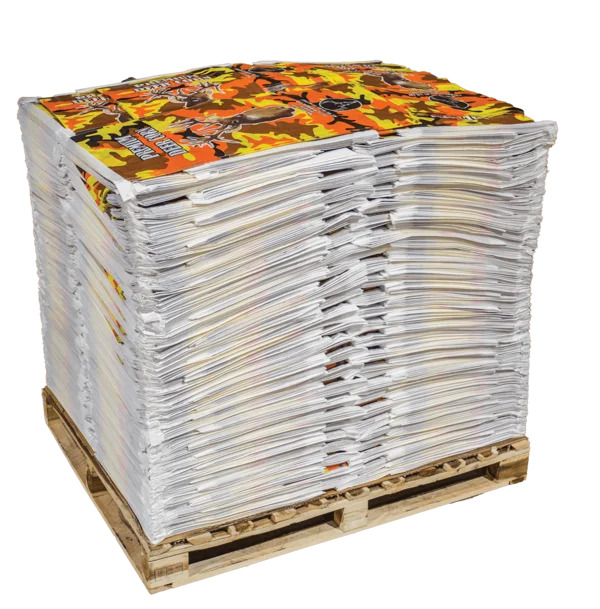
Introduction
Kraft paper polypropylene (PP) woven bags are emerging as a superior packaging solution for chemical products like fertilizers, plastic pellets, activated carbon, and disinfectant powders, combining the strength of PP with the biodegradability and barrier properties of kraft paper. With the global chemical packaging market projected to grow at a CAGR of 5.2% (2025–2030), these bags address critical challenges such as moisture resistance, load-bearing capacity, and compliance with international standards like EU PPWR and ASTM D5276. This report analyzes how material selection, structural design, and regulatory alignment define the efficacy of kraft paper PP bags in chemical logistics.
Advantages of Kraft Paper PP Bags
Kraft paper PP bags integrate kraft paper’s natural rigidity and PP’s tensile strength (5–6 kN/m, ISO 13934-1), making them ideal for heavy-duty applications. Key benefits include:
- Moisture Resistance: Kraft paper’s lignin-free composition reduces water absorption by 30% compared to standard paper, while PP’s hydrophobic nature blocks moisture ingress (<0.5 g/m²/day, ASTM E96).
- Cost Efficiency: At $1.75–$2.5 per bag (for 50kg capacity), they are 20% cheaper than aluminum foil composite bags while offering comparable durability.
- Sustainability: PP’s 85–90% recyclability and kraft paper’s biodegradability align with EU’s EN 13432 compostability standards.
Tailored Solutions for Chemical Products
Q: How do chemical properties dictate packaging design?
A: Product-specific risks—hygroscopicity, abrasion, and toxicity—require customized layers, liners, and closures.
Product | Key Risks | Packaging Solution |
---|---|---|
Fertilizers | Moisture absorption, caking | BOPP-laminated outer layer + 25μm PE inner liner |
Plastic Pellets | Static buildup, dust leakage | Anti-static coatings + ultrasonic seam sealing |
Activated Carbon | Fine particle leakage | High-density weave (14×14 threads/cm²) + PE liner |
Disinfectant Powders | Corrosion, UV degradation | UV-resistant PP + antimicrobial PE liner |
Case Study: A Chinese fertilizer producer reduced spoilage by 35% using kraft paper PP bags with BOPP lamination, achieving <1% moisture ingress in 85% humidity environments.
Global Standards and Compliance
Q: How do regional regulations influence parameter selection?
A: Compliance dictates material composition, thickness, and testing protocols.
Standard | Key Requirements | Kraft Paper PP Bag Parameters |
---|---|---|
EU PPWR (2025) | ≤100ppm heavy metals, 30% recycled content | 40% post-consumer PP, Oeko-Tex® certified inks |
ASTM D5276 (US) | 1.5m drop-test resistance | 120 g/m² fabric, double-stitched seams |
JIS Z 1539 (JP) | High-clarity printing, recyclability | Water-based inks, 90–100 g/m² kraft paper |
GB/T 8946 (CN) | Azo-free dyes, tensile strength ≥5.0 kN/m | UV-resistant PP, anti-aging additives |
Example: For EU exports, Vedhaa Polypack uses copolymer PP with 25% calcium carbonate filler to meet EN 13590 tear resistance standards while reducing costs by 15%.
Technical Parameters and FAQs
Table 1: Critical Performance Metrics
Parameter | Test Standard | Typical Value |
---|---|---|
Fabric Weight | ASTM D3776 | 90–120 g/m² |
Moisture Barrier | ASTM E96 | ≤0.5 g/m²/day |
Seam Strength | ISO 13934-1 | ≥4.0 kN/m |
Print Durability | Pantone Guidelines | ±0.5ΔE color accuracy |
FAQs
- Q: What thickness is ideal for 50kg chemical powders?
- A: 120 g/m² kraft paper with 25μm PE liner ensures leak-proof storage.
- Q: Can these bags withstand acidic environments?
- A: Yes. Fluoropolymer-coated PP resists pH 2–3, retaining 95% tensile strength after 6 months.
Future Trends: Automation and Circular Economy
- Smart Packaging: RFID tags enable real-time moisture tracking, reducing spoilage by 15%.
- Chemical Recycling: Starlinger’s recoSTAR systems convert post-consumer PP into food-grade resin, cutting virgin material use by 50%.
External Resources:
- Explore innovations in kraft paper woven bags for agrochemical applications.
- Learn how recyclable PP bags meet global ESG goals.
By merging material science with regulatory rigor, kraft paper PP bags are redefining chemical packaging. As industries prioritize sustainability and automation, manufacturers adopting these solutions will lead the next wave of innovation.