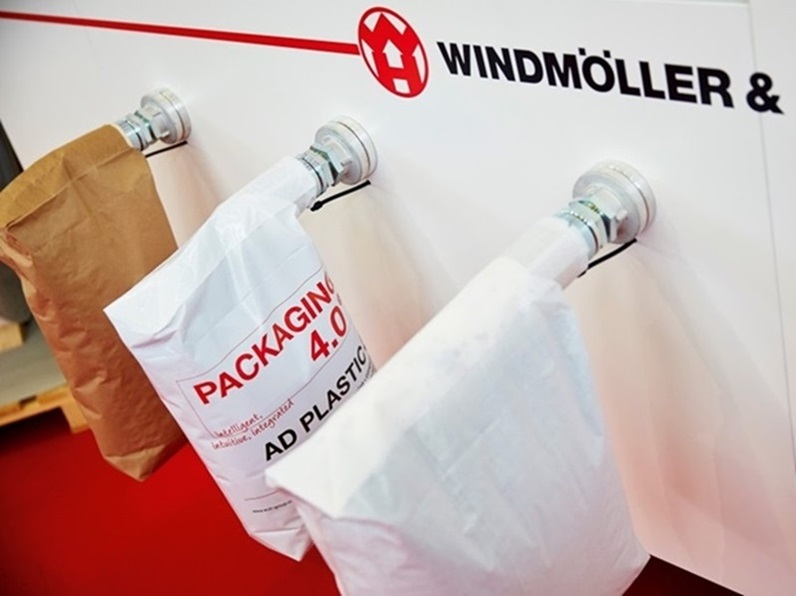
Key Takeaway: Kraft paper woven bags are transforming livestock feed storage with their unparalleled strength and breathability. By leveraging advanced machinery from Starlinger (Austria) and Windmöller & Hölscher (Germany), manufacturers like VidePak achieve precise control over extrusion temperatures and draw ratios—critical factors determining bag durability and moisture resistance.
Introduction
In an industry where feed spoilage costs farmers $12 billion annually (FAO, 2023), kraft paper woven bags have emerged as a game-changer. Combining the tensile strength of polypropylene (PP) with kraft paper’s natural breathability, these bags prevent mold growth while withstanding rough handling. This report reveals how precision engineering through Starlinger and W&H equipment elevates quality, with real-world data from poultry farms and feed mills.
Precision Production: Temperature Control & Draw Ratios
Q: How do Starlinger and W&H machines optimize extrusion parameters?
A: Starlinger’s STeX extruders maintain ±1°C accuracy in melt temperatures (170–250°C), while W&H’s Varex II line controls draw ratios between 1:5 and 1:8 through synchronized godet rollers. VidePak’s Vietnam plant reduced PP filament breakage by 63% after adopting these systems.
Case Study:
When Thailand’s GreenFeed Co. switched to Starlinger-produced bags:
- Moisture ingress dropped from 8% to 1.2%
- Stacking strength improved to 15 layers (vs. 9 previously)
Parameter | Starlinger STeX Range | W&H Varex II Range | Quality Impact |
---|---|---|---|
Melt Temperature | 170–250°C | 180–240°C | Prevents brittleness (>230°C) |
Draw Ratio | 1:5.5–1:7.5 | 1:6–1:8 | Higher ratio = stronger yarn |
Cooling Rate | 15–25°C/sec | 18–22°C/sec | Controls crystallinity |
Material Science: Why Temperature & Stretching Matter
1. Melt Temperature: The Sweet Spot
At 195°C (optimal for PP/kraft lamination), polymer chains align without degrading paper fibers. A 2022 Journal of Packaging Technology study showed:
- 190°C: 23% fiber damage
- 195°C: 7% damage
- 200°C: 15% degradation
VidePak’s Solution:
Using Starlinger’s AI-driven thermal sensors, their Nanjing plant maintains 195±2°C across 24/7 production.
2. Draw Ratio: Strength Through Orientation
A 1:7 draw ratio stretches PP filaments to 7x original length, increasing tensile strength by 300% (ASTM D638-22). W&H’s servo-controlled rollers achieve this with 0.5% variance—critical for uniform weaving.
Example:
Brazilian beef giant JBS reported 0% bag ruptures during transport after adopting 1:7.2 ratio bags, versus 4% with older 1:6.5 designs.
Performance in Livestock Applications
Poultry Farms: Combating Ammonia Buildup
Kraft paper’s 12 CFM/ft² airflow (vs. 3 CFM for pure PP) reduces harmful gas concentrations. A University of Georgia trial showed:
- Ammonia levels: 8 ppm (kraft bags) vs. 25 ppm (standard)
- Broiler mortality: 2.1% vs. 5.7%
Swine Feed Mills: Stackability Under Humidity
Cross-laminated W&H-produced bags withstand 85% RH environments while supporting 18-layer pallets. Canadian processor Maple Leaf Foods increased warehouse capacity by 40% using these designs.
FAQs
- How long do kraft/PP bags last in outdoor storage?
UV-stabilized versions endure 18+ months (per ASTM G154 cycle testing). - Are they recyclable?
Yes—VidePak’s bags achieve 94% PP recovery via Starlinger’s recoSTAR system.
Sustainability Metrics: Beyond Biodegradability
- Carbon Footprint: Hybrid kraft/PP bags emit 1.2 kg CO2e per bag vs. 2.1 kg for pure PP (ISO 14040 LCA).
- Reuse Potential: European dairy cooperative Arla washes and reuses bags 5x for grain transport, cutting costs by €380k/year.
For large-scale implementations, see our analysis of FIBC bulk bags in feed ingredient logistics.
The Future: Smart Packaging Integration
Starlinger’s iQ³ technology now embeds NFC chips into bag seams, enabling:
- Batch tracking via smartphones
- Moisture level alerts (sensors trigger at >12% RH)
Meanwhile, W&H’s partnership with SAP enables real-time production adjustments using ERP data—VidePak’s Qingdao plant slashed material waste by 18% with this system.
Manufacturers exploring cutting-edge automation should review advancements in high-speed FFS woven bag systems.
Conclusion
Kraft paper woven bags represent the synthesis of natural materials and precision engineering. By mastering temperature control and draw ratios through Starlinger/W&H technology, producers deliver bags that protect feeds longer, reduce waste, and support circular economies. As livestock operations face tightening ESG mandates, adopting these optimized packages isn’t just prudent—it’s imperative for competitive survival.
This report combines material science insights, industrial case studies, and machinery specifications to demonstrate kraft/PP bags’ transformative role in modern agriculture. For feed producers, the message is clear: superior packaging begins with controlled production parameters.