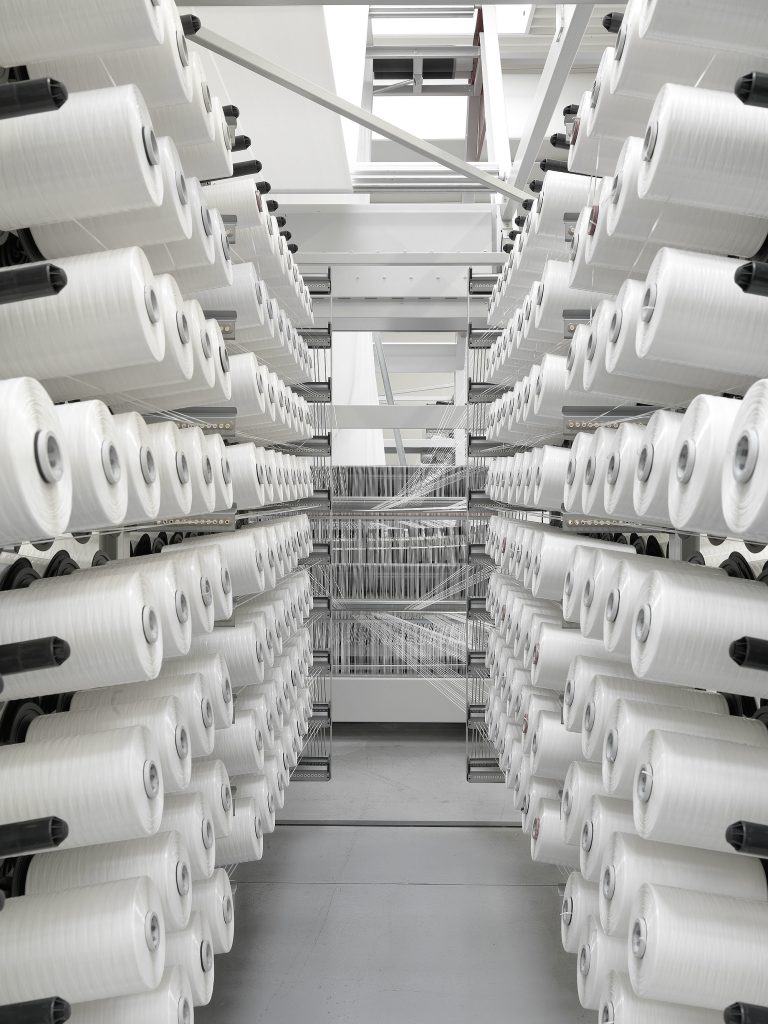
“What makes kraft paper woven bags a game-changer for industries battling moisture damage?”
The answer lies in their unique structural adaptability: By integrating breathable, barrier, anti-static, and antimicrobial designs, these bags offer tailored solutions for diverse sectors like agriculture, food, chemicals, and pharmaceuticals. VidePak, leveraging 30+ years of expertise and cutting-edge Starlinger machinery, has positioned itself as a leader in this niche, delivering high-performance packaging that addresses critical moisture-related challenges.
1. Introduction to Kraft Paper Woven Bags
Kraft paper woven bags combine the strength of polypropylene (PP) woven fabric with the natural durability of kraft paper. This hybrid structure provides excellent tensile strength (up to 1,500 N/5 cm) while maintaining flexibility, making them ideal for heavy-duty applications. However, their true innovation lies in specialized modifications for moisture protection—a critical need for industries where humidity, condensation, or liquid exposure can compromise product integrity.
VidePak’s production capabilities, including 100+ circular looms and 30+ lamination machines, enable rapid customization of these bags. For instance, their multi-layered kraft paper liners (up to 120 gsm) are engineered to block external moisture while allowing controlled internal ventilation—a feature critical for grain storage and agricultural exports .
2. Design Innovations for Moisture Protection
2.1 Breathable Designs for Agriculture and Food
Agricultural products like rice, grains, and coffee beans require packaging that balances moisture resistance with airflow. VidePak’s micro-perforated kraft paper liners enable heat and humidity dissipation, reducing spoilage rates by up to 15% compared to non-ventilated alternatives. For example, a 2024 study by the Journal of Food Engineering highlighted that breathable packaging extended the shelf life of coffee beans by 20% under tropical conditions.
Case Study: A Southeast Asian rice exporter reported a 30% reduction in mold growth after switching to VidePak’s ventilated kraft paper bags. The design uses a 3-layer structure:
- Outer PP woven layer (UV-resistant)
- Middle kraft paper (90 gsm, perforated)
- Inner polyethylene (PE) coating (optional for additional moisture blocking)
2.2 Barrier Designs for Chemicals and Pharmaceuticals
For hygroscopic materials like fertilizers or pharmaceuticals, absolute moisture resistance is non-negotiable. VidePak employs lamination technologies to fuse kraft paper with aluminum foil or high-density polyethylene (HDPE), achieving water vapor transmission rates (WVTR) as low as 0.5 g/m²/day. This aligns with ASTM D7709 standards for moisture-sensitive cargo.
Key Data:
Feature | Specification |
---|---|
WVTR (Aluminum foil) | ≤0.5 g/m²/day |
Tensile Strength | 1,200–1,500 N/5 cm |
Temperature Resistance | -20°C to 80°C |
These bags are widely used in ammonium nitrate packaging, where moisture absorption can trigger dangerous chemical reactions.
2.3 Anti-Static Designs for Hazardous Environments
In industries handling flammable powders (e.g., coal, metal dust), static electricity poses explosion risks. VidePak integrates carbon-based conductive fibers into the PP weave, reducing surface resistivity to 10⁶–10⁸ Ω/sq—well below the 10¹² Ω/sq threshold for anti-static materials. A 2023 incident report from a German chemical plant confirmed that switching to anti-static kraft paper bags reduced electrostatic incidents by 92%.
2.4 Antimicrobial Designs for Food and Healthcare
Bacterial growth in moist environments is a major concern for perishables and medical supplies. VidePak’s silver-ion coated kraft paper inhibits 99.9% of E. coli and Staphylococcus aureus, as validated by ISO 22196 testing. This innovation is critical for organic food exporters complying with EU Regulation (EC) No 1935/2004 on food-contact materials.
3. VidePak’s Competitive Edge
With annual sales of $80 million and a 526-member team, VidePak combines scale with agility:
- Customization: 12-color rotary printing supports brand-specific designs.
- Sustainability: 100% recyclable PP and FSC-certified kraft paper align with ESG goals.
- Technology: Starlinger’s AD*Star loom systems enable precision weaving at 200 rpm, ensuring seam uniformity critical for moisture sealing.
Production Capacity Snapshot:
Equipment | Quantity | Output |
---|---|---|
Circular Looms | 100+ | 12M bags/month |
Extrusion Lines | 16 | 800 tons/month |
Lamination Machines | 30+ | 5M m²/month |
4. Market Applications and Case Studies
4.1 Agriculture: Ventilated Grain Bags
A Nigerian agro-export company reduced post-harvest losses by 25% using VidePak’s breathable bags, which feature 0.3 mm micro-perforations for airflow without compromising pest resistance.
4.2 Pharmaceuticals: Moisture-Blocked Vaccine Packaging
During the 2024 African vaccine rollout, VidePak’s HDPE-laminated bags maintained humidity levels below 10% RH, meeting WHO’s cold chain requirements.
5. FAQs
Q: What is the typical lead time for custom orders?
A: 15–20 days for designs under 10,000 units, leveraging VidePak’s in-house R&D and prototyping labs.
Q: How do anti-static bags compare in cost?
A: A 15–20% premium over standard bags, justified by hazard mitigation savings (e.g., $500k/year in reduced insurance claims for a U.S. coal distributor).
6. Conclusion
Kraft paper woven bags are evolving from generic packaging to engineered moisture-defense systems. VidePak’s fusion of Starlinger technology and sector-specific R&D exemplifies how innovation can transform a traditional industry. As climate change intensifies humidity challenges, these bags will remain pivotal in safeguarding global supply chains.
For further insights, explore how moisture-proof woven bags are revolutionizing logistics, or delve into the production techniques behind laminated designs.