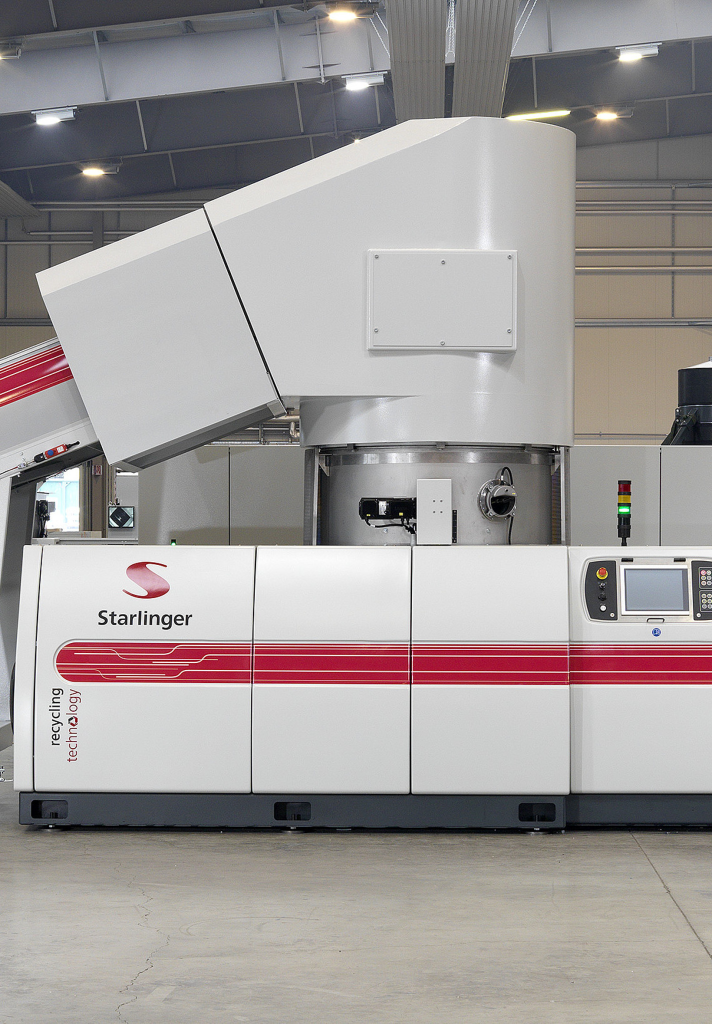
The demand for durable, versatile, and eco-friendly packaging solutions has propelled laminated woven bags to the forefront of the global packaging industry. These bags, produced using cutting-edge multi-layered co-extrusion blown film technology, are essential for meeting the stringent requirements of industries such as agriculture, construction, and logistics. This report explores their production process, advantages, and relevance in today’s market.
Key Manufacturing Processes: Foundations of Quality
The exceptional performance of laminated woven bags stems from three pivotal manufacturing stages: extrusion, weaving, and lamination. Each stage contributes directly to the durability and versatility of the final product.
1. Extrusion: Laying the Foundation for Strength
During extrusion, polypropylene (PP) resin is melted and drawn through precision-engineered dies to create thin, consistent filaments. These filaments serve as the backbone of the woven fabric, offering a balance of strength and flexibility. High-quality PP resin ensures uniformity, preventing weak points in the fabric. The precision in this step is crucial to achieving high tensile strength and resistance to wear.
2. Weaving: Building Structural Integrity
The extruded filaments are interwoven using advanced circular looms to create the fabric. The density of the weave, measured in picks per inch (PPI), determines the bag’s load-bearing capacity. A tightly woven fabric enhances resistance to tearing and deformation under stress, which is essential for heavy-duty applications such as industrial powders and fertilizers.
3. Lamination: Adding Protection and Versatility
Lamination involves bonding a multi-layered co-extrusion film to the woven fabric. This process uses a combination of heat and pressure to create a seamless protective layer. The lamination film provides moisture resistance, UV protection, and a smooth surface for high-quality printing. The durability of this layer ensures the bags can withstand harsh environmental conditions while preserving their contents.
Process | Impact on Quality |
---|---|
Extrusion | Produces strong, consistent filaments with high tensile strength. |
Weaving | Ensures structural integrity and resistance to tearing. |
Lamination | Provides moisture resistance, UV protection, and a printable surface. |
Advantages of Multi-Layered Co-Extrusion Technology
The multi-layered co-extrusion process integrates various polymers, each chosen for its specific properties. This advanced technology allows for:
- Moisture and UV Protection: Essential for safeguarding agricultural products and construction materials from degradation.
- Customizable Surfaces: Options for matte or glossy finishes cater to different branding and aesthetic needs.
- Enhanced Flexibility and Strength: The multi-layered design absorbs impact and resists punctures, ensuring reliable performance in transport and storage.
Responding to Market Demands
The versatility and durability of laminated woven bags make them indispensable across industries. Their increasing adoption is driven by the following factors:
1. Sustainability
Laminated woven bags are recyclable, aligning with global environmental regulations such as the European Union’s REACH standards. Their longevity reduces waste, making them an eco-friendly alternative to single-use plastics.
2. Industrial Utility
From cement to grains, these bags handle a wide range of products. Their ability to endure heavy loads without tearing ensures they remain a staple in logistics and supply chains.
3. Branding Opportunities
The smooth laminated surface supports advanced printing technologies from industry leaders like Starlinger and W&H. High-resolution printing allows for vibrant and precise designs, enhancing brand visibility.
Innovations Driving the Industry Forward
The laminated woven bag sector continues to evolve with technological advancements:
- Anti-Slip Coatings: These enhance stackability, improving storage and transportation efficiency.
- Enhanced Printing Technology: Multi-color, high-resolution printing facilitates detailed branding, increasing market appeal.
- Reinforced Lamination: New materials in lamination films provide greater resistance to extreme conditions.
FAQs
Q: What makes laminated woven bags superior to other packaging solutions?
Their combination of durability, moisture resistance, and customizability makes them ideal for industrial and agricultural use.
Q: How do these bags contribute to sustainability?
Recyclable materials and long product life reduce environmental impact, meeting global eco-friendly standards.
Q: Are they customizable for branding?
Yes, high-resolution printing enables vibrant and detailed designs tailored to specific business needs.
Q: What industries benefit most from laminated woven bags?
Industries such as agriculture, construction, and chemicals rely on these bags for their durability and adaptability.
Specifications Table: Laminated Woven Bags
Parameter | Specification |
---|---|
Material | Polypropylene woven fabric with laminated film |
Strength | Tensile strength up to 75 kg |
Finish | Matte or glossy |
Custom Options | Multi-color printing, UV-resistant coatings |
Applications | Agriculture, construction, industrial packaging |
External References
- Learn about Laminated Woven Bags and the Multi-Layered Co-Extrusion Blown Film Process.
- Explore Industrial Woven Packaging Bags Aligning with Policies and ESG Standards.
Conclusion
Laminated woven bags, produced through precision-driven processes like extrusion, weaving, and lamination, represent a pinnacle of innovation in packaging. Their superior durability, flexibility, and environmental compliance meet the complex demands of global industries. As markets evolve, technologies such as multi-layered co-extrusion ensure that these bags remain not only a practical choice but also a forward-thinking solution for businesses worldwide.