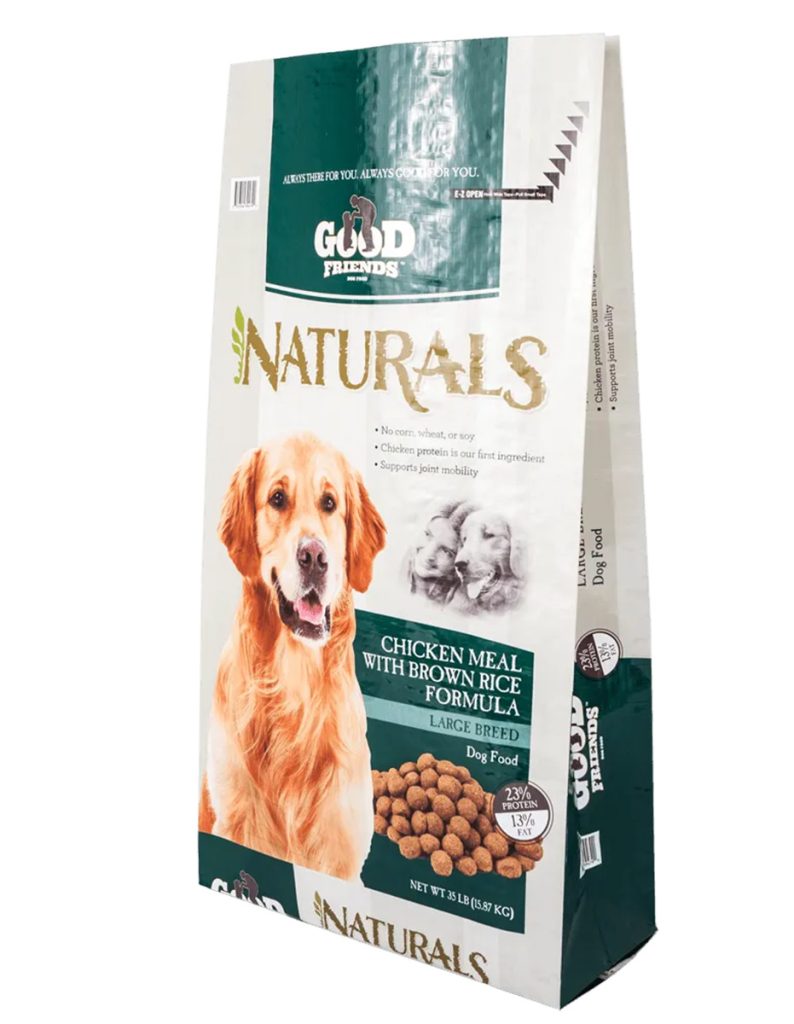
The production of Laminated Woven Bags has undergone significant advancements, largely driven by the adoption of the multi-layered co-extrusion blown film process. This cutting-edge technique, combined with high-precision equipment from Austrian Starlinger and German W&H, has revolutionized the industry, providing unmatched durability, flexibility, and efficiency in packaging solutions. Let us explore how these advancements have reshaped the landscape of Laminated Woven sacks and BOPP Woven Bags while highlighting the critical role of the drawing process in improving their performance.
The Multi-Layered Co-Extrusion Blown Film Process
The multi-layered co-extrusion blown film process is at the core of manufacturing high-quality Laminated Woven Bags. This process involves extruding multiple layers of molten plastic through a die, which are then inflated to form a thin film. The layers are fused to achieve optimal strength, moisture resistance, and aesthetic appeal. The benefits of this process include:
- Enhanced Durability: Multi-layered structures improve resistance to tearing and puncturing.
- Moisture Resistance: Laminations provide an effective barrier against moisture, preserving product integrity.
- Customizability: Multi-layer films support vivid and multi-color printing, meeting diverse branding needs.
- Eco-Friendly Solutions: Recyclable materials can be incorporated, contributing to sustainability.
This technology is particularly impactful in creating multi-wall woven bags and Laminated PP bags, offering exceptional protection for products ranging from chemicals to agricultural goods.
Explore more about Laminated Woven Bags and their manufacturing process
Superior Equipment: Starlinger and W&H
VidePak’s facilities utilize state-of-the-art machinery from Starlinger and W&H, known for their precision and efficiency. These systems feature:
- High Automation: Minimizing human intervention, reducing errors, and enhancing consistency.
- High-Speed Production: Achieving line speeds exceeding 200 bags per hour.
- Multi-Machine Integration: Seamless synchronization across extrusion, lamination, and printing units.
- Advanced Printing Capabilities: Supporting high-definition, multi-color designs for BOPP Woven Bags.
The superior performance of these machines enables VidePak to meet the global demand for high-quality Laminated Woven Bags, maintaining cost-efficiency while exceeding customer expectations.
The Role of Drawing in Bag Durability and Flexibility
Drawing, or stretching, is a critical step in the production of woven fabrics, directly influencing the durability and flexibility of Laminated PP bags. The process involves the following:
- Orientation of Polymer Chains: During drawing, polymer molecules are aligned, significantly enhancing tensile strength.
- Controlled Stretching: Precise control over the stretch ratio ensures uniformity and prevents weak points.
- Customization: Adjusting drawing parameters enables the production of fabrics with tailored flexibility and rigidity.
These improvements are particularly vital for applications such as multi-wall woven bags, where bags must endure rough handling and heavy loads without compromising on flexibility.
Table: Comparative Properties of Woven Bags with Different Drawing Ratios
Parameter | Low Stretch Ratio | Medium Stretch Ratio | High Stretch Ratio |
---|---|---|---|
Tensile Strength (MPa) | 25 | 35 | 45 |
Elongation at Break (%) | 40 | 25 | 15 |
Flexibility | High | Moderate | Low |
Suitable Applications | Lightweight Goods | General Packaging | Heavy-Duty Goods |
The enhanced durability and flexibility achieved through meticulous drawing are particularly significant for the production of Laminated PP bags and BOPP Woven Bags, ensuring they meet diverse market demands.
Learn more about the advancements in BOPP Woven Bags
Efficiency Through Automation
Automation has redefined production efficiency at VidePak. By leveraging advanced technologies:
- Consistency: Automated processes ensure uniform quality across batches.
- Reduced Waste: Precise material usage minimizes waste, enhancing sustainability.
- Faster Turnaround: Integrated systems accelerate production cycles, allowing quick fulfillment of large orders.
VidePak’s manufacturing capabilities include 150 circular looms, 16 extrusion lines, 32 lamination machines, and 16 printing machines. This robust infrastructure underscores our ability to produce high volumes of Laminated Woven Bags with consistent quality and rapid delivery timelines.
Applications of Laminated Woven Bags
The versatility of Laminated Woven Bags makes them indispensable across industries:
- Agriculture: Ideal for fertilizers and seeds due to their moisture resistance.
- Construction: Effective in packaging cement and sand with high durability.
- Food Packaging: Safe and hygienic solutions for grains and pet food.
- Retail: Eye-catching designs for branded products.
Sustainable Practices
VidePak remains committed to sustainability by incorporating recyclable materials into its production processes and minimizing energy consumption. Our advanced equipment from Starlinger and W&H ensures eco-friendly manufacturing without compromising on quality.
Conclusion
The integration of the multi-layered co-extrusion blown film process and cutting-edge equipment has transformed the production of Laminated Woven Bags, delivering unmatched durability, flexibility, and efficiency. VidePak continues to innovate, setting benchmarks in the industry for quality and sustainability. With our focus on advanced technologies and environmentally conscious practices, we remain at the forefront of the global packaging solutions market.