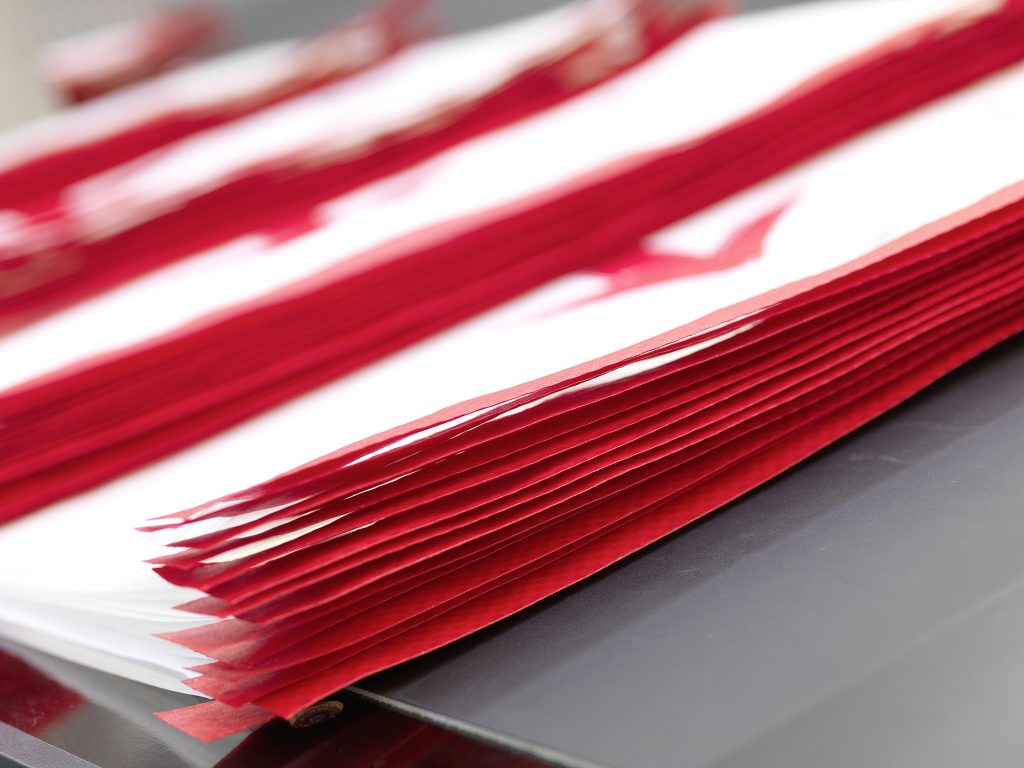
- Applications Across Food and Agricultural Industries
- Key Technical Parameters of Industrial Woven Bags
- Choosing the Right Packaging Solution
- Quality Assurance and Global Standards
- Sustainability Trends in Industrial Packaging
- Frequently Asked Questions (FAQs)
- Practical Examples from the Industry
- Conclusion
Industrial woven packaging bags are the cornerstone of safe, efficient, and sustainable solutions for food-grade materials like flour, sugar, spices, and agricultural products. By leveraging their durability, moisture resistance, and customizable features, these bags meet the rigorous demands of food safety standards and evolving global sustainability goals.
Applications Across Food and Agricultural Industries
1. Tailored Solutions for Specific Products
Industrial woven packaging bags cater to diverse food and agricultural materials, ensuring optimal storage and transportation:
- Flour and Sugar: Requires moisture-resistant inner linings and reinforced stitching to withstand heavy weights and stackability.
- Spices and Seasonings: UV protection and airtight seals to maintain freshness, with high-resolution multi-color printing for branding.
- Agricultural Powders and Food Additives: High tear resistance and anti-static properties to handle fine powders effectively.
Product Type | Key Requirements |
---|---|
Flour and Sugar | Inner liners for moisture resistance, robust stitching for durability |
Spices and Seasonings | UV stabilization, odor barriers, attractive printed designs |
Agricultural Powders | Anti-static properties, high tear resistance, customizable sizes |
Food Additives | Food-grade material certifications, odor-proof linings |
Key Technical Parameters of Industrial Woven Bags
Parameter | Optimal Range | Purpose |
---|---|---|
Thickness | 100–250 GSM | Ensures strength while optimizing material usage |
Bag Weight Capacity | 10–50 kg | Accommodates typical food-grade batch sizes |
UV Resistance | 1–3% additive content | Protects contents from prolonged sun exposure |
Printing Capability | Up to 8 colors | Enables branding and regulatory compliance |
Liner Options | PE or aluminum foil | Enhances barrier properties against moisture and odor |
Cost vs. Functionality
While advanced features like UV resistance and multi-layer coatings add to the cost, bulk production minimizes unit expenses, making premium features accessible.
Choosing the Right Packaging Solution
1. Understanding Specific Needs
- Humidity Sensitivity: Laminated or lined bags are critical for flour and sugar to prevent clumping.
- UV Exposure: Spices often require UV-stabilized bags for extended shelf life under direct sunlight.
- Product Weight: Agricultural powders necessitate high tensile strength to prevent ruptures during transport.
2. Functional Customizations
- Bag Closures: Open-top for easy filling, spout tops for precise dispensing, and valve tops for secure sealing.
- External Coatings: Laminated exteriors provide enhanced durability, aesthetics, and resistance to environmental factors.
- Printing: Eco-friendly inks align with sustainability goals and ensure vibrant, long-lasting designs.
Quality Assurance and Global Standards
Global Certifications
VidePak’s industrial woven bags adhere to stringent international guidelines, including:
- ISO 22000: Ensures food safety management.
- FDA and EU Compliance: Verifies the use of food-grade materials.
- REACH Standards: Certifies chemical safety in materials used.
- ASTM Protocols: Validates physical durability and reliability.
- HACCP: Guarantees contamination-free manufacturing processes.
Strict quality control at every stage—from raw material selection to final production—ensures consistency, durability, and compliance with global norms.
Sustainability Trends in Industrial Packaging
1. Recyclable and Biodegradable Materials
Woven polypropylene bags are increasingly recyclable, reducing landfill waste. Recent innovations include biodegradable additives, offering an eco-friendly alternative for industries aiming for net-zero emissions.
2. Advanced Manufacturing Technologies
Technologies like ultrasonic sealing and gusseted designs reduce material waste while enhancing bag functionality. These innovations balance sustainability with performance.
3. Lightweight, High-Performance Materials
Advances in polymer engineering allow thinner, more robust bags, reducing raw material usage and transportation costs.
Frequently Asked Questions (FAQs)
Q1: How do UV-resistant woven bags improve product longevity?
UV-resistant bags protect contents from degradation caused by sunlight, extending shelf life, especially for spices and additives stored in outdoor conditions.
Q2: Can industrial woven bags meet food safety requirements?
Yes, VidePak’s bags comply with ISO 22000, FDA, and HACCP standards, ensuring they are safe for direct food contact.
Q3: Are these bags compatible with automated filling systems?
Yes, the bags are designed for seamless integration with modern filling, stacking, and sealing equipment, enhancing operational efficiency.
Q4: What makes laminated bags ideal for flour and sugar?
Laminated bags offer superior moisture resistance, preventing product clumping and spoilage during storage and transport.
Q5: How can I ensure cost-efficiency while customizing bags?
Bulk orders and standardized bag sizes help reduce costs while maintaining the required features like UV stabilization and inner liners.
Practical Examples from the Industry
1. Sugar Industry
VidePak’s moisture-proof laminated bags have improved shelf stability for sugar, reducing wastage by 20% in humid regions.
2. Spice Export
UV-resistant woven bags have reduced spoilage during spice exports, especially in regions with prolonged sun exposure, enhancing profit margins by 15%.
3. Food Additives
Anti-static woven bags used for powdered food additives ensure safe and efficient storage, meeting global regulatory requirements.
- Discover details: Kraft Paper Bags Laminated with Woven Fabric: The Intersection of Technological Advancement and Cost Efficiency
Conclusion
Industrial woven packaging bags are indispensable for industries requiring durable, customizable, and sustainable packaging solutions. Whether for flour, spices, or agricultural products, these bags deliver unmatched performance while adhering to international safety and sustainability standards. VidePak continues to lead with innovations that balance functionality, cost-efficiency, and environmental responsibility, making it a trusted partner in the global packaging landscape.