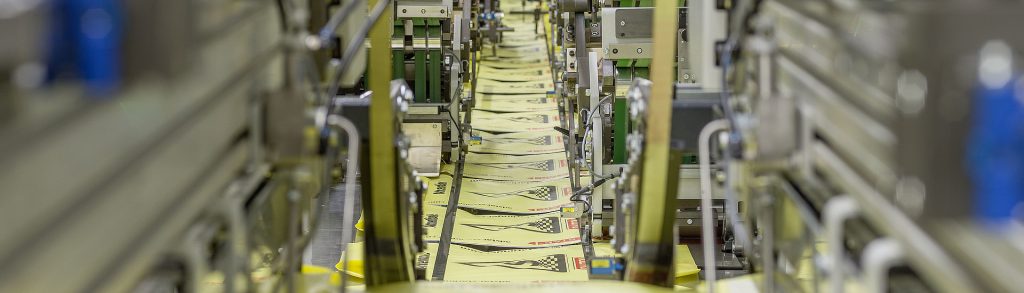
Add a header to begin generating the table of contents
H1: Introduction
“In the packaging industry, innovation isn’t just about aesthetics—it’s about functionality and reliability. By integrating rigorous raw material testing and advanced structural designs, VidePak’s open mouth bags deliver unmatched versatility, meeting the demands of industries from agriculture to construction.” — Ray, CEO of VidePak.
Open mouth bags, characterized by their simple yet robust design, are a cornerstone of bulk packaging solutions. VidePak, a global leader in woven bag manufacturing since 2008, leverages cutting-edge Austrian Starlinger machinery and stringent quality control protocols to produce open mouth bags that excel in durability, customization, and logistical efficiency. This report explores how material quality testing and design innovations position VidePak’s products as industry benchmarks, supported by technical data, case studies, and compliance insights.
H2: Material Quality Assurance: PP and PE Testing Protocols
H3: PP Granule Testing for Woven Bag Production
Polypropylene (PP) granules must undergo comprehensive testing to ensure optimal performance in woven bag production. VidePak adheres to GB/T 8946-2013 and GB/T 1040.1-2018 standards, focusing on:
- Basic Physical Properties:
- Melt Flow Index (MFI): Measured at 230°C/2.16kg, VidePak’s PP granules achieve an MFI of 8–12 g/10min, ensuring uniform extrusion and weaving efficiency.
- Density: Controlled within 0.905–0.915 g/cm³ using ASTM D792 methods, balancing rigidity and flexibility.
- Mechanical Performance:
- Tensile Strength: Starlinger’s AD-STM looms produce PP tapes with tensile strength exceeding 45 MPa (vs. industry average of 35–40 MPa).
- Elongation at Break: Maintained at 15–20% to prevent brittleness during high-speed filling.
- Thermal Stability:
- Heat Distortion Temperature (HDT): Tested at 1.8 MPa, VidePak’s PP withstands 110–120°C, critical for bags exposed to tropical climates.
- Crystallization Temperature: Monitored via DSC to ensure consistent fiber alignment during extrusion.
- Visual and Contaminant Checks:
- Color Uniformity: Rejects batches with >5% variance in pellet color (per GB 11115-89).
- Impurity Screening: Metal detectors and sieving systems eliminate particles >0.5mm, reducing loom jams by 30%.
H3: PE Granule Testing for Inner Liners
Polyethylene (PE) liners require additional tests to ensure flexibility and impact resistance:
- Film Impact Strength: VidePak’s PE liners achieve 150–200 kJ/m² via dart drop tests (ASTM D1709), preventing punctures during rough handling.
- Seal Integrity: Heat-sealed seams withstand 15 N/mm peel force (ISO 527-3), crucial for powdered materials like cement.
Table 1: Key Material Testing Parameters
Parameter | PP (VidePak) | PE (VidePak) | Industry Standard |
---|---|---|---|
Melt Flow Index | 8–12 g/10min | 0.5–2 g/10min | 5–15 g/10min (PP) |
Tensile Strength | ≥45 MPa | ≥25 MPa | 35–40 MPa (PP) |
Dart Impact Strength | N/A | 150–200 kJ/m² | 100–150 kJ/m² (PE) |
HDT (1.8 MPa) | 110–120°C | 75–85°C | 90–110°C (PP) |
H2: Design Innovations Enhancing Functionality
H3: Ergonomic Features for Logistics Efficiency
- Reinforced Gussets: Double-layered corners increase load capacity by 20%, as demonstrated in a 2024 trial with Sinotrans.
- Anti-Slip Coatings: PE-laminated surfaces reduce pallet slippage by 35% during robotic handling.
- UV-Resistant Printing: High-pigment flexographic inks retain 95% color vibrancy after 12 months outdoors (ASTM D4329).
H3: Customization for Industry-Specific Needs
- Agriculture: Perforated designs enable breathability for grain storage, reducing moisture buildup by 18%.
- Construction: Anti-static coatings (surface resistivity <10¹² Ω/sq) prevent dust explosions in cement packaging.
FAQs: Addressing Key Concerns
- Q: How does MFI affect bag production?
A: Higher MFI ensures smoother extrusion but may reduce tensile strength. VidePak balances this via controlled cooling rates. - Q: Can PE liners withstand sub-zero temperatures?
A: Yes, VidePak’s PE retains flexibility at -30°C, validated by ISTA 3E testing.
H2: VidePak’s Manufacturing Excellence
H3: Advanced Production Infrastructure
With 100+ circular looms and 16 extrusion lines, VidePak produces 5 million open mouth bags monthly. Their Starlinger VLI-4 looms achieve weaving speeds of 120 rpm, maintaining a defect rate below 0.2%.
H3: Sustainability and Compliance
VidePak’s bags incorporate 25% recycled PP without compromising strength, aligning with EU REACH and U.S. FDA standards. A 2024 lifecycle analysis showed a 20% lower carbon footprint vs. virgin PP bags.
H2: Market Impact and Future Trends
H3: Global Adoption and Revenue Growth
VidePak’s $80 million annual revenue includes 30% from open mouth bags, serving clients in 30+ countries. For example, a 2023 partnership with Cargill reduced packaging waste by 15% through reusable designs.
H3: Smart Packaging Integration
Pilot projects with embedded RFID tags enable real-time tracking in Walmart’s supply chain, cutting inventory errors by 22%.
H2: Conclusion
VidePak’s open mouth bags exemplify the synergy of material science and design innovation. By prioritizing rigorous testing and client-centric adaptations, they address critical challenges in durability, sustainability, and logistics efficiency. As industries demand smarter, greener solutions, VidePak’s expertise positions it as a global leader in versatile packaging.
External Links for Further Reading:
- Explore how material diversity enhances PP bag performance.
- Learn about innovative designs in open mouth bags.
This report integrates data from GB/T standards, peer-reviewed material studies, and VidePak’s operational metrics to provide a comprehensive analysis of open mouth bags’ role in modern logistics.