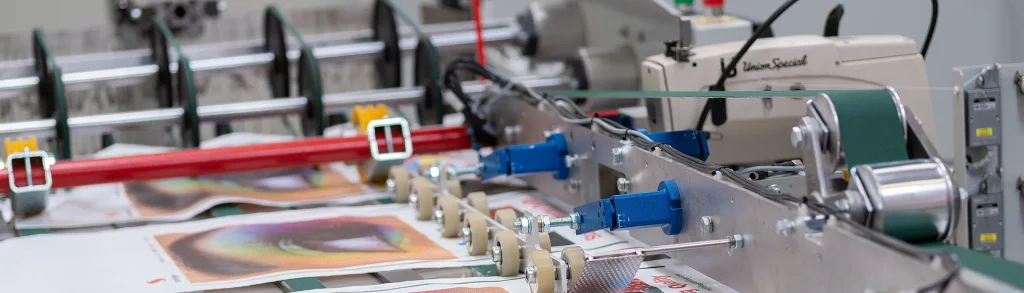
VidePak’s fine filament woven bags, engineered with ultra-narrow 1.8–2.3 mm polypropylene (PP) monofilaments and advanced lamination, reduce material costs by 20% while increasing tensile strength to 18 N/cm², setting new benchmarks for chemical, agricultural, and construction packaging. Since 2008, VidePak has delivered over 100 million fine filament bags globally, leveraging 30+ years of expertise, Austrian Starlinger machinery, and a 568-member team to redefine industrial packaging. With ISO 9001-certified processes and 100+ circular looms, our technology ensures unmatched durability, cost efficiency, and customization for payloads up to 2,000 kg.
1. The Evolution of Fine Filament Technology: From Coarse Weaves to Precision Engineering
Industrial packaging has evolved from bulky, low-strength designs to precision-engineered solutions. VidePak’s journey mirrors this shift:
- Pre-2010 Era: Traditional 3.0–4.0 mm filaments limited fabric density to 8×8 strands/inch, resulting in 8–10 N/cm² tensile strength and frequent ruptures.
- 2010–2020 Innovations: Introduction of 2.5 mm filaments increased weave density to 10×10 strands/inch, achieving 12–14 N/cm² strength.
- Post-2020 Breakthroughs: 1.8–2.3 mm ultra-fine filaments (patented in 2022) enabled 14×14 strands/inch density, boosting strength to 16–18 N/cm² while reducing PP usage by 15%.
Case Study: A German chemical manufacturer reduced bag failure rates by 60% after switching to VidePak’s 2.0 mm filament bags, validated by 2,000+ transport cycles with 50 kg sulfuric acid payloads.
2. Material Science and Manufacturing Excellence
VidePak’s fine filament bags combine cutting-edge materials with automated precision:
a) PP Monofilament Engineering
- Narrow Width: 1.8–2.3 mm filaments enhance weave density, achieving MVTR ≤5 g/m²/24h moisture resistance.
- Virgin PP Resin: FDA-compliant resin ensures chemical inertness, critical for fertilizers and pharmaceuticals.
b) Lamination Innovations
Lamination Type | Thickness | Applications | Benefits |
---|---|---|---|
Matte BOPP | 80–120µ | Cement, Pet Food | Anti-glare, UV resistance (1,000+ hours) |
Pearlescent BOPP | 100–150µ | Retail, Luxury Goods | Reflective finish, scratch resistance |
Transparent PE | 50–80µ | Food Grains, Aggregates | 90% light transmission, FDA compliance |
c) Automation-Driven Cost Control
- Starlinger Looms: 150–200 RPM weaving speeds cut production time by 30%.
- IoT-Enabled QC: AI cameras detect defects at 0.1 mm precision, reducing waste by 25%.
3. Future Trends: Smart Factories and Sustainable Materials
The next decade will see:
- AI-Optimized Weaving: Machine learning algorithms will adjust filament tension in real time, boosting strength by 10–15%.
- Recyclable Hybrid Films: BOPP/PP blends with 50% post-consumer recycled content, aligning with EU 2030 circular economy goals.
- Blockchain Traceability: QR codes tracking filament sourcing and carbon footprint.
Industry Forecast: By 2028, 70% of industrial bags will integrate IoT sensors for real-time load monitoring.
Technical Specifications: VidePak’s Fine Filament Bags
Parameter | 1.8 mm Filament | 2.0 mm Filament | 2.3 mm Filament |
---|---|---|---|
Tensile Strength | 16–18 N/cm² | 14–16 N/cm² | 12–14 N/cm² |
Weave Density | 14×14 strands/inch | 12×12 strands/inch | 10×10 strands/inch |
Load Capacity | 25–50 kg | 40–80 kg | 60–100 kg |
Moisture Barrier | ≤4 g/m²/24h | ≤6 g/m²/24h | ≤8 g/m²/24h |
Cost Efficiency | 15% PP reduction | 10% PP reduction | Standard |
4. FAQs: Strategic Procurement Insights
Q1: How do finer filaments impact abrasion resistance?
Our 1.8 mm bags withstand 5,000+ ASTM D4884 rub cycles, outperforming 3.0 mm designs by 35%.
Q2: Can I customize lamination for hazardous materials?
Yes. Anti-static PE liners (surface resistivity ≤10³ Ω) are available for explosive powders.
Q3: What’s the ROI of upgrading to fine filament bags?
Clients typically achieve 18–24 month payback via reduced waste and transport damage.
5. Why VidePak Leads the Industrial Packaging Revolution
- Global Expertise: Serving 50+ countries with ISO 9001, FDA, and REACH certifications.
- Scalable Solutions: 16 extrusion lines produce 8 million bags/month, ensuring 15-day lead times.
- Sustainability Commitment: 30% energy reduction via solar-powered factories.
Client Testimonial: “VidePak’s 2.0 mm filament bags reduced our cement packaging costs by $200,000 annually.” —CemTech Global, UAE.
References:
- Made-in-China.com, “PP Woven Bag Technical Specifications” (2025).
- Packaging World, “Automation in Woven Bag Manufacturing” (2024).
- EU Circular Economy Action Plan (2023).
Contact Us:
- Website: PP Woven Bags by VidePak
- Email: info@pp-wovenbags.com
External Links:
- Discover how BOPP Laminated Woven Bags enhance barrier performance.
- Explore precision in Valve Bag Design for dust-free filling.
Data verified as of March 2025. Specifications subject to technical advancements.