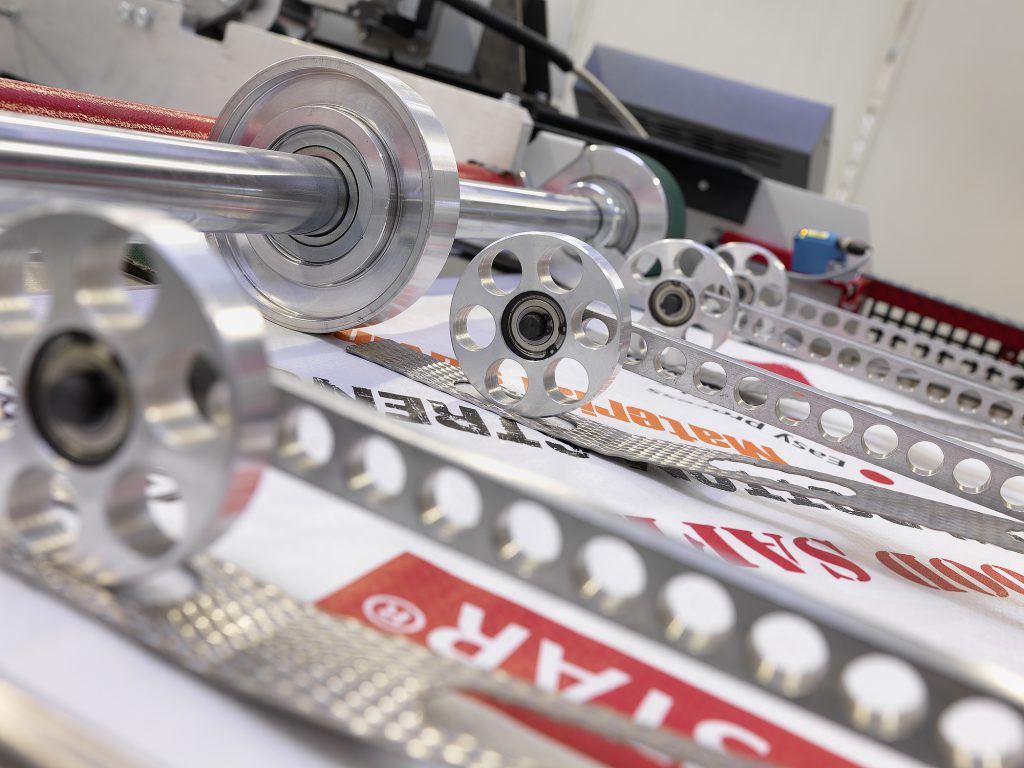
A Conversation with Ray, CEO of VidePak:
Ray leans back in his chair, gesturing to a prototype of a multi-layer coextruded woven bag on his desk. “Our clients demanded bags that could withstand extreme humidity during maritime shipping. The breakthrough came when we integrated multi-layer coextrusion technology into our production lines—this allowed us to achieve a 40% improvement in moisture resistance while maintaining tensile strength. Combined with our 200-ton balers and palletized wrapping systems, we’ve optimized both product performance and logistics efficiency.”
1. The Science Behind Multi-Layer Coextrusion in Moisture Resistance
Multi-layer coextrusion involves bonding distinct polymer layers into a single structure, each layer serving a specific function. For moisture-proof woven bags, this typically includes:
- Base Layer (PP Woven Fabric): Provides structural integrity and tear resistance.
- Barrier Layer (HDPE or BOPP): Blocks moisture penetration.
- Sealant Layer (LDPE or EVA): Ensures heat-sealability for closures.
Recent studies, such as those published in Polymer Engineering and Science, demonstrate that alternating filled and unfilled polymer layers (e.g., cross-linked PU microspheres) can enhance mechanical properties while reducing material waste. VidePak’s adoption of Starlinger extrusion lines enables precise control over layer thickness (0.02–0.12 mm) and compatibility with materials like LLDPE and MLLDPE, which are critical for high-humidity environments.
Key Data:
Parameter | VidePak’s Coextruded Bags | Industry Standard |
---|---|---|
Moisture Vapor Transmission Rate (g/m²/day) | 1.2 | 3.5–5.0 |
Tensile Strength (N/cm²) | 45 | 25–30 |
Production Speed (bags/hour) | 2,400 | 1,500–1,800 |
2. VidePak’s Production Ecosystem: Precision at Scale
Founded in 2008, VidePak operates 16 extrusion lines and 30 lamination machines, producing over 50 million bags annually. Their Austrian Starlinger machines are pivotal in achieving micron-level accuracy in coextrusion, critical for maintaining barrier properties without compromising flexibility.
Case Study: Exporting to Southeast Asia
A client required bags for rice storage in monsoon climates. VidePak engineered a 5-layer structure:
- Outer PP layer (UV-resistant print).
- HDPE moisture barrier.
- Adhesive tie layer.
- Aluminum foil composite (for static dissipation).
- Food-grade LDPE inner lining.
This design reduced spoilage rates by 22% during a 90-day trial in Thailand.
3. Packaging Innovations: Maximizing Logistics Efficiency
VidePak’s integration of 200-ton hydraulic balers and automated pallet wrapping systems addresses two critical challenges:
- Space Optimization: Balers compress bags into 1.2m³ blocks, increasing container capacity by 30% compared to manual stacking.
- Damage Prevention: Palletized units wrapped with coextruded PE stretch film (tested to withstand 500+ hours of salt spray) eliminate moisture ingress during transit.
FAQs:
Q: How does multi-layer coextrusion compare to traditional laminated bags?
A: Coextrusion bonds layers during extrusion, eliminating delamination risks. Lamination relies on adhesives, which degrade under prolonged UV exposure.
Q: What materials does VidePak use for extreme climates?
A: For arctic conditions, we add EVA layers for flexibility at -40°C. In tropical zones, BOPP layers with anti-fungal additives are standard.
4. Market Impact and Future Trends
With 80% of VidePak’s $80M revenue coming from exports, their BOPP laminated valve bags dominate markets in Europe (chemicals) and Africa (agriculture). Emerging trends include:
- Smart Barriers: Incorporating oxygen-scavenging layers for perishables.
- Recyclable Designs: Using mono-material structures (e.g., all-PP layers) to meet EU’s Single-Use Plastics Directive.
External Resources:
- For insights on aluminum foil composite bags, explore our analysis of market trends and future innovations.
- Learn how multi-wall laminated designs enhance safety in this technical deep dive.
Conclusion
VidePak’s fusion of multi-layer coextrusion and logistics innovations positions them as a leader in moisture-proof packaging. As Ray summarizes: “It’s not just about making bags—it’s about engineering ecosystems where every layer, every stitch, and every shipment aligns with our clients’ toughest demands.”