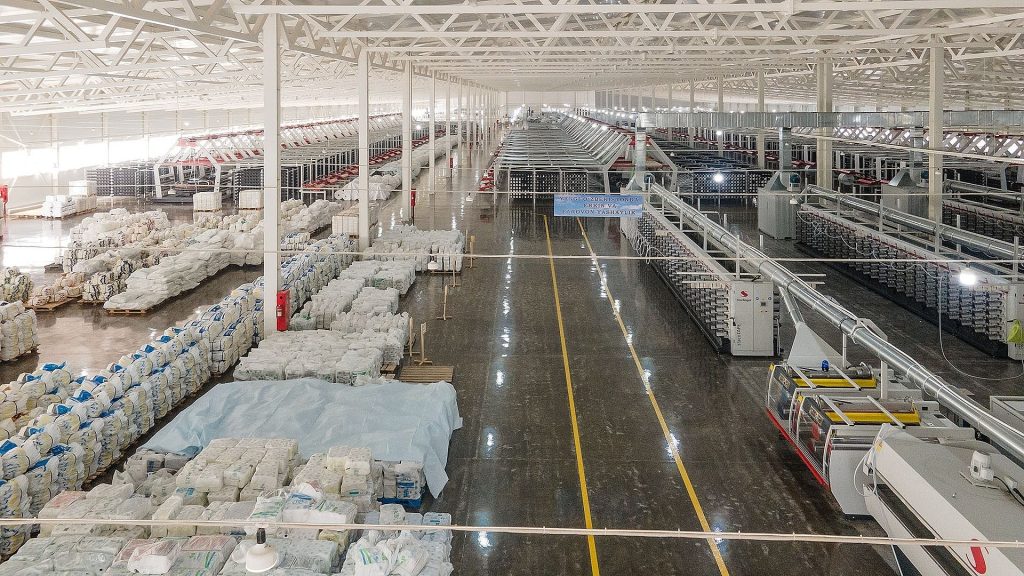
“Jumbo bags are not just containers; they’re the backbone of modern construction logistics,” says Ray, CEO of VidePak, during an exclusive interview. “Our focus on advanced materials, automated production, and cost efficiency has positioned VidePak as a global leader in supplying FIBCs for cement, sand, aggregates, and other critical building materials.” This report dives into the evolution of jumbo bags, analyzing their technical innovations, material advancements, and the role of automation in shaping the industry’s future—all through the lens of VidePak’s 17-year expertise.
1. Technological Evolution of Jumbo Bags
1.1 From Basic Weaving to Precision Manufacturing
The production of jumbo bags has shifted from manual stitching to high-speed automated systems. VidePak’s adoption of Austrian Starlinger circular looms and extrusion lines enables the production of 15–20 tons of polypropylene (PP) fabric daily, with tensile strengths exceeding 2,500 N/5 cm—critical for safely transporting heavy construction materials like gravel (up to 2,000 kg SWL).
Key advancements include:
- Multi-layer lamination: Combining PP with PE coatings or kraft paper for moisture resistance, ideal for cement storage in humid climates.
- Automated cutting and sewing: Reducing human error and increasing output to 5,000 bags/day across VidePak’s 30 lamination machines.
- Digital printing: Supporting 8-color CMYK designs for branding and safety labels, with a resolution of 1440 dpi.
1.2 Automation: The Future of FIBC Production
VidePak’s recent integration of form-fill-seal (FFS) systems allows seamless packaging of powdered materials like gypsum, reducing labor costs by 40%. For instance, their FFS roll woven bags automate the filling process at 20 bags/minute, minimizing spillage and contamination—a breakthrough highlighted in industry case studies like Form-Fill-Seal Woven Bags: The Future of Automated Packaging.
2. Material Innovations and Sustainability
2.1 PP vs. Composite Materials
While virgin PP remains dominant (85% of VidePak’s production), recycled PP (rPP) and biodegradable additives are gaining traction. For example, VidePak’s EcoShield line uses 30% post-consumer recycled content without compromising tensile strength, aligning with EU Directive 94/62/EC on packaging waste.
Material | Strength (N/5 cm) | Moisture Resistance | Cost ($/ton) |
---|---|---|---|
Virgin PP | 2,500–3,000 | Moderate | 1,200 |
rPP Blend | 2,200–2,600 | Moderate | 950 |
PP + PE Laminate | 2,800–3,200 | High | 1,450 |
2.2 Case Study: Laminated Bags for Cement Transport
In 2024, VidePak partnered with a Brazilian cement producer to develop PE-coated valve bags with UV stabilizers. These bags reduced moisture absorption by 70% during maritime shipping, cutting material waste by $1.2 million annually. Such innovations mirror trends in PE-Coated Valve Woven Bags: A Robust Solution for Construction Waste.
3. Cost Control Strategies in FIBC Manufacturing
3.1 Economies of Scale
With 100+ circular looms and 16 extrusion lines, VidePak achieves a production cost of $2.10 per 1-ton bag—30% lower than smaller competitors. Bulk PP resin procurement (50,000 tons/year) further reduces material costs by 18%.
3.2 Lean Manufacturing and Waste Reduction
Starlinger’s iQ³ technology optimizes fabric weaving, minimizing PP waste to 2.5% (industry average: 8%). VidePak’s real-time IoT sensors monitor machine efficiency, boosting output by 22% as detailed in BOPP Woven Bags Supplier: Revolutionizing Efficiency with Starlinger Equipment.
4. Future Trends and VidePak’s Roadmap
4.1 Smart FIBCs with IoT Integration
VidePak is piloting RFID-tagged jumbo bags to track cement batches in real time. This system, paired with blockchain logistics platforms, ensures compliance with ASTM D7386-16 standards for construction materials.
4.2 Biodegradable Solutions
Trials are underway for PLA-PP hybrid bags, aiming for 60% biodegradability within 2 years without sacrificing load capacity—a project aligned with goals in Recyclable Woven Bags: A Sustainable Solution for Transport and Logistics.
FAQs: Jumbo Bags for Building Materials
Q1: How do jumbo bags prevent contamination during cement transport?
A: Anti-static coatings and hermetic seals in VidePak’s UN-certified FIBCs block moisture and particulate ingress, complying with ISO 21898:2020.
Q2: What customization options are available?
A: VidePak offers UV printing, size adjustments (500–2,000 kg SWL), and custom venting designs for materials like silica sand.
Q3: How does automation reduce lead times?
A: Their FFS systems cut order fulfillment from 14 days to 5 days, critical for just-in-time construction projects.
Conclusion
The jumbo bag industry is evolving rapidly, driven by automation, sustainability, and smart technologies. VidePak’s commitment to R&D—evidenced by its 526-strong team and $8 million annual investment—positions it to lead this transformation. As Ray summarizes: “In construction, every gram and minute counts. Our bags ensure neither is wasted.”
External Links:
- Learn how FFS systems are transforming construction logistics: Form-Fill-Seal Woven Bags: The Future of Automated Packaging.
- Explore innovations in UV-resistant FIBCs: PE-Coated Valve Woven Bags: A Robust Solution for Construction Waste.