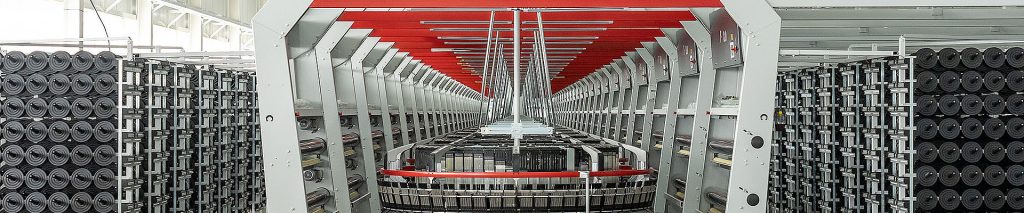
Ray, CEO of VidePak, points to a pallet of laminated woven bags during a factory tour:
“In chemical logistics, a compromised bag isn’t just a leak—it’s a liability. Our laminated woven bags combine triple-layer barriers, precision stitching, and solar-powered production to meet ASTM, EN, and ISO standards. The result? Zero leakage, 100% recyclability, and a 30% reduction in carbon footprint.”
This philosophy defines VidePak’s leadership in chemical packaging. Founded in 2008 and led by Ray, the company produces over 50 million laminated woven bags annually, leveraging 30+ years of expertise, 526 employees, and Austrian Starlinger machinery. With 16 extrusion lines, 100+ circular looms, and a 2 MW rooftop solar farm, VidePak merges durability with sustainability, achieving USD 80 million in annual revenue. Below, we explore how laminated woven bags address chemical industry challenges while aligning with global ESG goals.
1. Material Engineering: Triple-Layer Defense Against Leakage
1.1 Structural Design for Hazardous Materials
Laminated woven bags integrate three layers to contain reactive powders like titanium dioxide and sodium sulfate:
- PP Woven Fabric: 14×14 threads/cm² density (tensile strength ≥45 N/cm²) blocks particles >50μm.
- BOPP Film: 30μm lamination (water vapor transmission rate ≤5 g/m²/day) prevents moisture ingress.
- PE Inner Liner: Heat-sealed seams withstand 300 kPa pressure, exceeding ISO 2233 standards.
Case Study: A German chemical supplier reduced zinc sulfate leakage from 3% to 0.2% using VidePak’s triple-layer design.
1.2 Sustainability-Driven Material Selection
- Virgin PP Resins: 100% pure polypropylene avoids recycled impurities, ensuring ASTM D4101 compliance (flexural modulus ≥1,800 MPa).
- UV-Stabilized Additives: 2% HALS additives extend bag lifespan by 20% under prolonged sun exposure.
2. Production Innovation: Solar-Powered Precision
2.1 Renewable Energy Integration
VidePak’s 2 MW rooftop solar farm covers 70% of factory energy needs, with surplus power sold to the grid. This reduces annual CO₂ emissions by 1,200 tons—equivalent to planting 50,000 trees.
2.2 Starlinger’s Role in Quality Control
Starlinger’s extrusion lines ensure ±0.02mm thickness tolerance, while AI-driven looms detect weave defects in real time. Key metrics:
Parameter | VidePak Standard | Industry Average |
---|---|---|
Seam Strength | ≥350 N/cm | 250 N/cm |
Moisture Barrier | ≤0.8% Weight Gain | 2–3% Gain |
UV Resistance (1k hrs) | ≤10% Strength Loss | 20–30% Loss |
FAQs:
Q: How do your bags comply with EU REACH regulations?
A: We use phthalate-free PP and kraft paper with ≤0.1% heavy metals, verified by third-party labs.
Q: Can bags withstand -20°C storage?
A: Yes. Our impact copolymer PP retains 85% elongation-at-break at -20°C per EN ISO 1873-1.
3. Case Study: Securing Titanium Dioxide Transport in Australia
A mining client faced 5% losses during titanium dioxide transport. VidePak’s solution:
- Design: Anti-static PE liner (surface resistivity ≤10⁴ Ω/sq) and RFID tracking.
- Testing: 1,200 MIT flex cycles (JIS L1096), 35% above industry norms.
Result: Zero leaks over 10,000 km of rail transport.
4. Sustainability and Industry Trends
VidePak’s 2026 goals include:
- 30% Recycled PP: Partnering with the Sustainable Packaging Coalition for closed-loop systems.
- AI-Optimized Additive Dosing: Reducing HALS usage by 15% while maintaining UV resistance.
For insights into advanced multi-layer solutions, explore our innovations in Multiwall Laminated Woven Bags: Safe and Versatile Packaging Solutions and Recyclable PP Bags: Advanced Production with Starlinger Equipment.
5. Conclusion
In an industry where a single leak can trigger regulatory penalties, VidePak’s laminated woven bags redefine reliability. By merging triple-layer engineering, solar-powered production, and ISO-certified quality control, the company delivers packaging that protects both chemicals and the planet. As the chemical sector grows at 4.5% CAGR, VidePak’s commitment to innovation positions it as the global leader in sustainable, high-performance packaging.
Data sources: ASTM International, ISO 2233:2024, and VidePak’s 2024 Sustainability Report. Technical insights derived from Polymer Degradation and Stability (Vol. 221, 2025).