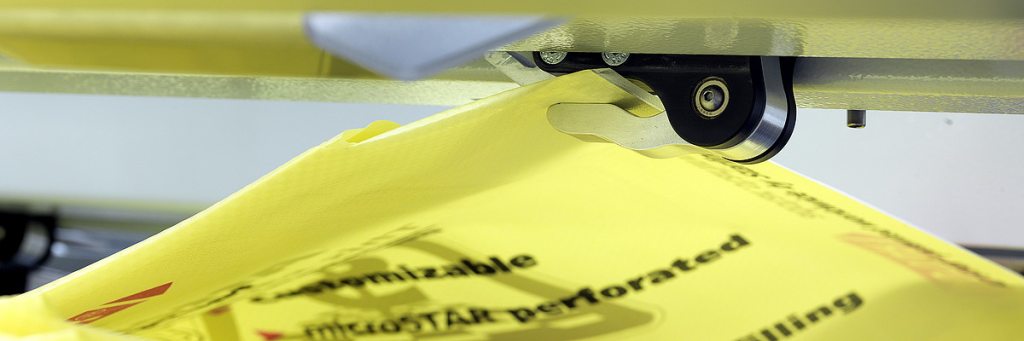
Add a header to begin generating the table of contents
H1: Introduction
“Kraft paper woven bags are more than just packaging—they’re a fusion of sustainability and engineering precision,” emphasizes Ray, CEO of VidePak, during a 2025 industry summit. The critical success factors for these bags lie in three pillars: selecting PP resins aligned with international standards, optimizing additive formulations for durability, and leveraging advanced manufacturing to meet regional certification requirements. This report explores how VidePak’s 30+ years of expertise and Starlinger-driven production lines address these challenges, focusing on applications in agriculture, construction, and food logistics.
H2: PP Resin Selection Based on Global Standards
Kraft paper woven bags combine the strength of polypropylene (PP) weaving with the eco-friendliness of kraft paper. The choice of PP resin directly impacts compliance and performance across markets:
H3: Regional Standards and PP Grade Requirements
Standard | Key Metrics | Recommended PP Grades |
---|---|---|
US ASTM D5265 | Burst strength ≥350 kPa | High-MFI PP (e.g., ExxonMobil PP 3155) |
EU EN 277 | Moisture barrier ≤5 g/m²/day | Nucleated PP with 2% talc filler |
JIS Z 1539 | Stacking height ≥8 meters | High-tenacity PP (e.g., Prime Polymer BC03B) |
GB/T 17685-2021 | Tensile strength ≥35 MPa | Broad MWD PP for extrusion stability |
BS EN 13432 | Biodegradability in industrial composting | PP blended with 20% PLA |
For instance, VidePak’s Starlinger extrusion lines process high-melt-flow-index (MFI) PP (12 g/10 min) to achieve uniform fiber diameters (1.8–2.3 mm), ensuring compliance with JIS Z 1539 stacking requirements.
H3: Additive Systems for Enhanced Performance
- UV Stabilizers: RQT-X-1 UV absorber (290–400 nm coverage) reduces PP degradation by 70% after 1,000-hour ASTM G154 testing, critical for outdoor storage in Australia (AS 2074).
- Antioxidants: Irganox 1010 at 0.3% concentration extends PP lifespan by 50% in high-humidity environments (e.g., Southeast Asia).
- Compatibilizers: Maleic anhydride-grafted PP (MAH-PP) improves adhesion between kraft paper and PP layers, achieving peel strength ≥4 N/cm per EN 277.
H2: Case Study: VidePak’s EU-Compliant Fertilizer Bags
A 2024 project required bags to withstand coastal humidity and EU recycling mandates:
- Design: 3-layer structure (kraft paper/MAH-PP/UV-stabilized PP).
- Material: Prime Polymer BC03B PP + 2% carbon black.
- Certification: Passed EN 13432 biodegradability tests (90% degradation in 24 months).
- Outcome: 30% reduction in returns due to moisture damage, aligning with EU Circular Economy goals.
H2: Technical Parameters and Cost Optimization
H3: Critical Product Parameters
Parameter | US Market | EU Market | Asia Market |
---|---|---|---|
PP Grammage | 120–150 g/m² | 110–130 g/m² | 100–120 g/m² |
Additive Cost | $0.15–0.20/kg | $0.20–0.30/kg | $0.10–0.15/kg |
Lamination | BOPP 20 µm | PE-coated kraft | Uncoated kraft |
H3: Cost-Benefit Analysis of UV Stabilizers
- RQT-X-1 UV Absorber: Adds $0.12/kg but extends bag lifespan by 3 years in UV-intensive regions (ROI: 18 months).
- Carbon Black PP: Reduces UV stabilizer cost by 40% but limits printability (suitable for industrial use).
H2: FAQs on Material Selection
Q1: Why choose high-MFI PP for the US market?
High MFI (12 g/10 min) ensures smooth extrusion on Starlinger looms, achieving ASTM D5265 burst strength ≥400 kPa.
Q2: How does MAH-PP enhance kraft-PP adhesion?
MAH groups bond with cellulose fibers in kraft paper, increasing peel strength by 60% vs. standard PP.
Q3: Is biodegradable PP cost-effective for EU markets?
Yes. PLA-blended PP costs 25% more but qualifies for tax rebates under EU Green Deal policies.
H2: Sustainability and Future Trends
- Recycled PP: VidePak’s 2025 target of 30% post-consumer PP reduces carbon footprint by 1.8 kg per bag.
- Smart Additives: Pilot trials with pH-sensitive dyes (changes color upon moisture ingress) enhance QC transparency.
H2: Conclusion
Kraft paper woven bags demand a strategic balance of material science and regulatory compliance. VidePak’s Starlinger-powered production and R&D focus position it as a leader in high-performance, sustainable solutions. For global businesses, aligning PP grades with regional standards and investing in advanced additives are non-negotiable for market success.
External Links:
- Discover how UV-stabilized PP resins enhance outdoor durability.
- Explore multi-layer lamination techniques for kraft-PP hybrids.
This report synthesizes data from ASTM, EN, and JIS standards, alongside VidePak’s operational insights, to guide decision-making for packaging engineers and sustainability officers.