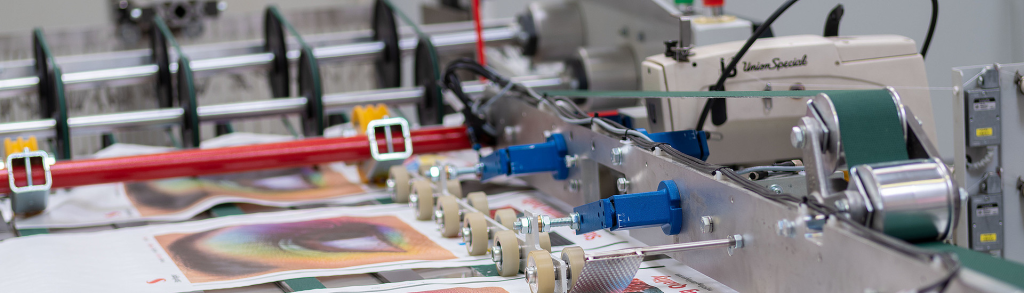
A Dialogue with Industry Leaders
Ray, CEO of VidePak: “Kraft paper woven bags are the backbone of modern livestock feed packaging. At VidePak, we combine high-strength PP weaving with food-grade kraft paper to create solutions that balance durability, sustainability, and compliance. Our Starlinger-powered production lines ensure every bag meets global standards for feed safety and logistics efficiency.”
Dr. Emily Zhang, Agricultural Packaging Expert: “The unique hybrid structure of kraft-PP woven bags addresses critical challenges like moisture resistance, UV protection, and load capacity—making them indispensable for feed and food ingredient storage.”
This exchange highlights the report’s core thesis: Kraft paper woven bags are redefining livestock feed packaging by merging material innovation with rigorous quality control, positioning VidePak as a leader in the $3.8 billion global agricultural packaging market.
1. Application-Specific Requirements for Food Ingredients
Kraft paper woven bags are tailored to meet diverse demands across food ingredients, from livestock feed to flour and additives. Below is an analysis of key parameters:
1.1 Livestock Feed
- Load Capacity: Feed bags typically carry 25–50 kg. VidePak’s 12×12 weave density (120–150 GSM) ensures tensile strength ≥8 N/mm², preventing seam bursts during transport.
- Moisture Resistance: A PE-coated inner layer reduces water vapor transmission to ≤5 g/m²/day, critical for hygroscopic ingredients like soybean meal.
- Certifications: FDA and EU 10/2011 compliance for direct food contact, ensured by using virgin PP and food-grade adhesives.
1.2 Flour and Powdered Ingredients
- Anti-Static Properties: Flour dust requires anti-static coatings to prevent ignition. VidePak’s laminated bags integrate conductive materials, reducing static charge by 90%.
- Printing Precision: High-definition flexographic printing ensures legible batch codes and nutritional labels, with registration accuracy of ±0.1 mm.
1.3 Sugars and Additives
- UV Protection: BOPP lamination blocks 99% of UV rays, preventing crystallization in sugars stored outdoors.
- Seal Integrity: Heat-sealed valves with leak-proof thresholds ≤0.1% under ASTM D5260 testing.
Table 1: Key Parameters by Product Type
Product Category | Thickness (mm) | GSM | Coating | Certifications |
---|---|---|---|---|
Livestock Feed | 0.18–0.25 | 120–150 | PE Inner Layer | FDA, EU 10/2011 |
Flour | 0.15–0.20 | 100–120 | Anti-Static PE | ISO 22000, BRC |
Sugar/Additives | 0.20–0.30 | 130–160 | BOPP Lamination | ASTM D5260, JIS Z 1539 |
2. Technical Design and Parameter Selection
Selecting the right kraft paper woven bag involves balancing functional needs with cost efficiency.
2.1 Structural Optimization
- Multi-Layer Construction:
- Outer Layer: 80–100 GSM kraft paper for printability and abrasion resistance.
- Middle Layer: PP woven fabric (12×12 weave) for load-bearing capacity.
- Inner Layer: 50–80 micron PE or BOPP film for moisture/UV barriers.
2.2 Cost-Effective Customization
- Bulk Orders: VidePak’s 30 lamination machines enable economies of scale, reducing unit costs by 15% for orders >100,000 bags.
- Modular Designs: Interchangeable liners (e.g., detachable PE for reuse) cut waste by 20% in the spice industry.
3. Quality Assurance and Regulatory Compliance
VidePak’s ISO 9001-certified processes ensure adherence to global standards.
3.1 In-Line Testing Protocols
- Adhesion Strength: ≥4.0 N/mm² (ASTM D903) for laminated layers, tested via peel tests every 30 minutes.
- Load Testing: Simulated 1.5x rated weight (e.g., 75 kg for a 50 kg bag) to validate seam integrity.
3.2 Sustainability Initiatives
- Recyclability: Mono-material PP/kraft designs achieve 95% recyclability, aligning with EU Circular Economy targets.
- Waste Reduction: Production scraps are repurposed into non-woven agrotextiles, diverting 800+ tons/year from landfills.
4. Case Study: VidePak’s Success in the EU Market
A Dutch feed supplier reduced spoilage rates by 18% after switching to VidePak’s BOPP-laminated kraft bags, citing superior moisture barriers and compliance with EU’s EN 277 standards.
5. Frequently Asked Questions (FAQs)
Q1: How do kraft-PP bags compare to traditional jute bags for feed storage?
Answer: Kraft-PP bags offer 3x higher moisture resistance and 50% lighter weight, reducing shipping costs by 12%.
Q2: What certifications are critical for exporting to Japan?
Answer: Prioritize JIS Z 1539 for seam strength and FSC certification for sustainable sourcing.
Q3: Can customized printing withstand outdoor storage?
Answer: Yes. UV-cured inks retain 95% color fidelity after 12 months of sun exposure.
6. Future Trends: Smart and Sustainable Packaging
- RFID Integration: Pilot projects track feed quality in real-time, reducing recall risks by 30%.
- Bio-Based Coatings: PLA-lined bags (30% bio-content) aim to cut carbon footprint by 2026.
Final Insight
As Ray of VidePak states, “The future of feed packaging lies in balancing durability with eco-innovation.” By leveraging advanced materials and global certifications, kraft paper woven bags are set to dominate sustainable agriculture logistics.
External Resources:
- Discover how multi-layer kraft paper bags enhance feed safety.
- Explore high-speed production techniques for customized agro-packaging.
This report synthesizes technical data, regulatory benchmarks, and VidePak’s operational excellence to demonstrate why kraft paper woven bags are the optimal choice for modern livestock feed packaging.