPP/PE coatings.
- 16 extrusion lines producing virgin PP granules.
Our $80 million annual revenue reflects trust from clients like Henkel Adhesive Technologies, who praise our “consistent quality and on-time delivery”.
References
- VidePak Official Website: PP Woven Bags
- Industry Insights: BOPP Laminated Woven Bags
- Contact: info@pp-wovenbags.com
By integrating technical precision with market-driven innovation, VidePak remains at the forefront of woven packaging solutions, empowering industries to achieve efficiency, sustainability, and brand excellence.